Automatisch von KI übersetzt, Original lesen
Hebevorgänge in Offshore-Windparks profitieren vom Ringkran
04 Dezember 2023
Eine der größten Herausforderungen auf hoher See besteht darin, dass die Flut – die den Bau von Windparks zum Stillstand bringen kann – nicht aufzuhalten ist, es sei denn, man setzt einen Schwerlast-Ringkran ein. Alex Dahm berichtet.
Weltweit werden immer mehr Offshore-Windenergieprojekte gebaut, wobei der Schwerpunkt zunehmend auf der Betriebseffizienz liegt.
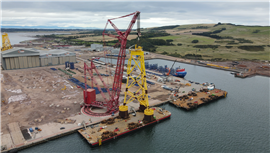
Ein wichtiger Aspekt bei den Hebearbeiten am Kai ist, dass der Wasserstand alle sechs Stunden durch die Gezeiten um bis zu vier Meter schwanken kann. Dies ist insbesondere in Großbritannien der Fall, wo der extreme Tidenhub beim Be- und Entladen von Schiffen schwer zu bewältigen ist. Er ist zu groß, um ihn durch Ballastierung auszugleichen. Das Be- und Entladen von beispielsweise großen Jackets ist bei extremen Tidenhubs nicht möglich. Dies führt zu Projektverzögerungen und ungenutzten Transportschiffen.
Die Global Energy Group im schottischen Hafen Nigg hatte mit diesem Problem beim Bau des Offshore-Windparks Seagreen zu kämpfen. Der Auftragnehmer Mammoet schlug den Einsatz eines seiner Schwerlast-Ringkrane vor. Am Kai aufgestellt, ermöglicht dies gezeitenunabhängige Hebevorgänge und sorgt für eine optimale Auslastung des Installationsschiffs.
Seagreen ist der tiefste Offshore-Windpark der Welt mit festem Boden, was einer Fundamenthöhe von 95 Metern entspricht. Die 114 Windturbinenfundamente tragen sehr große 10-MW-Windturbinen von Vestas.
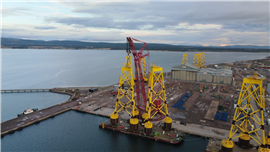
Der Ringkran wird anstelle der herkömmlichen Methode verwendet, bei der die Fundamente und andere Komponenten auf mehreren Achslinien eines selbstangetriebenen modularen Transporters auf ein Schiff und von diesem herunter transportiert werden, das für einen reibungslosen Übergang zwischen Dock und Schiff ballastiert ist.
Neben der Ballastreichweite ergeben sich bei diesem Ansatz auch andere Probleme. Wenn selbstangetriebene modulare Transporter (SPMT) auf das Schiff gefahren und wieder heruntergefahren werden müssen, muss Decksfläche ständig freigehalten und verfügbar sein. Der Platz für die Lagerung von Komponenten ist dann eingeschränkt.
Größere und stärkere Lastkähne können die Lösung sein, allerdings ist die Auswahl an geeigneten Schiffen eingeschränkt. Dies kann zu Projektverzögerungen führen.
Da die Mammoet-Ingenieure seit 2018 an dem Projekt beteiligt sind und eine enge Arbeitsbeziehung mit dem Kunden Global Energy Group pflegen, konnten sie über den Umfang des Schwertransports hinausblicken.
Doppelte Zeit
Die Lösung bestand darin, den Einsatz von SPMT mit dem Ringkran PTC 210 DS zu kombinieren. Dadurch gab es keine Verzögerungen mehr, die durch das Warten auf die Gezeiten verursacht wurden. Eine solche SPMT-Beladung dauerte fünf Stunden, sodass nur ein Vorgang pro Schicht durchgeführt werden konnte. Mit dem Kran entfällt dies, da das Deck des Lastkahns nicht mehr auf gleicher Höhe mit dem Kai bleiben muss. Der Kran kann seine Hebevorgänge trotzdem durchführen, und zwar zwei pro Schicht.
Durch den Einsatz von SPMT und dem riesigen Kran konnten zwei Vorgänge gleichzeitig ausgeführt werden. Während der Kran Jackets auf ein Schiff lud, konnte das SPMT andere entladen.
Die Jackets konnten früher als erforderlich an den Kai gebracht werden, sodass sie vom Kran abgeholt werden konnten. Dies trug dazu bei, die Wartezeit im Hafen des Schiffes zu verkürzen.
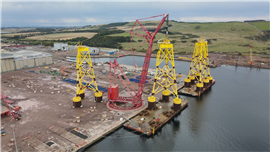
Oliver Smith, technischer Vertriebsleiter bei Mammoet UK, kommentierte das Projekt wie folgt: „Wie immer ist die Kosteneffizienz ein wichtiger Faktor, wenn sich ein Unternehmen für ein Projekt dieser Größenordnung entscheidet. Wir waren schon Jahre im Voraus in dieses Projekt involviert – lange bevor einige Details ans Licht kamen. Erst später mussten wir die Situation neu bewerten und vom reinen SPMT-Betrieb abrücken.“
Smith sagte, alles sei wie geplant verlaufen und das Feedback der Global Energy Group und anderer Interessengruppen sei positiv gewesen. „Wir wussten, dass diese Methode sicher, flexibel und kostengünstiger ist als SPMT. Jetzt können wir sie der gesamten Branche vorstellen, damit sie als Vorlage dafür dienen kann, wie Offshore-Windinfrastruktur schneller und kostengünstiger ins Wasser gebracht werden kann, insbesondere bei hohen Gezeitenschwankungen.“
BLEIBEN SIE VERBUNDEN
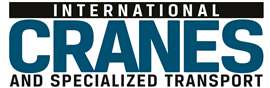
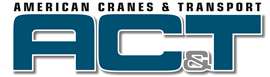
Erhalten Sie die Informationen, die Sie benötigen, genau dann, wenn Sie sie brauchen – über unsere weltweit führenden Magazine, Newsletter und täglichen Briefings.
KONTAKTIEREN SIE DAS TEAM
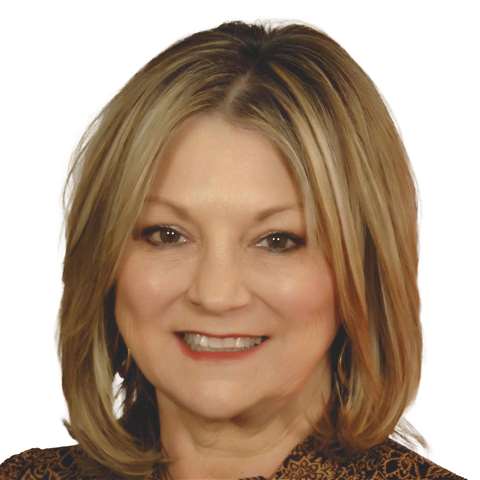
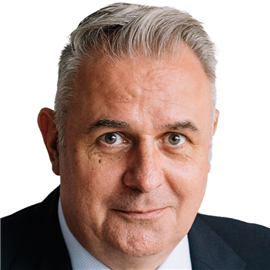
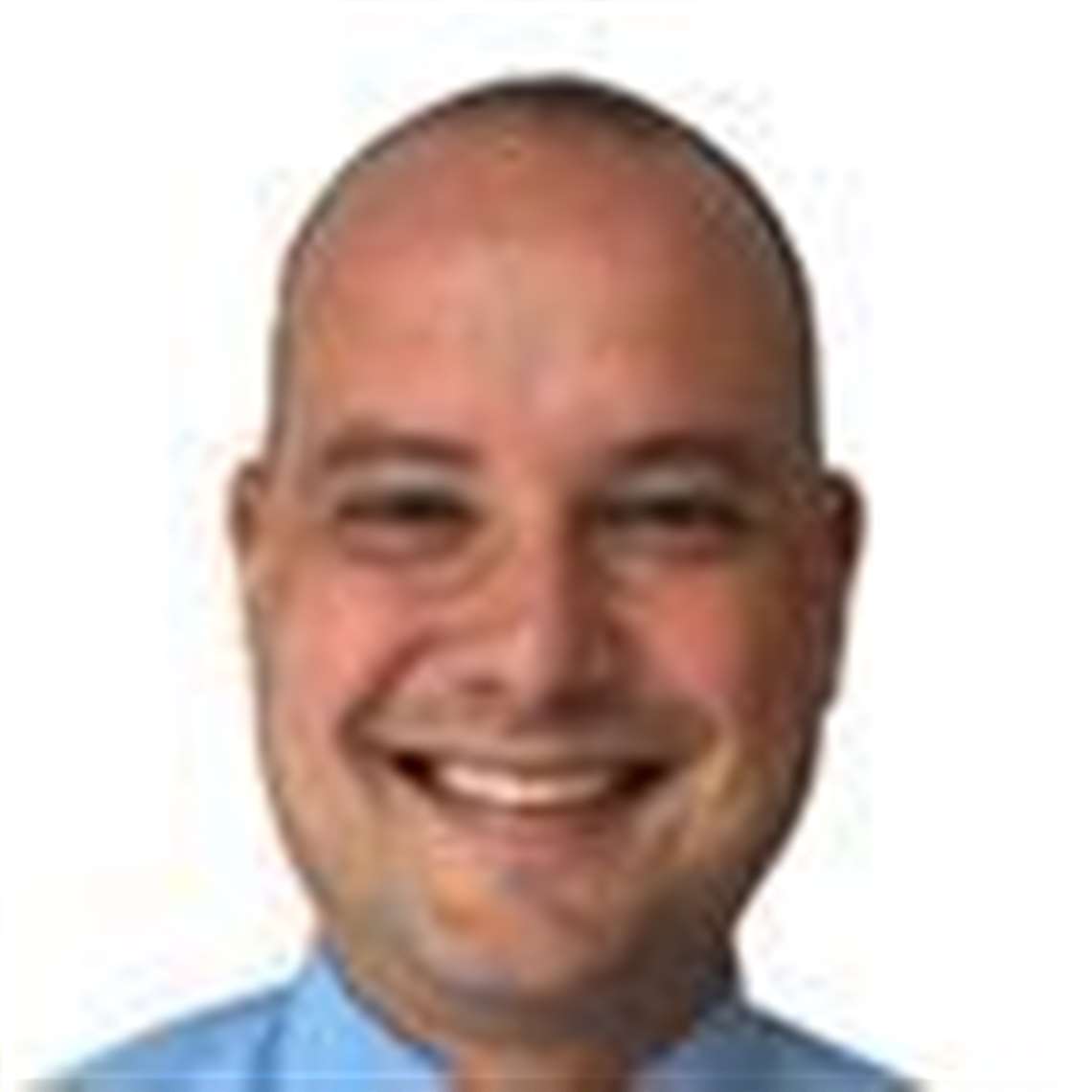
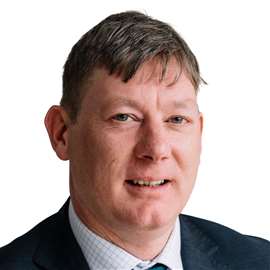