Read this article in French German Italian Portuguese Spanish
INTERVIEW: The game changer meeting future demand for crawlers
28 February 2024
ICST spoke exclusively to Sarens’ senior R&D engineer, and crawler crane expert, Hendrik Sanders, about meeting the future demand for crawler cranes.
International heavy lift and transport specialist Sarens continues to innovate with its ever-increasing lifting capabilities and transport operations. Progressively heavier loads are needing to be lifted, and crane manufacturers have had to adapt and produce ever-larger models to meet these huge project demands.
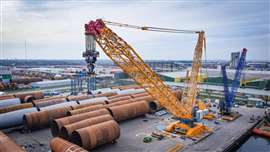
Sarens is continuing to meet this challenge, and is regularly adding high lifting capacity cranes to its fleet of over 1500 cranes, 3100 axle lines, and set of giant cranes.
Earlier in 2023, Sarens took delivery of the first unit of Liebherr’s new 2,500 tonne capacity crawler crane, the LR 12500-1.0. Sarens named its new crawler crane Straffen Hendrik, after its long-term employee Hendrik Sanders.
Rostock in Germany was the first place the LR 12500-1.0 was put to work for Sarens’ client Van Oord where it lifted 50 monopile foundations for offshore wind turbines. Each one had a diameter of up to nine metres and a length of up to 90 metres. They were lifted into the water in tandem with an 800 ton capacity Liebherr LR 1800-1.0 lattice boom crawler crane.
Currently Sarens is in final negotiation with Liebherr on the acquisition of a second LR 12500-1.0 for delivery in 2024.
How did your journey at Sarens begin?
HS: I’ve worked at Sarens for 34 years, and for most of that I’ve been in the crane business, particularly in the lattice boom division, and working with crawler cranes.
I was site supervisor for the first year, and I had been a site manager for several years. Then in 1993 came to the office environment and started in the engineering department. I did that for seven years and then moved to the operational side of the lattice boom crane department. Before I started there, we had a combined planning department for both lattice boom and telescopic cranes. As the company grew bigger and bigger, it became easier to split the departments as it was too complicated to keep it together – lattice boom crane are more a worldwide venture whereas the telescopic range is better managed on a local, or regional, level. So, I worked in the lattice boom department for several years and now I’m working in the research and development department. It means I can be a link between Sarens and crane manufacturers.
I try to get from the manufacturers what we want and need, and work with them on achieving what our newest cranes need. Crane manufacturers don’t usually design a crane for just one client, and they want their cranes to have global appeal, but I try and help demonstrate what we want and what is possible to create together.
I mainly work with the European manufacturers, though of course we also have Chinese cranes in our fleet like Sany, XCMG and Zoomlion. Chinese manufacturing has come a long way over the years, and they are now creating some real innovation of their own. So that’s been really interesting for me to follow and see the progress.
What is the main difference between the Chinese and the European manufacturers?
HS: Chinese manufacturers are trying out several new innovations. For instance, a mini super lift for boom erection built into the back of the crane. This is useful because in lattice boom cranes, one of the main challenges is boom erection. If you can erect the main boom without a derrick attachment, it’s an advantage because you want to avoid rigging the back mast. You can then avoid transporting additional ballast to site for boom erection. I think that the recent developments seen in lattice boom cranes have been triggered by the wind turbine industry. Previously it was the wind turbines on land but the latest development is in the offshore industry, especially now the USA market is getting involved.
We get a lot of requests now to deploy crawler cranes or lattice boom cranes for marshalling. This means to put a crane alongside the shore at the port, to prepare the towers and wind turbines for their sea voyage and the loading of the components on board of the sea-going vessel. For the bigger boom cranes in our fleet, that’s the major market for us now.
Depending whether the feeder barges are suited for roll on / roll off or not, we can also facilitate SPMT transport from the manufacturer’ yard to the marshalling quay.
Wind turbines are getting bigger and bigger, so all the equipment has to get bigger too. Is it becoming more difficult to transport crawler cranes to these sites?
HS: It is different for different countries, but I think most crane manufactures follow the rule of 60 tons of component weight as the maximum for international transport. It depends on the size of the lattice boom crane. For smaller lattice boom crawler cranes, 60 ton of body weight is of course too much. You want to stay as low as possible with the body weight.
It’s always an advantage to have crane components as light as reasonably possible, for transport. With most of the cranes, let’s say in the 600 ton class, the A-frame including the derricking winch can be removed. By doing that, most of the crane bodies can stay within the limit of 60 ton. When you have to move the bigger cranes you have split them and divide the superstructure from the carrier with a quick connection at the slewing ring. But sometimes quick connections are a bit more intricate than others. It’s better to keep the slew ring attached to the carbody and have a four-pin connection or something similar to install the superstructure on top.
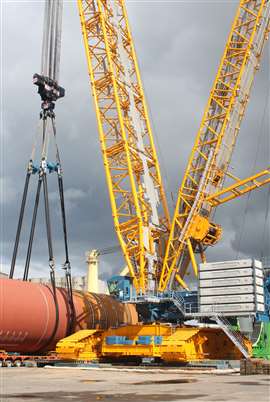
The ease of transportation goes hand in hand with the ease of rigging, we can’t split one from the other. It’s a never-ending story but there is continual development on this front.
What are the main differences and advantages of lattice boom versus telescopic boom crawler cranes?
HS: It has to do with the duration of the job. Depending on the duration of a particular job, telescopic cranes are a real advantage as you can travel easier to site than with lattice boom cranes, and the set up can be done in a few hours, so it’s a very fast assembly. With a lattice boom crane, you have to transport the body separately. Though if it’s a smaller crane, the tracks can still be on, so you can drive it straight from the trailer.
If the job is only for a few days, there’s no point having a lattice boom crawler crane if the job can be done by a telescopic crane. It’s too difficult with the planning stage too for a short job.
And there’s a price difference, rental of a lattice boom crane is cheaper than a comparable telescopic crane., but the mobilization / demobilization cost is considerably more expensive.
The advantage of a crawler crane is that you can travel with a load. When you have a telescopic crane, positioned at a certain distance from the load, you cannot approach once the crane is set up. If you are missing capacity for one or two meters extra radius, there is not much you can do. Let’s say with a crawler crane, the crane body is more compact. You mostly can get closer to the load.
You can do a job with a smaller lattice boom crane compared to a telescopic crane, because the lighter lattice boom offers more lifting capacity, and you can move with the load. So this is sometimes an advantage. Some clients have a misunderstanding initially because of the ability of a crawler crane to move with a load, so they want to use it as a means of transport. We do not want this and tell clients that traveling with a load, should only be done over short distances. It is not a replacement for a truck or a lorry. Only cranes up to the 180 ton class can have tractor type of crawler chains. These bulldozer type of tracks don’t exist with the bigger models. With the bigger models the crawler pads are not mounted on a chain, but are running on steel rollers incorporated in the chassis of the crawler. And they are very prone to wear. So, if you drive extensive distances, you will wear out the tracks quickly and it’s very expensive to refurbish the tracks.
How do crawler cranes compare with other crane types such as all terrain cranes?
HS: It’s what you’re using it for, it’s job specific.
As an example, for rigging our bigger cranes, one or more assistant cranes are needed. If the rigging of a large crane takes 14 days, it really is an advantage to have a small crawler crane as the rigging goes faster compared to a telescopic crane, because you don’t have to set it up, and it’s easy to move. With a crawler crane, it takes only a few minutes and you’re ready to lift at the other end of the site.
Most of the time it’s not a technical question but a commercial one. It’s cost. For the mobilization cost of a crawler crane is more expensive than a telescopic crane. With Sarens, we have lots of branches worldwide so depending on where the job site is, there will be different options available for the work, and the decision of whether to use a crawler or a telescopic crane can differ between countries and sites.
What is the biggest challenge with safety when it comes to lattice boom crawler cranes?
HS: The biggest challenge in terms of safety, as with many other crane types, is working at height. I must say that in the last 10 years, manufacturers have made real progress on this. With increasing wind turbine erection demand, where cranes have to be moved very often, there is a lot more working at height, but luckily the safety culture was already in place from the refinery and petrochemical jobs of the past. That industry was the first to have full time safety officers on their sites, and they have continued to lead in setting the standards for safety.
There’s also been developments to ensure that workers have followed a safety training before they can enter on site.
Standardization of safety training has come later, as initially different companies each had their specific safety training. Now it is more standardized, and if there is a specific requirement on a particular job site, an informational video can show special points of attention for that site.
Even wind turbine companies have systems of safety that include full time safety officers on site, and workers have to complete an induction before commencing work.
Safety has been continually under focus since the introduction of the EC regulations in Europe in 1985, crane manufacturers had to prove that their machines were safe and could be operated safely. This includes the lifting operations and lifting equipment regulations (e.g. LOLER).
Rigging a crane safely has also been addressed. Crane companies and manufacturers alike take responsibility for the safety during rigging of the cranes. A modern crane nowadays is equipped with all sorts of systems to ensure safe rigging, such as access platforms, lifelines, anchor points, safety nets, etc…
Now the issue is with cranes that have an older design, you need to retrofit these fall arrest systems. In many cases, retrofit can be done, but it’s easier to incorporate safety systems from the beginning into the design. It’s also less expensive. European safety regulations are strict, and it makes it harder to import cranes from other parts of the world.
Does Europe have the strictest regulations on safety in the world?
HS: It is hard to say, but European safety regulations are for sure quite advanced. Some countries follow the European regulations, such as Australia. It has its own specific safety rules for operating in the country but it accepts cranes that adhere to EU standards. I think the attitude is that if a crane is deemed safe by Europe, it can be imported for work in Australia. The USA has its own standards. American legislation is not the same as in Europe. In general, it’s not a problem to import from Europe to the USA, as the European crane manufacturers take both EN and ANSI standards into account, but it’s sometimes a little difficult the other way around.
What is the latest crawler crane technology that you’re excited about?
HS: For me I’m always interested in bigger crawler cranes. For say 15 years or so, a 600 tons machine was a big crawler crane. Then it moved up to the 750t-800t class. But now we are looking at the
1000 ton class to become a common crane class. All this has mainly been driven by the wind turbine industry.
We see that now more and more here in Europe, smaller crane companies have relatively big crawler cranes in their fleet. And it is all to do with the increasing heights of wind turbines, and it’s rising. For the moment, the maximum hub height here in Europe is about 180 meters. But this is not the standard yet. There are already quite some wind farms with turbines with 165 meters of hub height. But the expectation is that this will go up.
Maybe 15 years ago we thought the total limit would be 200 metres for tip heights, because of air traffic regulations. Now there doesn’t seem to be a strict limit for the height of the towers. We have seen that the higher you put the wind turbine, the greater its efficiency, but of course there’s a cost implication and it’s quite expensive to get turbines up to such great heights.
Moving from a 600 ton crawler to a 1000 ton crawler to install a turbine creates a significant price increase, and also there’s less availability. I think at the moment there’s only about 100 or so. But we’re seeing a surge in popularity of 800 tonne machines. Cranes like Liebherr’s 800 ton capacity LR 1800-1.0 crawler are serving this market, with LG 1800-1.0 as the new flag ship in this class. I think it’s become available to the market at exactly the right time. Liebherr keeps links and communication with wind turbine manufacturers so that they can get the most relevant information firsthand for crane development and future needs.
The 750t-800t class is the current class for wind turbine erection but I do think it could move up to the 1000t class. There are prototypes of turbines that suggest this could be the future but it’s difficult to predict. There’s always the never-ending discussion about the increasing weight of nacelles, and if they could be lifted in one piece. I think you can look a few years ahead but not much further.
Tadano is also working on a new larger capacity crawler crane for the wind turbine business, and they need to get availability to market at the right time. It’s about predicting future demand precisely, so you have something the industry needs in terms of capacity but not overshoot it. It needs to be right on time.
That’s something we looked at from the beginning. With lattice boom crawler cranes for wind turbine erection, the stability of the boom was very important for any crane design. Turbines are installed in windy areas, logically, but wind of course can pose an additional challenge. You need a boom system on the crane that is resistant to wind from any direction, particularly from the side. With longer booms, the more difficult it is to take the sideways forces.
In the beginning companies tried to stay with the European transport dimensions of 3.5 metres width, as beyond that, it’s difficult to get road permits for transportation.
Taking the boom width from 3 to 3.5 metres helped improve stability when dealing with sideways wind. But that was just the first step and companies realized that was not sufficient to deal with new heights. Liebherr then came up with their parallel boom, the power boom, which had two booms parallel to each other. They took two standard booms and put them side by side and they were able to lift loads higher. The wider boom doesn’t increase the crane capacity as such but you can lift the same loads to larger heights, which was exactly what the wind industry wanted.
It was a great solution but the next challenge was that a parallel boom is not material efficient. The weight of the boom compared to its capacity for stiffness, this weight stiffness ratio is not ideal. It’s better to design a new, lighter boom that has more stiffness. This is the tendency in new crane design.
These wider booms have to be more stiff, but also they need to be collapsible, because you can’t transport a boom that is 6 or 8 metres wide. So, transport is important but so is the speed of assembly. Liebherr and Tadano both have worked out intricate solutions to this.
Last year, Sarens bought the first LR 12500-1.0 from Liebherr, and the design of the boom is so interesting. It’s the first crane with a special T-shaped superstructure with a wide 7.5 metre boom that starts right from the bottom. Liebherr calls the new boom construction the High Performance Boom. We are really convinced that this will be a game changer for the lattice boom crane industry.
STAY CONNECTED
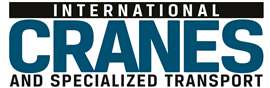
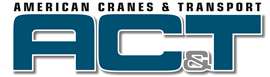
Receive the information you need when you need it through our world-leading magazines, newsletters and daily briefings.
CONNECT WITH THE TEAM
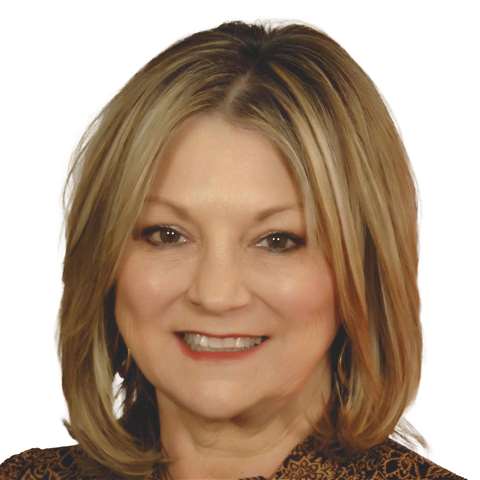
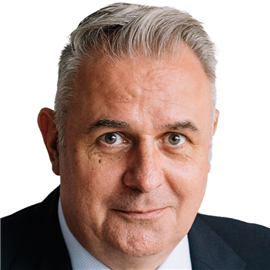
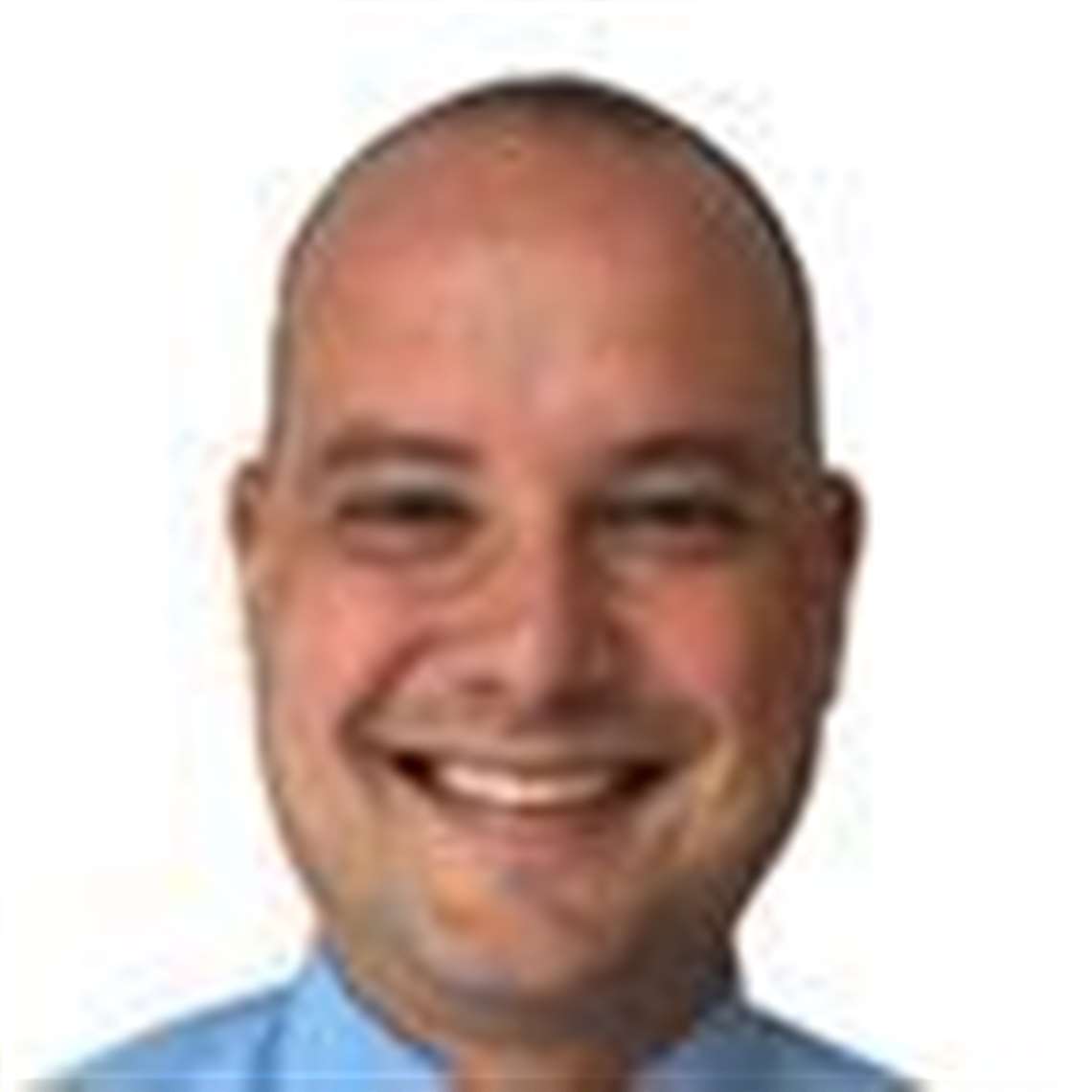
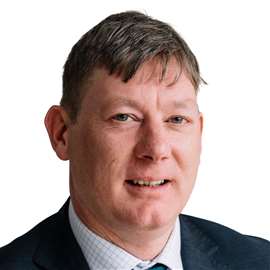