Read this article in French German Italian Portuguese Spanish
Breaking limits: How super heavy lift cranes are solving engineering challenges
23 December 2024
Heavy lifts from super big cranes aid the construction of a plethora of global infrastructure and industrial projects. Niamh Marriott reports.
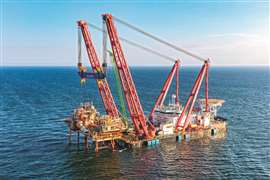
As engineering demands grow more complex, the need for specialized equipment, innovative lifting techniques, and careful planning becomes ever more critical.
Huge cranes, equipped with the latest technology, are reshaping the way we move and place the heaviest loads and are helping to drive progress across energy, construction and manufacturing industries worldwide.
In the works
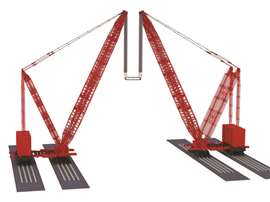
As previously reported by Crane and Transport Briefing, a whopping 14,000 tonne capacity land-based crane is planned for construction by a division of China Petrochemical Corporation (Sinopec). Sinopec Heavy Lifting and Transportation Co., Ltd. (SHLTC), based in Beijing, China, is planning to start construction of what will be – by a big margin – the world’s largest land-based crane of its type.
The new giant lattice boom super heavy lift crane, designed and developed in-house by SHLTC, will be used in China and further afield on the company’s projects, making major lifts in the industrial chemical, nuclear and offshore engineering sectors, the company said.
Construction is due to start in 2024 with testing completed by the end of 2026.
New crane
In October, Chinese heavy equipment manufacturer Sany delivered the world’s first 9 axle, 4,000 tonne all terrain crane, the SAC40000T, to a Chinese hoisting company, marking a historic milestone in crane design.
With the largest lifting capacity on the fewest axles, this machine is tailored for next-generation wind turbine installation, the company says. It features an 81 metre full-extension boom, 124 metre jib, and a maximum lifting height of 200 metres. Capable of lifting 375 tonnes to 100 metres at an 18 metre radius and 200 tonnes to 185 metres at 30 metre radius, the SAC40000T addresses the growing demand for equipment to support clean energy advancements.
Built on a compact 22 metre 9-axle chassis—the shortest in its class—the crane offers unmatched manoeuvrability with a 16 metre steering radius and 18 per cent gradeability. It is designed for rapid assembly, with single-side superlift setup in under an hour and reeving times under 70 minutes.
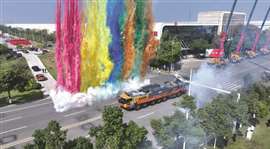
Intelligent safety features, including real-time boom monitoring and advanced signal systems, enhance operational reliability. The SAC40000T’s compact design sets a new industry benchmark, making it ideal for challenging terrain and high-demand wind energy projects, Sany added.
In describing the crane’s development, the product manager says, “We know there’s a growing need for powerful, precise equipment to drive clean energy forward. Current 2000t class can handle 7-8MW turbines. But 10-13MW turbines over the next 5-10 years? That’s why we bring 4,000 tonne AT to the table. Prioritising a compact, powerful design with fewer axles, we’ve enhanced its flexibility and ease of travel on rugged, mountainous terrain.”
Heavy collaboration
As previously reported by Crane and Transport Briefing, Dutch heavy lift company Mammoet launched its SK6000, which it claims as the world’s strongest land-based crane. A standout feature of this crane is its powerful rope winches, supplied by Liebherr. Designed with Liebherr’s advanced drive technology, these rope winches enable the SK6000 to handle exceptional lifting capacities, the company says.
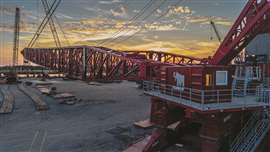
The SK6000 is capable of operating entirely on electricity, which helps reduce the carbon footprint of major industrial projects. Central to this functionality are the four Liebherr-supplied gear ring rope winches, each delivering a line pull of 600 kN, allowing the SK6000 to achieve its immense lifting capacity of 6,000 tonnes.
Both Mammoet and Liebherr worked closely to design and fine-tune the winches to meet the specific demands of the SK6000. This collaborative effort ensured the winches met not only the crane’s immense lifting requirements but also maintained compactness, a key feature for transport and assembly worldwide.
“Our collaboration with Mammoet showcases the versatility and strength of Liebherr’s drive technology,” says Markus Groeber, technical sales engineer, Liebherr Drive Technology. “For the SK6000, we equipped the winches with Liebherr’s own gear rings, gearboxes and electric motors, creating a system that offers unmatched lifting power and efficiency.”
Offshore moves
Heavy lifts for offshore work involve the precise handling and transportation of massive structures, such as platforms, turbines, or subsea equipment, often requiring specialized vessels and advanced engineering solutions.
Dutch offshore contractor Allseas successfully removed Shell UK’s 31,000 tonne Brent Charlie platform topsides from the UK sector of the North Sea.
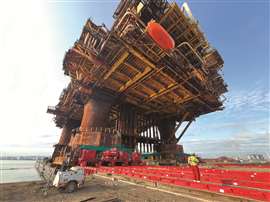
The single lift removal by Allseas’ vessel Pioneering Spirit is one of the heaviest offshore lifts ever performed, the company says, and concludes years of engineering and planning.
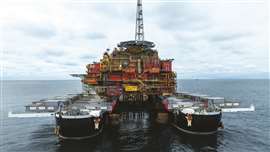
The former production facility will be delivered to Able UK’s Seaton Port facility in Hartlepool, northeast England for disposal, where more than 97 per cent of the materials will be recycled.
Edward Heerema, Allseas Chairman, says, “It started in 2013, with Shell’s decision to award Allseas the contract for the engineering, preparation and removal of its four Brent platforms. The trust shown then in Allseas’ technical expertise served as a milestone in the 20 year development of Pioneering Spirit. At the time, the vessel was still under construction, but Shell’s belief in Allseas gave us the opportunity to showcase our single-lift technology.”
The Brent decommissioning project is unique in its scale and complexity, comprising four platforms – three concrete-based and one steel jacket. Allseas has played a key role, performing the engineering, preparation and removal of all four platforms.
In executing Allseas’ scope, Pioneering Spirit has removed and transported close to 100,000 tonnes of topsides weight to Hartlepool for disposal at Able UK Seaton Port facility.
Power lifting
Netherlands-headquartered Heerema Marine Contractors successfully installed its first WTG monopile foundation project at the He Dreiht Offshore Windfarm, currently Germany’s largest offshore wind farm by power supplier EnBW.
A major milestone was reached when its semi-submersible crane vessel Thialf installed all 64 WTG monopile foundations, with each monopile measuring approximately 70 meters in length and weighing 1,225 tones, and each transition piece being 32 meters long and weighing 607 tonnes.
The installation was finished well within the agreed timeframe, with all activities, including full grouting, completed within 24 hours per foundation location.
“A key factor in our success was the dedication and expertise of our highly skilled crew aboard the Thialf, who, together with our specialized subcontractors, executed excellent installation cycles,” says a spokesperson for the project. “Moreover, these cycles were made possible by the efficient operation of Thialf’s dual cranes, the significant noise reduction achieved using the innovative T-NMS-10000, and the feeder barge concept, which ensured a continuous supply of monopiles and transition pieces to the vessel.”
Jörn Däinghaus, project director for He Dreiht at EnBW underlines: “We are very pleased that our joint planning with Heerema Marine Contractors has enabled such an efficient and smooth installation of the foundations. This is a key milestone for every offshore wind project. Together, we have taken another important step towards a more sustainable energy supply.”
When completed, the He Dreiht wind farm is expected to have a capacity of over 960 MW, providing renewable energy for approximately 1.1 million households. This project not only supports Germany’s energy transition, but also contributes to the European Union’s broader goals of increasing renewable energy capacity and reducing dependence on fossil fuels.
Electric dreams
Huisman has been awarded another contract for the delivery of a knuckle boom crane for a client in the offshore energy market.
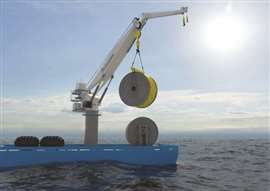
The 550 tonne capacity knuckle boom crane will be equipped with Huisman’s secondary-controlled active heave compensation system, which features the latest technology in load control for various offshore environments and energy management, the company says.
The crane’s boom is optimised for versatile operations on a pipelay vessel, offering an extended reach ideal for lifting objects onto the pipelay tower.
Huisman’s scope of work includes the complete range of engineering, production, installation, and testing, with a turnkey delivery from its facility in Schiedam, the Netherlands.
This contract marks Huisman’s third significant knuckle boom crane contract announced this year. The company’s new range of knuckle boom cranes include the potential for full electric active heave compensation. These cranes are designed to meet the growing demands of the offshore industry, ensuring reliable performance in various environmental conditions while minimising energy consumption. With these innovations, Huisman says it continues to set the standard for lifting technology, ensuring clients can achieve their project goals with greater efficiency and a lower environmental impact.
Wind farm
Marine engineer Seaqualize lifted 11 MW turbines to Van Oord’s offshore installation vessel the Aeolus to help complete the first commercial scale offshore wind farm in the USA.
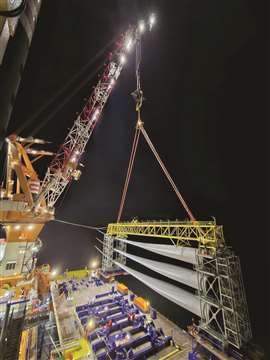
It was the first time this operation was done using a new turbine feeder operation.
During the project, the Seaqualize HC750 and its operators were responsible for safely transferring over 25,000 tonnes between the barge and the Aeolus. First, the HC750 followed the barge motions to ensure the Aeolus crane could safely connect with the component. Then, the HC750 tensioned the crane rigging, while keeping the wave heave motions compensated, and lifted the components off deck. This way, the turbine components such as towers, nacelles and blade racks, weighing up to 750 tonnes per piece, were protected from hitting the deck. After everything was safely lifted off, the HC750 placed the secondary lifting equipment back on the barge, for the next load out.
Wytze Kuipers, project manager for offshore wind at Van Oord says, “Many said feedering turbines in the open ocean would be too complex, especially in the winter season. But with good team work and innovations like the Seaqualize Heave Chief, we’ve shown it can be done.”
Eni UK Limited has awarded Scaldis a contract for the engineering, removal, transportation and disposal of six Eni Hewett platforms in the Southern North Sea of the UK.
The offshore operations are scheduled to take place in 2024, 2025 and 2026 with preparatory works and modules lifts being carried out by the Heavy Lift Vessel Rambiz, and the main lifts being executed by the heavy lift vessel Gulliver.
Scaldis successfully and safely lifted the first Eni Hewett platform this summer.
The heavy lift industry continues to push boundaries with groundbreaking innovations and record setting projects across construction, offshore energy, and industrial sectors, meeting growing demands for precision, capacity, and sustainability. As technology evolves, these transformative capabilities not only support massive infrastructure projects but also contribute significantly to global sustainability goals.
STAY CONNECTED
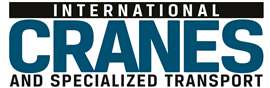
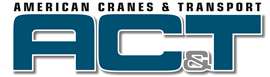
Receive the information you need when you need it through our world-leading magazines, newsletters and daily briefings.
CONNECT WITH THE TEAM
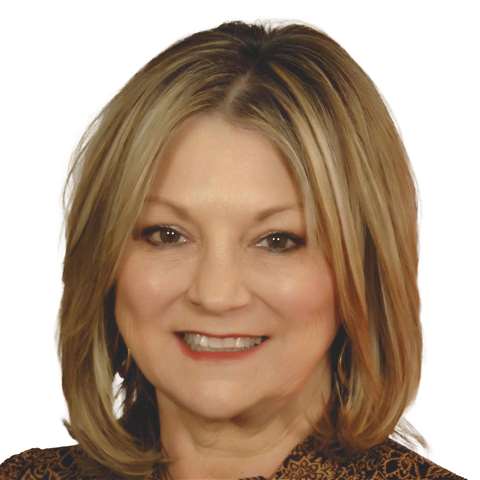
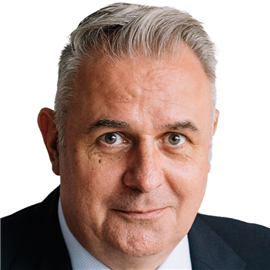
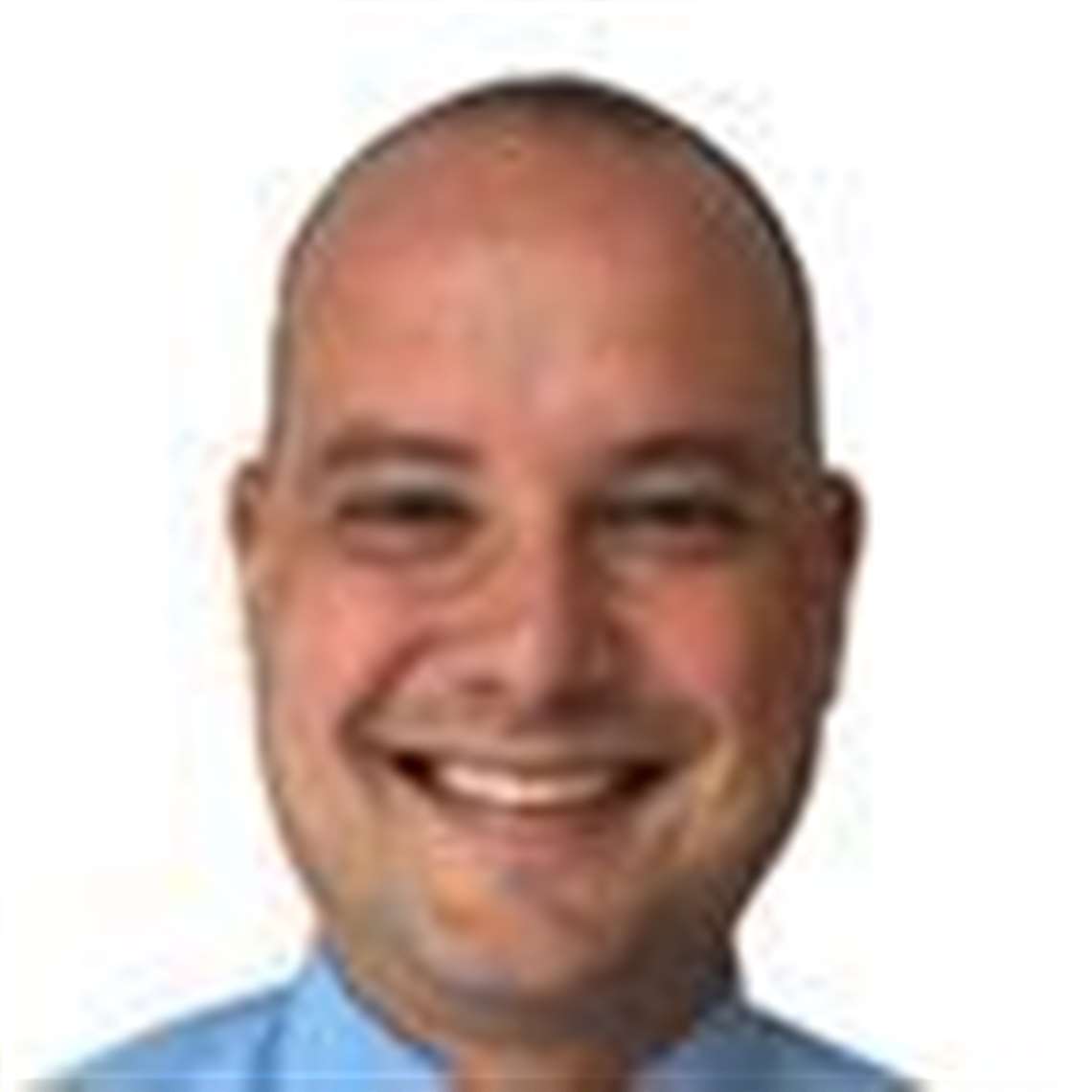
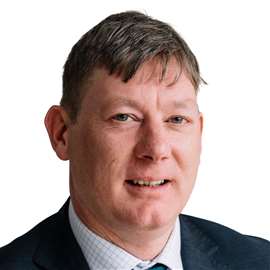