Automatisch von KI übersetzt, Original lesen
INTERVIEW: Der Game Changer, der die zukünftige Nachfrage nach Crawlern erfüllt
28 Februar 2024
ICST sprach exklusiv mit Hendrik Sanders, dem leitenden Forschungs- und Entwicklungsingenieur und Raupenkranexperten von Sarens, über die Deckung der zukünftigen Nachfrage nach Raupenkranen.
Der internationale Spezialist für Schwerlast- und Transportarbeiten Sarens setzt mit seinen stetig wachsenden Hebekapazitäten und Transportleistungen auf Innovationen. Immer schwerere Lasten müssen gehoben werden, und die Kranhersteller mussten sich anpassen und immer größere Modelle produzieren, um diesen enormen Projektanforderungen gerecht zu werden.
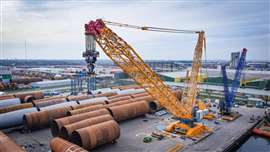
Sarens stellt sich dieser Herausforderung weiterhin und erweitert seine Flotte aus über 1500 Kränen, 3100 Achslinien und einer Reihe von Riesenkränen regelmäßig um Kräne mit hoher Tragkraft.
Anfang 2023 erhielt Sarens das erste Exemplar des neuen Raupenkrans LR 12500-1.0 von Liebherr mit einer Tragkraft von 2.500 Tonnen. Sarens nannte seinen neuen Raupenkran Straffen Hendrik, nach seinem langjährigen Mitarbeiter Hendrik Sanders.
Rostock in Deutschland war der erste Einsatzort des LR 12500-1.0 für Sarens‘ Kunden Van Oord. Dort hob er 50 Monopile-Fundamente für Offshore-Windkraftanlagen. Jedes hatte einen Durchmesser von bis zu neun Metern und eine Länge von bis zu 90 Metern. Die Fundamente wurden im Tandem mit einem 800-Tonnen-Gittermast-Raupenkran vom Typ Liebherr LR 1800-1.0 ins Wasser gehoben.
Derzeit befindet sich Sarens in den letzten Verhandlungen mit Liebherr über den Erwerb eines zweiten LR 12500-1.0 zur Lieferung im Jahr 2024.
Wie begann Ihre Reise bei Sarens?
HS: Ich arbeite seit 34 Jahren bei Sarens und war die meiste Zeit davon im Krangeschäft tätig, insbesondere in der Abteilung Gittermasten und mit Raupenkranen.
Im ersten Jahr war ich Baustellenleiter, danach war ich mehrere Jahre lang Baustellenmanager. 1993 wechselte ich ins Büro und begann in der Konstruktionsabteilung. Das machte ich sieben Jahre lang und wechselte dann in den operativen Bereich der Gittermastkranabteilung. Zuvor hatten wir eine gemeinsame Planungsabteilung für Gittermast- und Teleskopkrane. Als das Unternehmen immer größer wurde, wurde es einfacher, die Abteilungen aufzuteilen, da es zu kompliziert war, sie zusammenzuhalten – Gittermastkrane sind eher ein weltweites Unterfangen, während das Teleskopsortiment besser auf lokaler oder regionaler Ebene verwaltet wird. Also arbeitete ich mehrere Jahre in der Gittermastabteilung und bin jetzt in der Forschungs- und Entwicklungsabteilung tätig. Das bedeutet, dass ich ein Bindeglied zwischen Sarens und den Kranherstellern sein kann.
Ich versuche, von den Herstellern unsere Wünsche und Bedürfnisse zu erfahren und arbeite mit ihnen zusammen, um die Anforderungen unserer neuesten Krane zu erfüllen. Kranhersteller konstruieren in der Regel keine Krane für nur einen Kunden und möchten, dass ihre Krane weltweit Anklang finden. Ich versuche jedoch, unsere Wünsche und die gemeinsamen Möglichkeiten zu demonstrieren.
Ich arbeite hauptsächlich mit europäischen Herstellern zusammen, obwohl wir natürlich auch chinesische Krane wie Sany, XCMG und Zoomlion in unserer Flotte haben. Die chinesische Fertigung hat im Laufe der Jahre große Fortschritte gemacht, und sie bringt nun selbst einige echte Innovationen hervor. Daher war es für mich sehr interessant, den Fortschritt zu verfolgen und zu beobachten.
Was ist der Hauptunterschied zwischen den chinesischen und den europäischen Herstellern?
HS: Chinesische Hersteller testen verschiedene Innovationen. Zum Beispiel einen Mini-Superlift für die Auslegermontage, der in die Kranrückseite integriert ist. Das ist praktisch, denn bei Gittermastkranen ist die Auslegermontage eine der größten Herausforderungen. Wenn der Hauptausleger ohne Derrick-Anbaugerät montiert werden kann, ist das ein Vorteil, da man sich das Aufrüsten des hinteren Mastes sparen möchte. So entfällt der Transport zusätzlichen Ballasts zur Baustelle für die Auslegermontage. Ich denke, die jüngsten Entwicklungen bei Gittermastkranen wurden von der Windkraftindustrie angestoßen. Früher waren es die Windkraftanlagen an Land, aber die neueste Entwicklung findet in der Offshore-Industrie statt, insbesondere jetzt, wo der US-Markt involviert ist.
Wir erhalten derzeit viele Anfragen für den Einsatz von Raupenkranen oder Gittermastkranen zum Rangieren. Das bedeutet, einen Kran am Ufer im Hafen zu platzieren, um die Türme und Windkraftanlagen für ihre Seereise vorzubereiten und die Komponenten an Bord des Seeschiffs zu verladen. Für die größeren Auslegerkrane in unserer Flotte ist das derzeit unser Hauptmarkt.
Abhängig davon, ob die Feederschiffe für Roll-on/Roll-off geeignet sind oder nicht, können wir auch den SPMT-Transport vom Herstellergelände zum Rangierkai ermöglichen.
Windkraftanlagen werden immer größer, daher muss auch die gesamte Ausrüstung größer werden. Wird es schwieriger, Raupenkrane dorthin zu transportieren?
HS: Das ist von Land zu Land unterschiedlich, aber ich glaube, die meisten Kranhersteller halten sich bei internationalen Transporten an die Regel von maximal 60 Tonnen Komponentengewicht. Das hängt von der Größe des Gittermastkrans ab. Für kleinere Gittermast-Raupenkrane sind 60 Tonnen Eigengewicht natürlich zu viel. Man möchte das Eigengewicht so gering wie möglich halten.
Für den Transport sind möglichst leichte Krankomponenten von Vorteil. Bei den meisten Kränen, beispielsweise der 600-Tonnen-Klasse, lässt sich der A-Rahmen inklusive Derrickwinde demontieren. Dadurch können die meisten Kranaufbauten die 60-Tonnen-Grenze einhalten. Um größere Kräne zu bewegen, werden sie geteilt und der Oberwagen über eine Schnellverbindung am Drehkranz vom Unterwagen getrennt. Manchmal sind Schnellverbindungen jedoch etwas komplizierter als andere. Es ist besser, den Drehkranz am Unterwagen zu belassen und den Oberwagen mit einer Vierbolzenverbindung oder ähnlichem oben zu montieren.
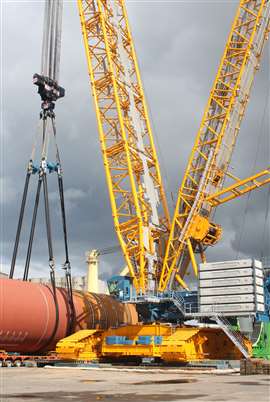
Der einfache Transport geht Hand in Hand mit der einfachen Montage. Wir können das eine nicht vom anderen trennen. Es ist eine unendliche Geschichte, aber es gibt in diesem Bereich kontinuierliche Entwicklungen.
Was sind die Hauptunterschiede und Vorteile von Gittermast-Raupenkranen gegenüber Teleskopmast-Raupenkranen?
HS: Das hängt mit der Dauer des Einsatzes zusammen. Je nach Dauer eines bestimmten Einsatzes sind Teleskopkrane ein echter Vorteil, da sie sich leichter zur Baustelle transportieren lassen als Gittermastkrane. Zudem ist der Aufbau in wenigen Stunden erledigt, sodass die Montage sehr schnell geht. Bei einem Gittermastkran muss die Karosserie separat transportiert werden. Bei kleineren Kranen können die Ketten jedoch noch montiert sein, sodass man sie direkt vom Anhänger aus fahren kann.
Wenn der Auftrag nur ein paar Tage dauert, ist ein Gittermast-Raupenkran sinnlos, wenn die Arbeit auch mit einem Teleskopkran erledigt werden kann. Auch die Planungsphase ist für einen kurzen Auftrag zu aufwändig.
Und es gibt einen Preisunterschied: Die Miete eines Gittermastkrans ist günstiger als die eines vergleichbaren Teleskopkrans, die Kosten für die Mobilisierung/Demobilisierung sind jedoch erheblich höher.
Der Vorteil eines Raupenkrans besteht darin, dass man mit Last fahren kann. Bei einem Teleskopkran, der in einem gewissen Abstand zur Last positioniert ist, kann man sich nach dem Aufbau des Krans nicht mehr nähern. Fehlt die Kapazität für ein oder zwei Meter zusätzlichen Radius, ist nicht viel möglich. Beispielsweise ist der Kranaufbau eines Raupenkrans kompakter. Man kann meist näher an die Last heranfahren.
Mit einem kleineren Gittermastkran kann man Arbeiten erledigen als mit einem Teleskopkran, da der leichtere Gittermast mehr Hubkapazität bietet und man die Last mitfahren kann. Das ist manchmal ein Vorteil. Manche Kunden haben jedoch zunächst ein Missverständnis wegen der Fähigkeit eines Raupenkrans, sich mit Last zu bewegen, und möchten ihn daher als Transportmittel nutzen. Das wollen wir vermeiden und sagen unseren Kunden, dass Fahrten mit Last nur über kurze Strecken erfolgen sollten. Ein Raupenkran ist kein Ersatz für einen Lkw. Nur Kräne bis zur 180-Tonnen-Klasse können mit Traktor-Raupenketten ausgestattet werden. Diese Raupenketten wie bei Bulldozern gibt es bei den größeren Modellen nicht. Bei den größeren Modellen sind die Raupenplatten nicht auf einer Kette montiert, sondern laufen auf Stahlrollen, die in das Fahrgestell der Raupe integriert sind. Diese sind sehr verschleißanfällig. Bei längeren Fahrten verschleißen die Ketten schnell, und eine Überholung ist sehr teuer.
Wie schneiden Raupenkrane im Vergleich zu anderen Krantypen wie beispielsweise All-Terrain-Kranen ab?
HS: Es kommt darauf an, wofür Sie es verwenden, es ist arbeitsplatzspezifisch.
Beispielsweise werden für den Aufbau unserer größeren Kräne ein oder mehrere Hilfskrane benötigt. Wenn der Aufbau eines großen Krans 14 Tage dauert, ist ein kleiner Raupenkran von Vorteil, da er im Vergleich zu einem Teleskopkran schneller aufgebaut werden kann, da er leicht zu bewegen ist und keine Aufstellung benötigt. Mit einem Raupenkran dauert es nur wenige Minuten, und Sie sind am anderen Ende der Baustelle einsatzbereit.
Meistens ist es keine technische, sondern eine wirtschaftliche Frage. Es geht um die Kosten. Die Mobilisierungskosten eines Raupenkrans sind höher als die eines Teleskopkrans. Sarens hat weltweit viele Niederlassungen. Je nach Einsatzort stehen daher unterschiedliche Optionen zur Verfügung. Die Entscheidung, ob ein Raupen- oder ein Teleskopkran eingesetzt wird, kann je nach Land und Standort unterschiedlich ausfallen.
Was ist die größte Herausforderung in Bezug auf die Sicherheit bei Gittermast-Raupenkranen?
HS: Die größte Herausforderung in Sachen Sicherheit ist, wie bei vielen anderen Krantypen auch, die Arbeit in der Höhe. Ich muss sagen, dass die Hersteller in den letzten zehn Jahren hier echte Fortschritte gemacht haben. Mit der steigenden Nachfrage nach Windkraftanlagen, bei denen Kräne häufig bewegt werden müssen, kommt es deutlich mehr zu Arbeiten in der Höhe. Glücklicherweise war die Sicherheitskultur jedoch bereits in der Raffinerie- und Petrochemiebranche vorhanden. Diese Branche war die erste mit hauptamtlichen Sicherheitsbeauftragten auf ihren Baustellen und hat bis heute die Standards für Sicherheit maßgeblich mitgestaltet.
Darüber hinaus wurden Maßnahmen ergriffen, um sicherzustellen, dass die Arbeiter eine Sicherheitsschulung absolviert haben, bevor sie die Baustelle betreten dürfen.
Die Standardisierung von Sicherheitsschulungen erfolgte erst später, da anfangs verschiedene Unternehmen jeweils eigene, spezifische Sicherheitsschulungen durchführten. Heute ist die Schulung standardisierter, und wenn auf einer Baustelle besondere Anforderungen bestehen, kann ein Informationsvideo auf die besonderen Anforderungen für diese Baustelle hinweisen.
Sogar Windkraftanlagenunternehmen verfügen über Sicherheitssysteme, zu denen Vollzeit-Sicherheitsbeauftragte vor Ort gehören, und die Arbeiter müssen vor Arbeitsbeginn eine Einweisung absolvieren.
Seit der Einführung der EG-Verordnungen in Europa im Jahr 1985 steht die Sicherheit kontinuierlich im Fokus. Kranhersteller müssen nachweisen, dass ihre Maschinen sicher sind und sicher betrieben werden können. Dazu gehören auch die Vorschriften für Hebevorgänge und Hebezeuge (z. B. LOLER).
Auch die sichere Montage eines Krans wurde thematisiert. Kranunternehmen und -hersteller tragen gleichermaßen Verantwortung für die Sicherheit beim Aufrüsten der Krane. Ein moderner Kran ist heutzutage mit verschiedenen Systemen ausgestattet, die eine sichere Montage gewährleisten, wie z. B. Zugangsplattformen, Rettungsleinen, Ankerpunkte, Sicherheitsnetze usw.
Das Problem besteht nun darin, dass bei Kränen älterer Bauart diese Absturzsicherungssysteme nachgerüstet werden müssen. In vielen Fällen ist eine Nachrüstung möglich, aber es ist einfacher, Sicherheitssysteme von Anfang an in die Konstruktion zu integrieren. Außerdem ist es kostengünstiger. Die europäischen Sicherheitsvorschriften sind streng und erschweren den Import von Kränen aus anderen Teilen der Welt.
Verfügt Europa über die strengsten Sicherheitsvorschriften der Welt?
HS: Das ist schwer zu sagen, aber die europäischen Sicherheitsvorschriften sind auf jeden Fall recht fortschrittlich. Einige Länder folgen den europäischen Vorschriften, wie zum Beispiel Australien. Es hat seine eigenen spezifischen Sicherheitsvorschriften für den Betrieb im Land, akzeptiert aber Kräne, die den EU-Normen entsprechen. Ich denke, die Einstellung ist, dass ein Kran, der von Europa als sicher eingestuft wird, für den Einsatz in Australien importiert werden kann. Die USA haben ihre eigenen Standards. Die amerikanische Gesetzgebung unterscheidet sich von der europäischen. Im Allgemeinen ist es kein Problem, von Europa in die USA zu importieren, da die europäischen Kranhersteller sowohl die EN- als auch die ANSI-Normen berücksichtigen. Umgekehrt ist es manchmal etwas schwieriger.
Welche neueste Raupenkrantechnologie begeistert Sie am meisten?
HS: Ich bin immer an größeren Raupenkranen interessiert. Etwa 15 Jahre lang galt eine 600-Tonnen-Maschine als großer Raupenkran. Dann stieg sie in die 750-t- bis 800-t-Klasse auf. Aber jetzt schauen wir uns die
Die 1000-Tonnen-Klasse wird sich zu einer gängigen Kranklasse entwickeln. All dies wurde hauptsächlich von der Windkraftindustrie vorangetrieben.
Wir beobachten, dass hier in Europa immer mehr kleinere Kranunternehmen relativ große Raupenkrane in ihrer Flotte haben. Das hängt mit der zunehmenden Höhe von Windkraftanlagen zusammen, und diese steigt weiter. Derzeit liegt die maximale Nabenhöhe in Europa bei etwa 180 Metern. Das ist aber noch nicht der Standard. Es gibt bereits einige Windparks mit Anlagen mit einer Nabenhöhe von 165 Metern. Es wird jedoch erwartet, dass diese Zahl weiter steigt.
Vor etwa 15 Jahren dachten wir, die maximale Spitzenhöhe liege aufgrund der Flugverkehrsbestimmungen bei 200 Metern. Heute scheint es keine strikte Begrenzung für die Höhe der Türme mehr zu geben. Wir haben festgestellt, dass die Effizienz einer Windkraftanlage steigt, je höher sie gebaut wird. Allerdings entstehen dadurch auch Kosten, und es ist recht teuer, Turbinen in so große Höhen zu bringen.
Der Umstieg von einem 600-Tonnen-Raupenkran auf einen 1000-Tonnen-Raupenkran zur Installation einer Turbine führt zu einem deutlichen Preisanstieg und verringert zudem die Verfügbarkeit. Ich glaube, derzeit gibt es nur etwa 100 Exemplare. Wir beobachten jedoch einen starken Anstieg der Beliebtheit von 800-Tonnen-Maschinen. Krane wie der Liebherr-Raupenkran LR 1800-1.0 mit 800 Tonnen Tragkraft bedienen diesen Markt, wobei der LG 1800-1.0 das neue Flaggschiff dieser Klasse ist. Ich denke, er ist genau zum richtigen Zeitpunkt auf den Markt gekommen. Liebherr pflegt Kontakte und kommuniziert mit Windkraftanlagenherstellern, um die wichtigsten Informationen für die Kranentwicklung und den zukünftigen Bedarf aus erster Hand zu erhalten.
Die 750- bis 800-Tonnen-Klasse ist die aktuelle Gewichtsklasse für den Bau von Windkraftanlagen, aber ich denke, sie könnte auf die 1000-Tonnen-Klasse anwachsen. Es gibt Turbinenprototypen, die darauf hindeuten, dass dies die Zukunft sein könnte, aber es ist schwer vorherzusagen. Es gibt immer wieder Diskussionen über das zunehmende Gewicht der Gondeln und darüber, ob sie in einem Stück gehoben werden könnten. Ich denke, man kann ein paar Jahre vorausschauen, aber nicht viel weiter.
Tadano arbeitet außerdem an einem neuen Raupenkran mit größerer Kapazität für die Windkraftindustrie. Dieser muss rechtzeitig auf den Markt kommen. Es geht darum, die zukünftige Nachfrage präzise vorherzusagen, um die Kapazitäten zu haben, die die Branche benötigt, ohne diese zu überschreiten. Die Lieferung muss pünktlich erfolgen.
Das haben wir von Anfang an berücksichtigt. Bei Gittermast-Raupenkranen für die Montage von Windkraftanlagen war die Stabilität des Auslegers bei jeder Krankonstruktion von entscheidender Bedeutung. Windkraftanlagen werden logischerweise in windigen Gebieten installiert, aber Wind kann natürlich eine zusätzliche Herausforderung darstellen. Sie benötigen ein Auslegersystem, das Wind aus allen Richtungen standhält, insbesondere seitlich. Je länger der Ausleger, desto schwieriger ist es, die seitlichen Kräfte aufzunehmen.
Anfangs versuchten die Unternehmen, bei den europäischen Transportmaßen von 3,5 Metern Breite zu bleiben, da es für den Transport darüber hinaus schwierig war, Straßengenehmigungen zu erhalten.
Die Vergrößerung der Auslegerbreite von 3 auf 3,5 Meter verbesserte die Stabilität bei Seitenwind. Doch das war nur der erste Schritt, und die Unternehmen erkannten, dass dies nicht ausreichte, um neue Höhen zu bewältigen. Liebherr entwickelte daraufhin den Parallelausleger, den Powerboom, der aus zwei parallel zueinander angeordneten Auslegern bestand. Zwei Standardausleger wurden nebeneinander angeordnet, wodurch höhere Lasten gehoben werden konnten. Der breitere Ausleger erhöht zwar nicht die Krankapazität, ermöglicht aber größere Lasten in größere Höhen – genau das, was die Windindustrie wünschte.
Das war eine großartige Lösung, doch die nächste Herausforderung bestand darin, dass ein Parallelausleger nicht materialeffizient ist. Das Verhältnis von Gewicht und Steifigkeit des Auslegers ist nicht ideal. Es ist besser, einen neuen, leichteren Ausleger mit höherer Steifigkeit zu konstruieren. Dies ist der Trend bei der Konstruktion neuer Kräne.
Diese breiteren Ausleger müssen steifer und gleichzeitig zusammenklappbar sein, da sich ein sechs oder acht Meter breiter Ausleger nicht transportieren lässt. Der Transport ist also wichtig, aber auch die Montagegeschwindigkeit. Liebherr und Tadano haben hierfür komplexe Lösungen entwickelt.
Letztes Jahr kaufte Sarens den ersten LR 12500-1.0 von Liebherr, und das Design des Auslegers ist äußerst interessant. Es ist der erste Kran mit einem speziellen T-förmigen Oberwagen und einem breiten, 7,5 Meter langen Ausleger, der direkt von unten beginnt. Liebherr nennt die neue Auslegerkonstruktion „High Performance Boom“. Wir sind überzeugt, dass dies die Gittermastkranbranche revolutionieren wird.
BLEIBEN SIE VERBUNDEN
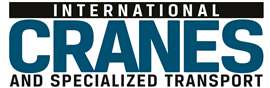
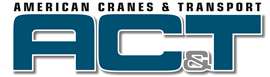
Erhalten Sie die Informationen, die Sie benötigen, genau dann, wenn Sie sie brauchen – über unsere weltweit führenden Magazine, Newsletter und täglichen Briefings.
KONTAKTIEREN SIE DAS TEAM
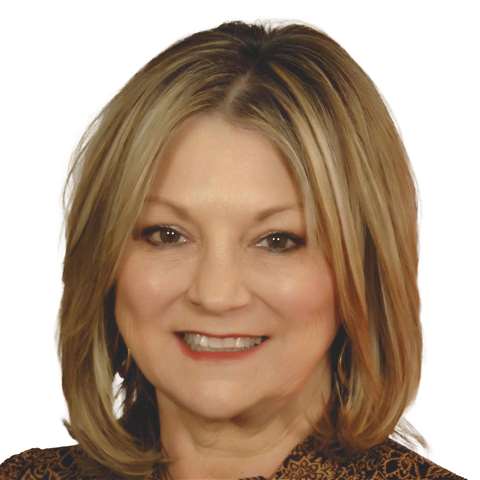
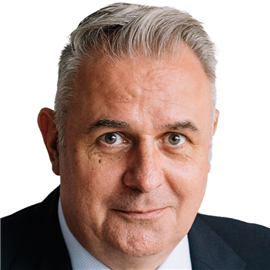
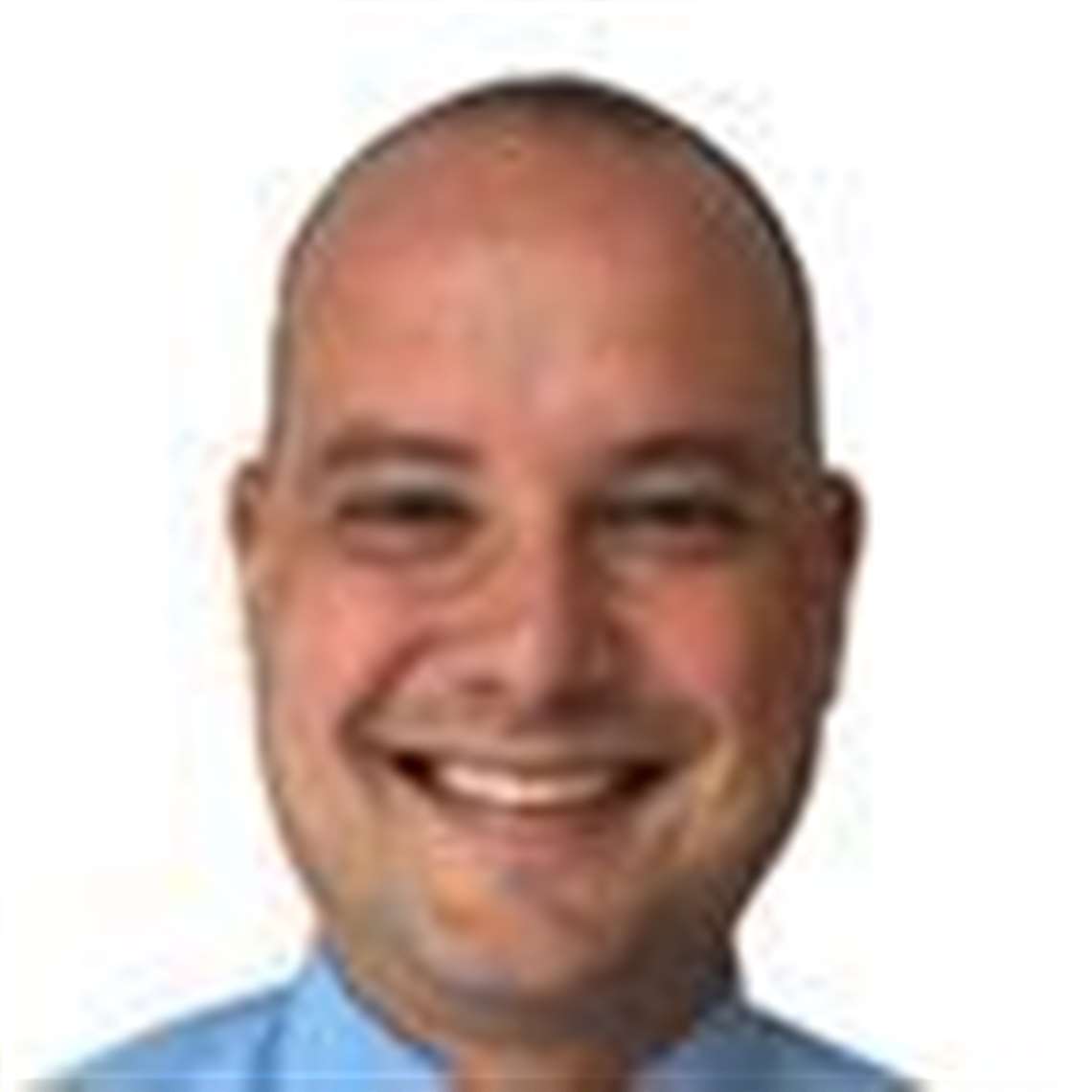
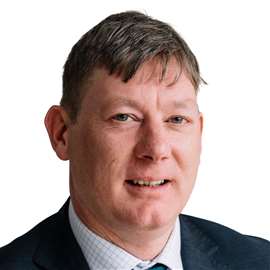