Article traduit automatiquement par l’IA, lire l’original
INTERVIEW : Le changement de jeu qui répond à la demande future de robots d'exploration
28 février 2024
L'ICST s'est entretenu en exclusivité avec Hendrik Sanders, ingénieur principal en R&D et expert en grues sur chenilles de Sarens, pour savoir comment répondre à la demande future de grues sur chenilles.
Sarens, spécialiste international du levage et du transport de charges lourdes, continue d'innover grâce à ses capacités de levage et à ses opérations de transport en constante évolution. Face à des charges de plus en plus lourdes, les fabricants de grues ont dû s'adapter et produire des modèles toujours plus imposants pour répondre à ces exigences de projets colossales.
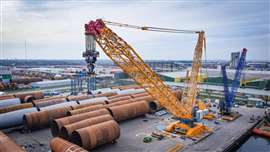
Sarens continue de relever ce défi et ajoute régulièrement des grues à haute capacité de levage à sa flotte de plus de 1 500 grues, 3 100 lignes d'essieux et un ensemble de grues géantes.
Début 2023, Sarens a réceptionné la première unité de la nouvelle grue sur chenilles Liebherr d'une capacité de 2 500 tonnes, la LR 12500-1.0. Sarens a baptisé sa nouvelle grue sur chenilles Straffen Hendrik, en hommage à son employé de longue date, Hendrik Sanders.
Rostock, en Allemagne, a été le premier site où la LR 12500-1.0 a été mise à contribution pour Van Oord, client de Sarens, où elle a soulevé 50 fondations monopiles pour éoliennes offshore. Chacune d'elles mesurait jusqu'à neuf mètres de diamètre et 90 mètres de longueur. Elles ont été mises à l'eau grâce à une grue sur chenilles à flèche treillis Liebherr LR 1800-1.0 d'une capacité de 800 tonnes.
Actuellement, Sarens est en négociation finale avec Liebherr pour l'acquisition d'un deuxième LR 12500-1.0 pour une livraison en 2024.
Comment a commencé votre parcours chez Sarens ?
HS : Je travaille chez Sarens depuis 34 ans et, pendant la majeure partie de cette période, j'ai travaillé dans le secteur des grues, en particulier dans la division des flèches en treillis et avec des grues sur chenilles.
J'ai été chef de chantier la première année, après avoir été chef de chantier pendant plusieurs années. Puis, en 1993, j'ai rejoint le bureau et intégré le service ingénierie. J'y ai travaillé pendant sept ans, puis je suis passé au service opérationnel des grues à flèche treillis. Avant cela, nous avions un service de planification commun pour les grues à flèche treillis et les grues télescopiques. Avec la croissance de l'entreprise, il est devenu plus facile de scinder les services, car la cohésion était trop complexe : les grues à flèche treillis sont davantage une activité mondiale, tandis que la gamme télescopique est mieux gérée au niveau local ou régional. J'ai donc travaillé au service des grues à flèche treillis pendant plusieurs années et je travaille maintenant au service recherche et développement. Cela me permet d'être un lien entre Sarens et les fabricants de grues.
J'essaie d'obtenir des fabricants ce dont nous avons besoin et ce que nous souhaitons, et je travaille avec eux pour répondre aux besoins de nos nouvelles grues. Les fabricants de grues ne conçoivent généralement pas une grue pour un seul client et souhaitent que leurs grues soient commercialisées dans le monde entier. J'essaie de les aider à démontrer nos aspirations et ce qu'il est possible de créer ensemble.
Je travaille principalement avec des fabricants européens, même si notre flotte compte bien sûr aussi des grues chinoises comme Sany, XCMG et Zoomlion. L'industrie manufacturière chinoise a beaucoup progressé au fil des ans et elle innove désormais de manière significative. C'est donc très intéressant pour moi de suivre et d'observer ces progrès.
Quelle est la principale différence entre les fabricants chinois et européens ?
HS : Les fabricants chinois testent plusieurs innovations. Par exemple, un mini-super-élévateur pour le montage de la flèche, intégré à l'arrière de la grue. C'est utile car, avec les grues à flèche treillis, l'un des principaux défis est le montage de la flèche. Pouvoir monter la flèche principale sans mât de charge est un avantage, car cela évite de gréer le mât arrière. On évite ainsi de transporter du lest supplémentaire sur le site pour le montage de la flèche. Je pense que les récents développements des grues à flèche treillis ont été initiés par l'industrie éolienne. Auparavant, c'était l'éolien terrestre, mais la dernière évolution concerne l'industrie offshore, notamment avec l'arrivée du marché américain.
Nous recevons actuellement de nombreuses demandes de déploiement de grues sur chenilles ou de grues à flèche en treillis pour le triage. Cela signifie qu'une grue doit être déployée le long du quai du port, afin de préparer les pylônes et les éoliennes pour leur voyage en mer et le chargement des composants à bord du navire. Pour les grues à flèche plus grandes de notre flotte, c'est notre principal marché actuel.
Selon que les barges d'alimentation sont adaptées au roulage ou non, nous pouvons également faciliter le transport SPMT du chantier du fabricant jusqu'au quai de triage.
Les éoliennes sont de plus en plus grandes, et donc tous les équipements doivent l'être aussi. Le transport des grues sur chenilles vers ces sites devient-il plus difficile ?
HS : Cela varie selon les pays, mais je pense que la plupart des fabricants de grues appliquent la règle des 60 tonnes de poids des composants comme limite pour le transport international. Cela dépend de la taille de la grue à flèche en treillis. Pour les grues sur chenilles à flèche en treillis plus petites, un poids de 60 tonnes est évidemment excessif. Il est important de maintenir un poids de la grue aussi bas que possible.
Il est toujours avantageux d'avoir des composants de grue aussi légers que possible pour le transport. Sur la plupart des grues, disons de la catégorie 600 tonnes, le cadre en A, y compris le treuil de levage, peut être retiré. Ainsi, la plupart des corps de grue peuvent rester dans la limite de 60 tonnes. Pour déplacer les grues plus grandes, il faut les séparer et séparer la superstructure du porteur grâce à une connexion rapide au niveau de la couronne d'orientation. Cependant, ces connexions rapides sont parfois plus complexes. Il est préférable de conserver la couronne d'orientation fixée à la caisse et d'utiliser une connexion à quatre broches ou un dispositif similaire pour fixer la superstructure par-dessus.
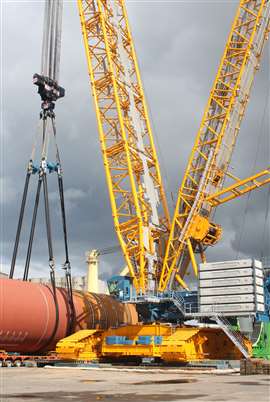
La facilité de transport va de pair avec la facilité de montage ; nous ne pouvons pas dissocier l'une de l'autre. C'est une histoire sans fin, mais le développement est continu dans ce domaine.
Quelles sont les principales différences et avantages des grues sur chenilles à flèche en treillis par rapport aux grues sur chenilles à flèche télescopique ?
HS : Cela dépend de la durée du chantier. Selon la durée du chantier, les grues télescopiques présentent un réel avantage : elles permettent de se déplacer plus facilement sur le chantier qu'avec les grues à flèche en treillis, et le montage peut se faire en quelques heures, ce qui rend le montage très rapide. Avec une grue à flèche en treillis, il faut transporter la carrosserie séparément. En revanche, si la grue est plus petite, les chenilles peuvent rester en place, ce qui permet de la conduire directement depuis la remorque.
Si le chantier ne dure que quelques jours, il est inutile d'avoir une grue à chenilles à flèche treillis si le travail peut être réalisé avec une grue télescopique. La planification est également trop complexe pour un chantier de courte durée.
Et il y a une différence de prix, la location d'une grue à flèche en treillis est moins chère qu'une grue télescopique comparable, mais le coût de mobilisation/démobilisation est considérablement plus élevé.
L'avantage d'une grue sur chenilles est qu'elle permet de se déplacer avec une charge. Avec une grue télescopique, positionnée à une certaine distance de la charge, il est impossible de s'en approcher une fois installée. S'il vous manque un ou deux mètres de rayon supplémentaire, vous ne pouvez pas faire grand-chose. Par exemple, avec une grue sur chenilles, le corps de la grue est plus compact, ce qui permet généralement de se rapprocher de la charge.
Il est possible d'effectuer des travaux avec une grue à flèche treillis plus petite qu'une grue télescopique, car sa flèche treillis plus légère offre une plus grande capacité de levage et permet de déplacer la charge. C'est donc parfois un avantage. Certains clients ont d'abord une idée fausse quant à la capacité d'une grue sur chenilles à se déplacer avec une charge, et souhaitent donc l'utiliser comme moyen de transport. Nous ne souhaitons pas cela et indiquons à nos clients que les déplacements avec une charge ne doivent se faire que sur de courtes distances. Ce n'est pas un substitut à un camion. Seules les grues jusqu'à 180 tonnes peuvent être équipées de chaînes de chenilles de type tracteur. Ces chenilles de type bulldozer ne sont pas disponibles sur les modèles plus grands. Sur ces modèles, les patins de chenille ne sont pas montés sur une chaîne, mais sur des rouleaux en acier intégrés au châssis de la grue. De plus, ils sont très sensibles à l'usure. Ainsi, sur de longues distances, les chenilles s'usent rapidement et leur remise en état est très coûteuse.
Comment les grues sur chenilles se comparent-elles aux autres types de grues telles que les grues tout-terrain ?
HS : C'est à quoi vous l'utilisez, c'est spécifique au travail.
Par exemple, pour le montage de nos plus grosses grues, une ou plusieurs grues auxiliaires sont nécessaires. Si le montage d'une grande grue prend 14 jours, une petite grue sur chenilles est un réel avantage : le montage est plus rapide qu'une grue télescopique, car elle n'a pas besoin d'être installée et est facile à déplacer. Avec une grue sur chenilles, cela ne prend que quelques minutes et vous êtes prêt à lever la charge à l'autre bout du chantier.
La plupart du temps, il ne s'agit pas d'une question technique, mais d'une question commerciale : le coût. En effet, le coût de mobilisation d'une grue sur chenilles est plus élevé que celui d'une grue télescopique. Sarens possède de nombreuses succursales dans le monde. Ainsi, selon la localisation du chantier, différentes options seront disponibles. Le choix entre une grue sur chenilles et une grue télescopique peut varier selon les pays et les sites.
Quel est le plus grand défi en matière de sécurité lorsqu’il s’agit de grues sur chenilles à flèche en treillis ?
HS : Le plus grand défi en matière de sécurité, comme pour de nombreux autres types de grues, réside dans le travail en hauteur. Je dois dire qu'au cours des dix dernières années, les fabricants ont réalisé de réels progrès dans ce domaine. Avec la demande croissante de montage d'éoliennes, où les grues doivent être déplacées très fréquemment, le travail en hauteur est beaucoup plus fréquent. Heureusement, la culture de la sécurité était déjà bien ancrée dans les métiers du raffinage et de la pétrochimie. Ce secteur a été le premier à avoir des responsables sécurité à temps plein sur ses sites, et il a continué à jouer un rôle de premier plan dans l'établissement de normes de sécurité.
Des mesures ont également été prises pour garantir que les travailleurs ont suivi une formation en matière de sécurité avant de pouvoir entrer sur le site.
La standardisation des formations à la sécurité est intervenue plus tard, chaque entreprise ayant initialement sa propre formation spécifique. Aujourd'hui, la formation est plus standardisée et, si un chantier nécessite une exigence spécifique, une vidéo d'information peut présenter les points d'attention spécifiques à ce chantier.
Même les entreprises d'éoliennes disposent de systèmes de sécurité qui incluent des agents de sécurité à temps plein sur place, et les travailleurs doivent suivre une formation d'initiation avant de commencer à travailler.
Depuis l'introduction de la réglementation CE en Europe en 1985, la sécurité est au cœur des préoccupations. Les fabricants de grues doivent prouver que leurs machines sont sûres et peuvent être utilisées en toute sécurité. Cela inclut les réglementations relatives aux opérations de levage et aux équipements de levage (par exemple, LOLER).
La sécurité du montage d'une grue a également été abordée. Les entreprises et les fabricants de grues sont tous responsables de la sécurité lors du montage. Une grue moderne est aujourd'hui équipée de nombreux systèmes pour garantir la sécurité du montage, tels que des plateformes d'accès, des lignes de vie, des points d'ancrage, des filets de sécurité, etc.
Le problème concerne les grues de conception ancienne : il est nécessaire de moderniser ces systèmes antichute. Dans de nombreux cas, cette modernisation est possible, mais il est plus simple d'intégrer des systèmes de sécurité dès la conception. C'est également moins coûteux. Les réglementations européennes en matière de sécurité sont strictes, ce qui complique l'importation de grues d'autres régions du monde.
L’Europe possède-t-elle les réglementations de sécurité les plus strictes au monde ?
HS : Difficile à dire, mais les réglementations européennes en matière de sécurité sont incontestablement très avancées. Certains pays, comme l'Australie, appliquent les réglementations européennes. Elle a ses propres règles de sécurité pour l'exploitation sur son territoire, mais accepte les grues conformes aux normes européennes. Je pense que l'idée est que si une grue est jugée sûre par l'Europe, elle peut être importée pour travailler en Australie. Les États-Unis ont leurs propres normes. La législation américaine n'est pas la même qu'en Europe. En général, importer des grues d'Europe vers les États-Unis ne pose aucun problème, car les fabricants européens de grues respectent les normes EN et ANSI, mais l'inverse est parfois plus difficile.
Quelle est la dernière technologie de grue sur chenilles qui vous enthousiasme ?
HS : Personnellement, je suis toujours intéressé par les grues sur chenilles de plus grande taille. Pendant une quinzaine d'années, une machine de 600 tonnes était une grosse grue sur chenilles. Puis, on a atteint la catégorie des 750 à 800 tonnes. Mais aujourd'hui, nous nous intéressons à la
La catégorie des grues de 1 000 tonnes va devenir une catégorie courante. Cette tendance est principalement due à l'industrie éolienne.
Nous constatons qu'en Europe, de plus en plus de petites entreprises de grues possèdent des grues sur chenilles relativement imposantes dans leur parc. Cela est dû à la hauteur croissante des éoliennes, et cette tendance est en hausse. Actuellement, la hauteur maximale du moyeu en Europe est d'environ 180 mètres. Mais ce n'est pas encore la norme. Il existe déjà de nombreux parcs éoliens équipés d'éoliennes atteignant 165 mètres de hauteur de moyeu. Mais on s'attend à ce que cette hauteur augmente.
Il y a peut-être 15 ans, nous pensions que la hauteur maximale des éoliennes serait de 200 mètres, en raison de la réglementation du trafic aérien. Aujourd'hui, il ne semble plus y avoir de limite stricte pour la hauteur des tours. Nous avons constaté que plus une éolienne est haute, plus son rendement est élevé, mais cela a bien sûr un coût, et il est assez coûteux d'installer des éoliennes à de telles hauteurs.
Passer d'une grue sur chenilles de 600 tonnes à une grue sur chenilles de 1 000 tonnes pour l'installation d'une éolienne entraîne une augmentation significative des prix, et la disponibilité est également réduite. Je pense qu'il n'en existe qu'une centaine actuellement. Cependant, nous constatons un regain de popularité pour les machines de 800 tonnes. Des grues comme la grue sur chenilles LR 1800-1.0 de Liebherr, d'une capacité de 800 tonnes, sont destinées à ce marché, la LG 1800-1.0 étant le nouveau fleuron de cette catégorie. Je pense qu'elle est arrivée sur le marché au bon moment. Liebherr entretient des liens étroits avec les fabricants d'éoliennes afin qu'ils puissent obtenir les informations les plus pertinentes en première ligne pour le développement des grues et les besoins futurs.
La catégorie 750-800 tonnes est actuellement la catégorie d'éoliennes construites, mais je pense qu'elle pourrait évoluer vers la catégorie 1 000 tonnes. Certains prototypes d'éoliennes laissent présager que ce sera l'avenir, mais il est difficile de prédire l'avenir. On discute sans cesse du poids croissant des nacelles et de leur capacité à être soulevées d'un seul tenant. Je pense qu'on peut se projeter dans quelques années, mais pas beaucoup plus loin.
Tadano travaille également sur une nouvelle grue sur chenilles de plus grande capacité pour le secteur éolien, et l'entreprise doit la commercialiser au bon moment. Il s'agit d'anticiper précisément la demande future afin de répondre aux besoins du secteur en termes de capacité, sans toutefois la dépasser. Il faut que la livraison soit effectuée dans les délais.
C'est un aspect que nous avons pris en compte dès le début. Avec les grues sur chenilles à flèche en treillis pour le montage d'éoliennes, la stabilité de la flèche était primordiale pour toute conception de grue. Les éoliennes sont logiquement installées dans des zones venteuses, mais le vent peut bien sûr représenter un défi supplémentaire. Il est nécessaire d'avoir une flèche résistante au vent, quelle que soit sa direction, et notamment au vent latéral. Plus la flèche est longue, plus il est difficile de supporter les forces latérales.
Au début, les entreprises ont essayé de s'en tenir aux dimensions de transport européennes de 3,5 mètres de largeur, car au-delà, il est difficile d'obtenir des permis routiers pour le transport.
L'élargissement de la flèche, de 3 à 3,5 mètres, a permis d'améliorer la stabilité face au vent latéral. Mais ce n'était qu'une première étape, et les entreprises ont réalisé que cela ne suffisait pas pour atteindre de nouvelles hauteurs. Liebherr a alors inventé sa flèche parallèle, la flèche motorisée, composée de deux flèches parallèles. L'entreprise a utilisé deux flèches standard et les a placées côte à côte pour lever des charges plus hautes. Cette flèche plus large n'augmente pas la capacité de la grue, mais permet de lever les mêmes charges à des hauteurs plus élevées, ce qui correspondait exactement aux attentes de l'industrie éolienne.
C'était une excellente solution, mais le défi suivant résidait dans le manque d'efficacité matérielle d'une flèche parallèle. Le rapport poids/rigidité de la flèche n'est pas idéal. Il est préférable de concevoir une nouvelle flèche plus légère et plus rigide. C'est la tendance actuelle en matière de conception de nouvelles grues.
Ces flèches plus larges doivent être plus rigides, mais aussi pliables, car il est impossible de transporter une flèche de 6 ou 8 mètres de large. Le transport est donc important, mais la rapidité de montage l'est tout autant. Liebherr et Tadano ont tous deux mis au point des solutions complexes pour y remédier.
L'année dernière, Sarens a acquis la première LR 12500-1.0 de Liebherr, et la conception de sa flèche est vraiment intéressante. Il s'agit de la première grue dotée d'une superstructure spéciale en T et d'une flèche large de 7,5 mètres qui part du bas. Liebherr appelle cette nouvelle conception de flèche « Flèche Haute Performance ». Nous sommes convaincus qu'elle révolutionnera le secteur des grues à flèche treillis.
RESTEZ CONNECTÉ
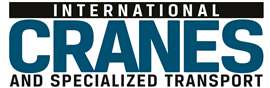
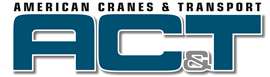
Recevez les informations dont vous avez besoin, au moment où vous en avez besoin, grâce à nos magazines, newsletters et briefings quotidiens de renommée mondiale.
CONTACTEZ L'ÉQUIPE
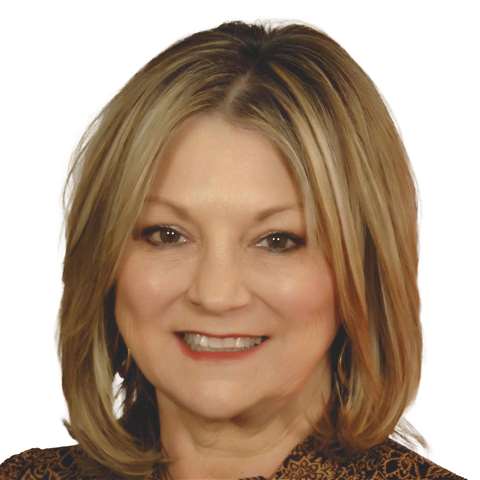
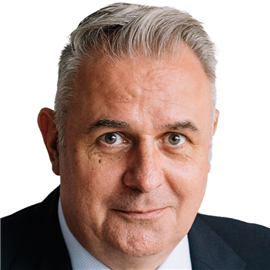
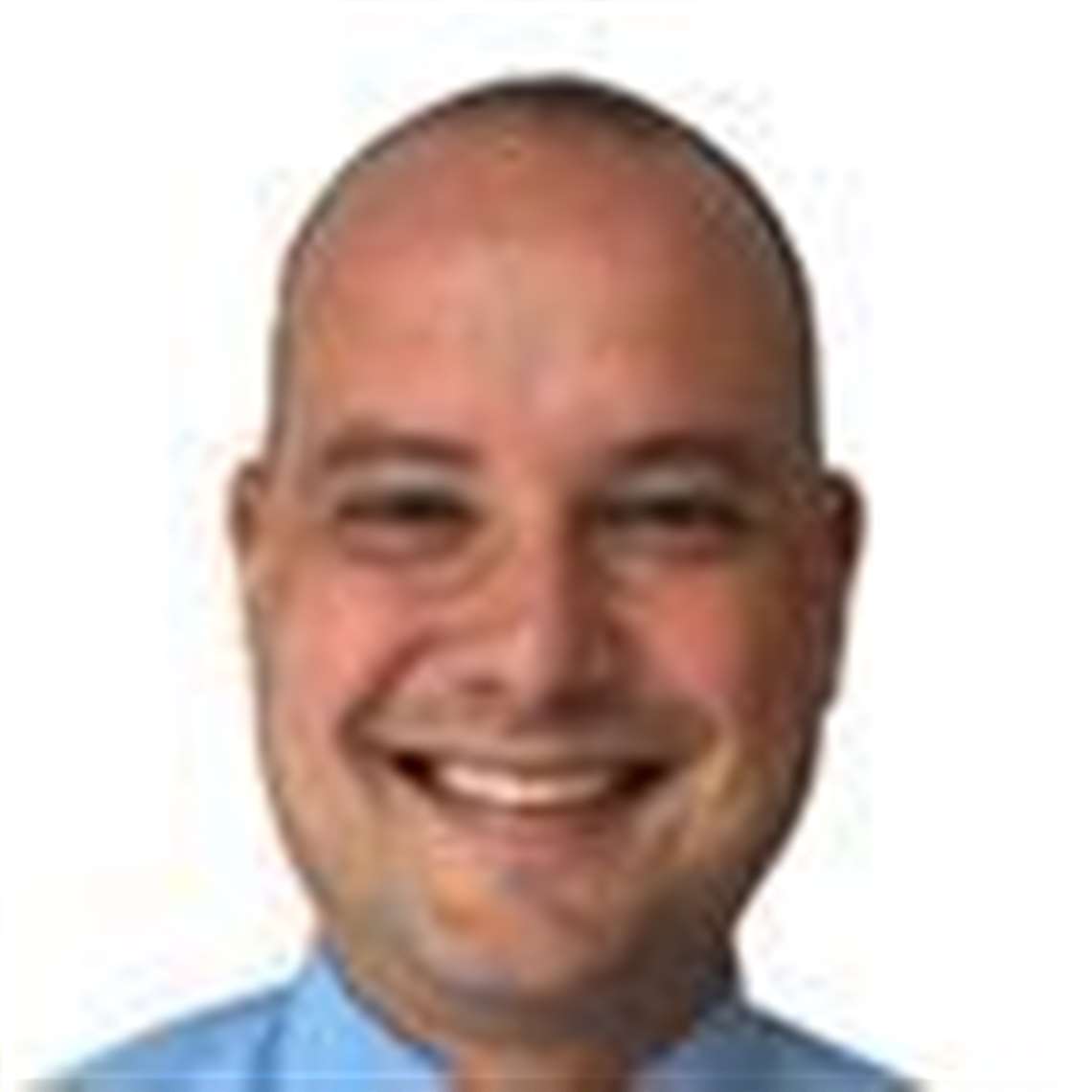
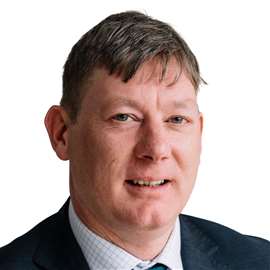