Read this article in French German Italian Portuguese Spanish
Offshore wind farm lifts benefit from ring crane
04 December 2023
One of the biggest offshore challenges is that nothing can stop a tide – which can bring a halt to work on wind farm construction projects – unless you use a super heavy lift ring crane. Alex Dahm reports.
Offshore wind energy construction projects are ramping up all over the world, increasingly putting a focus on operational efficiency.
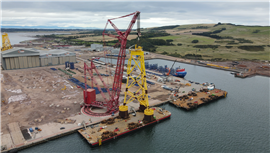
A key consideration for the lifting work at the quayside is that there can be tidal water level changes of as much as four metres, every six hours. This is the case around the UK where the extreme tidal range is difficult to contend with when loading and unloading vessels. It is too much to compensate for using ballasting. Load-ins and load-outs of, for example, large jackets can’t be done at the extremes of the tidal range. This means project delays and idle transport vessels.
Global Energy Group at the Port of Nigg in Scotland had this issue to contend with for the Seagreen Offshore Wind Farm. Contractor Mammoet suggested deployment of one of its super heavy lift ring cranes. Erected at the quayside this would allow lifts to be made irrespective of the tide and to keep the installation vessel as busy as possible.
Seagreen is the deepest fixed bottom offshore wind farm in the world which means its foundations are 95 metres tall. Its 114 wind turbine foundations carry very large, 10 MW, Vestas wind turbines.
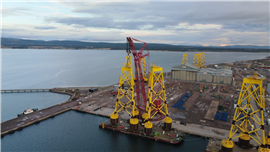
The ring crane is used instead of the conventional approach of carrying the foundations and other components on multiple axle lines of self propelled modular transporter on and off a vessel that is ballasted for a smooth transition between dock and vessel.
Issues other than the ballasting range are also inherent with this approach. Where self propelled modular transporter (SPMT) has to be driven on and off the barge, deck space needs to be kept permanently clear and available. Space for component storage is then restricted.
Larger and stronger barges can be the solution but there is a narrower choice of suitable vessels. It can lead to project delays.
Having been involved with the project since 2018 and sharing a close working relationship with its customer Global Energy Group, Mammoet engineers could look further than the heavy transport scope.
Double time
The solution was to combine the use of SPMT with the PTC 210 DS ring crane. It meant no more delays caused by waiting for tides. An SPMT load out like this would need five hours so only one operation could be done per shift. With the crane this no longer applies as the barge deck no longer needs to remain level with the quay. The crane can still make its lift regardless, to the tune of two per shift.
Using SPMT and the giant crane allowed two operations to run at the same time. As the crane loaded jackets onto a vessel the SPMT could be unloading others.
Earlier than required the jackets could be brought to the quayside ready for the crane to pick them, helping to reduce waiting time when the vessel is in port.
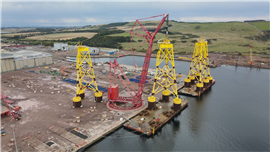
Commenting on the project Oliver Smith, Mammoet UK technical sales manager, said, “As ever, when an organisation is deciding on a project of this scale, cost-efficiency is always an important factor. We were involved with this project years in advance – well before some of the full details came to light. It was only further down the line that we needed to reassess the situation and move away from SPMT-only operations.”
Smith said everything proceeded as planned and that the feedback from Global Energy Group and other stakeholders was positive. “We knew this method was safe, flexible and more cost-effective than using SPMT. Now we can share it with the wider industry so it can serve as a template for how to get offshore wind infrastructure in the water faster and more cost-efficiently; especially where tidal variances are high.”
STAY CONNECTED
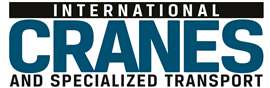
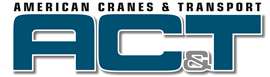
Receive the information you need when you need it through our world-leading magazines, newsletters and daily briefings.
CONNECT WITH THE TEAM
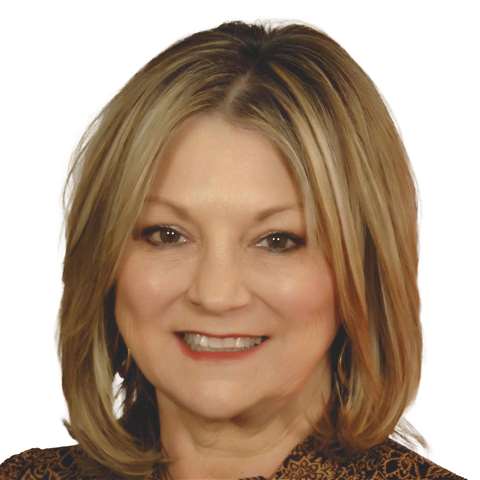
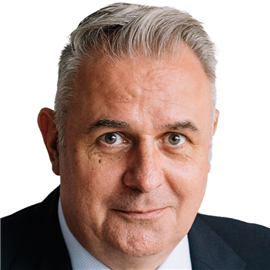
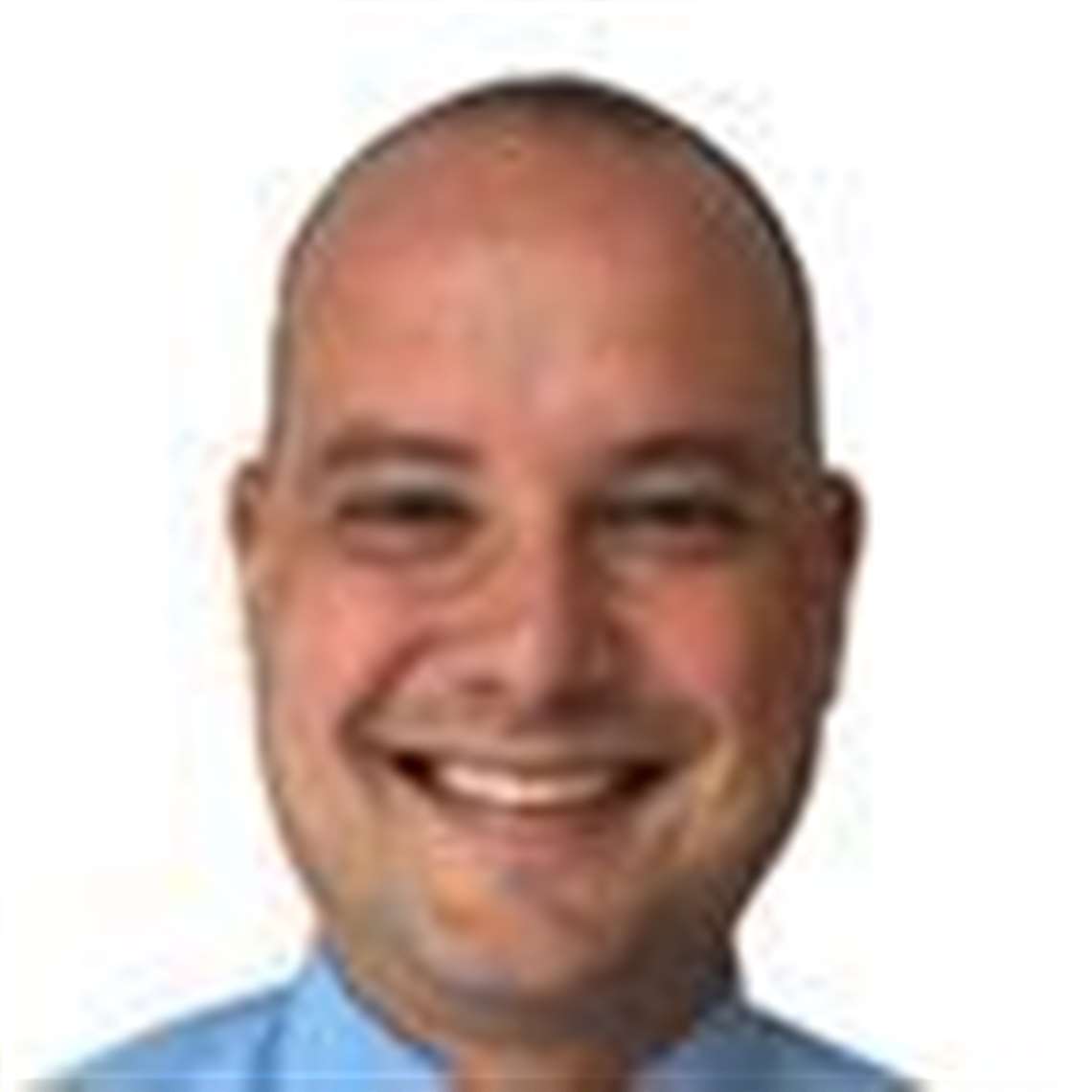
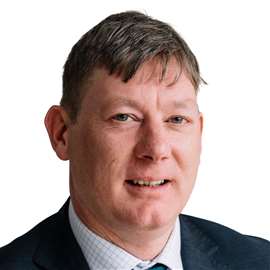