Which material is safest for crane rope?
07 March 2022
Wire or fibre, ropes are key for a crane’s performance. Niamh Marriott reports.
When it comes to rope, the debate continues, which is better, safer, more efficient – steel wire or synthetic fibre rope?
Arguing for synthetic material is James Gregory, president of digging and rigging at Samson Rope. He says, “Wire rope has a mind of its own when you’re handling it. Anything we can do to enhance our strong safety culture and jobs easier and more efficient for the riggers and crews is valuable.”
Samson’s K-100 is an alternative to steel wire hoist ropes and is made of synthetic fibre. The company says it’s just as strong but weighs 80 per cent less than wire. Being lighter means “easier handling without the danger of injury from broken strands and results in quicker reeving operations, while the torque-neutral braided construction reduces load spin and cabling. Kinking and birdcaging are eliminated, and, while rare, diving on the drum is easily remedied with no adverse effect on the rope.” It’s also easier and quicker to inspect, the company says.
The company explains that K-100 doesn’t require any lubrication so is more environmentally efficient and that rope inspection is simplified and quicker. In early 2021 Sampson began to offer several of its products, including the AmSteel-Blue, AmSteel-X, Saturn-12, EverSteel-X, and Turbo-RC ropes with the option of containing bio-sourced fibre.
Appropriate equipment
Synthetic rope needs to be stored and operated with appropriate equipment. Oklahoma, USA-based Braden has added a new anchoring system for its TR 20 recovery winches, which the company says will ensure secure installation of synthetic rope for winching applications.
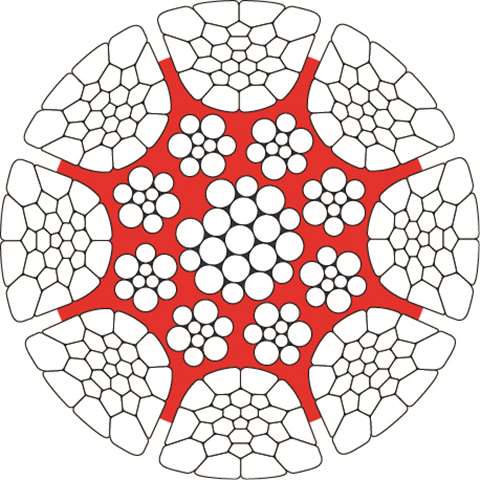
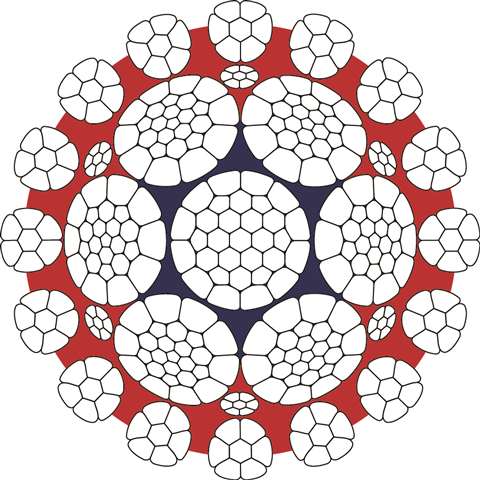
“Synthetic rope continues to grow in popularity for utility, towing and recovery, construction, military and other applications,” says a Braden spokesperson. “Replacing traditional steel cables can drastically reduce the overall weight of any towing or utility vehicle, particularly those with multiple winches. Abrasion-resistant and easy to inspect, synthetic rope is torque-neutral, which means it will not twist and is much easier to handle.”
The company’s latest product, the Synthetic Rope Anchor (PN 113316) works with 12 mm and 16 mm synthetic rope and can provide pulling power that has up to 40 per cent less weight compared to steel cable.
Installation is designed to be straightforward says Braden. To use the anchor, an eye must be spliced into the rope and inserted through the smaller opening of the wedge pocket on the drum. Install the anchor in the eye, then pull the rope until the anchor is fully seated in the pocket and the anchor will secure the rope in the drum.
“Synthetic rope should be installed on a new winch drum with all burrs and sharp edges removed. The rope should be spooled onto the drum while under tension,” continues the spokesperson. “Synthetic rope should not be installed on drums that have previously had wire rope installed.”
Fibre action
The industry is experimenting with fibre rope and embracing its benefits. The new heavy lift ship crane type HLC 150.000-3000 from Liebherr, which will have a lifting capacity of 3,000 tonnes, will rely on several HyperTen fibre ropes from Teufelberger.
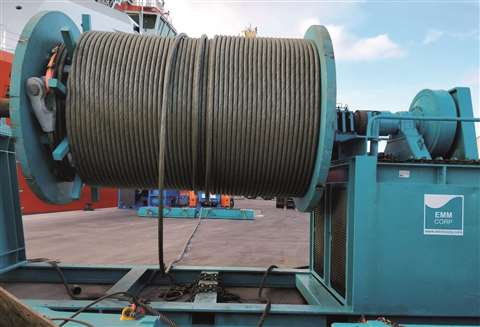
Liebherr opted for several 34 and 50 mm HyperTen fibre ropes for the heavy lift ship crane. Teufelberger says the weight of the HyperTen is so low that the rope even floats in the water.
For attaching loads on deck, Teufelberger says the advantages of a lightweight fibre rope compared to a steel wire rope are “obvious” – namely the weight difference. The 50 mm HyperTen weighs only 1.4 kg/m against a comparable steel wire rope weighing 11.5 kg/m. The rope also has a long service life, according to the company.
Björn Ernst, head of the fibre rope development department, describes the challenges faced during development,“Apart from adapting the rope diameter and the respective diameter tolerances to the winch geometry, it was necessary to develop a load-side rope end termination that can be used in combination with the standard wire rope pouch sockets in the market. The challenge was to develop a Fast Connector Socket (FCS) for a high-strength fibre rope. The company’s FCS for fibre ropes has an identical external appearance to one for steel wire rope and is therefore compatible.
Wire demands
Steel wire rope continues to be dominant. Wire rope manufacturer Usha Martin Group Companies says the demand for its product is strong. The company has a wide range of combined capabilities from manufacturing to installations, as well as bespoke products and turnkey solutions. Recently, a client required a replacement main hoist rope for its vessel’s onboard knuckle boom crane, and the company handled the project from start to completion.
Together, Usha Martin Italia (the group’s global design centre) and Brunton Shaw, a UK-based group manufacturing facility, designed and manufactured a 3,300 metre length of OceanMax35 56 mm compacted non-rotating steel wire rope.
Once the rope had been produced, EMM Corp, an Aberdeen, Scotland-based group service centre, worked alongside the hauliers to co-ordinate the mobilisation of the 51 tonne reel from the manufacturing facility to the port side in the North East of Scotland, where EMM Corp’s engineers were waiting to begin the installation onto the client’s vessel. EMM Corp supplied the spooling winch and handled all craneage-related operations. Overall management was overseen by Netherlands-based De Ruiter Staalkabel.
Rope safety
“Regardless of whether it is a huge lattice boom crawler crane for setting up wind turbines, a crane for handling containers or an indoor crane in a paper factory, they all have one thing in common: the wire rope, which serves as a lifting device for the load to be moved,” says a Casar spokesperson, part of WireCo. “The rope has always been a critical crane component, the importance of which has increased due to the development on the crane market.”
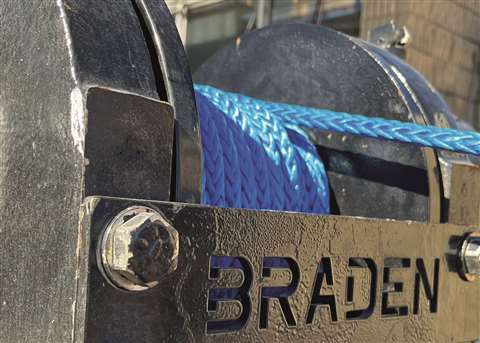
The company believes the design of a rope can maximise safety.
“Safety and reliability have top priority in crane operations, which is why Casar ropes are designed and calculated in such a way that they show their discard status on the rope surface in good time, so the operator knows when to change the rope.”
Casar has researched and tested various rope properties, including breaking strength, turning behaviour, efficiency, flexibility and diameter reduction under load. This led to the development of Doublefit, made from compressed steel strands. The rope has been used as the hoist rope on the Manitowoc MLC 650 crawler cranes for the last few years.
“By compressing the strands and hammering both the heart rope and the slammed rope, a very round and smooth surface is obtained,” explains a spokesperson.
A luffing rope, used to alter the angle of the boom, demands use of a different type of rope. For this requirement Casar offers its Parafit rope. The company says it has “excellent spooling behaviour and drum-crushing resistance.” The smooth surface with less indentation means lower abrasion and less damage, the company says.
Spanish crane manufacturer Jaso used the Doublefit and Parafit on its J780PA, a large luffing jib tower crane. Bosko Mujika, Jaso Tower Cranes R&D manager, comments, “We will continue to use Doublefit and Parafit on our tower cranes, as the swaged surface ensures optimal spooling, high rotation resistance, and a long and safe lifespan. The breaking strength is impressive.”
Safety is at the forefront of both synthetic and wire rope, and weighing up the choices, it seems the industry prefers to have several reliable options.
STAY CONNECTED
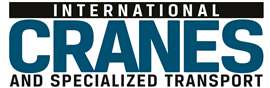
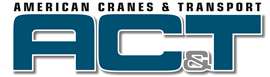
Receive the information you need when you need it through our world-leading magazines, newsletters and daily briefings.
CONNECT WITH THE TEAM
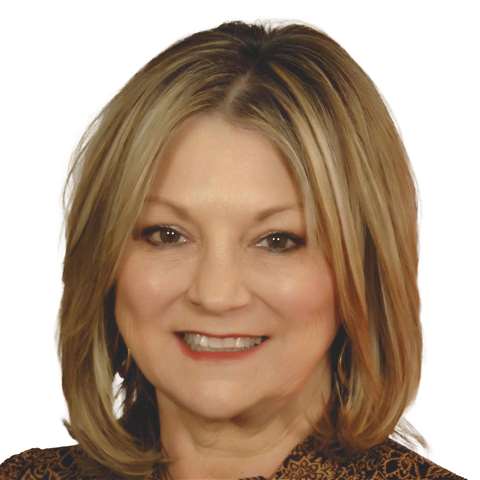
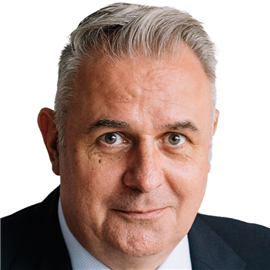
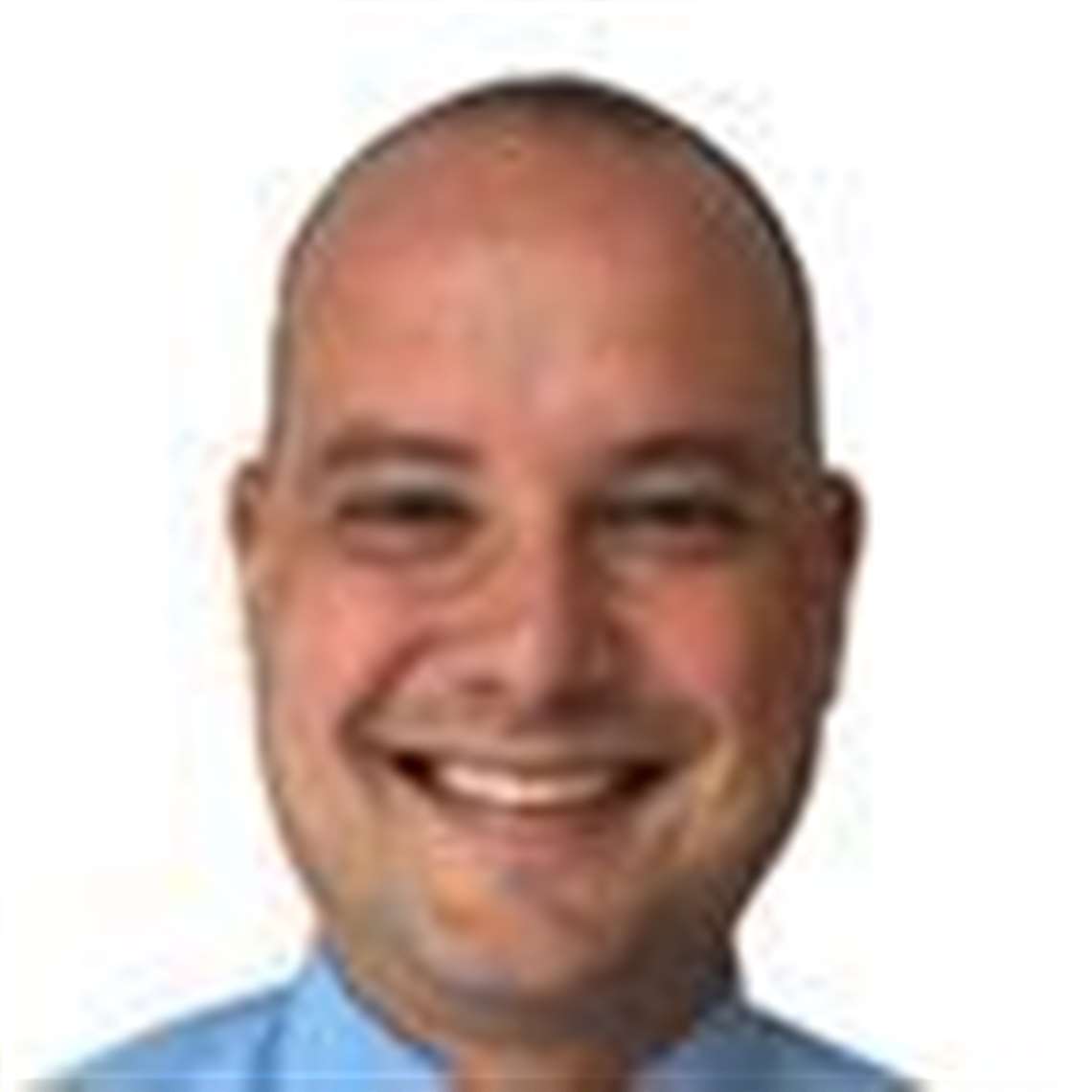
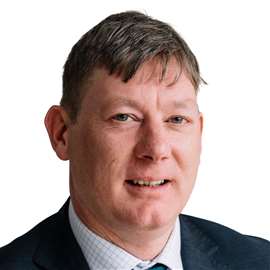