Is construction losing out on efficiency gains by using too many tower cranes?
09 May 2023
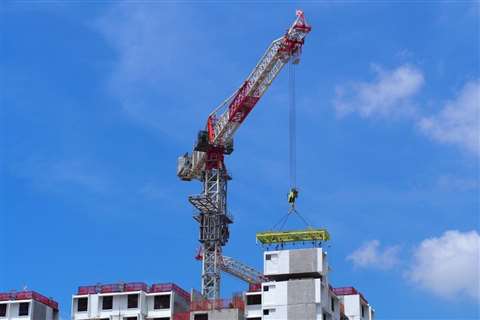
A city skyline bristling with tower cranes is normally taken as a good omen in the world of construction.
It suggests strong client demand and bulging order books as contractors work to fulfil tenders.
Some consultancies and planning firms even publish tower crane indices that judge the health of a region’s construction market by how many cranes stand above its cities.
But what if having so many hooks hanging above a site is actually a sign that a construction site could be operating more efficiently and more profitably?
Construction methods are modernising gradually as prefabricated prefinished volumetric construction (PPVC) and other offsite manufacturing techniques gain in popularity.
Progress is uneven across the world, however, with some markets like Australia, Singapore, and the Middle East taking a lead while others adopt a more conservative approach.
Prefabricating larger, heavier building elements requires bigger, more powerful cranes to lift them.
Crane manufacturers have started to cater to that demand (see below).
Whereas five years ago a mainstream manufacturer’s range might have topped out with a 32t tower crane, that has now extended to 50t or even 64t.
There’s also a trend towards a flat top design for faster setup times and a lower overall height. It’s also easier to change job and counterjib lengths on a flat top crane.
Contractors missing opportunity for greater efficiency
“Over the past 20 years, we have been continually upsizing the cranes in Australia as the construction methodology changes,” says Simon Marr, director at Australian crane specialist Marr Contracting.
While countries like his own have embraced PPVC and the larger cranes that go with it, others are still catching up. And Marr can see a missed opportunity for greater efficiency, speed and ultimately profit that contractors are currently losing out on.
During a visit to London, where Marr Contracting has an office, he explains that the approach in the UK and other parts of Europe is still much more traditional. “Here, it’s very much still about lifting 2t beams and that seems to be a really inefficient way to build,” he says.
“Whereas, we have a job back home at the moment on a structural steel building where we are lifting trusses of 120t. Why are we doing that? We are trying to take the risk out of the project.
“You see a lot of jobs where there are just way too many cranes. They can’t work because they are falling over each other. They are slow and costly because you need more labour, more engineering and more temporary works on your structure.”
Marr argues that prefabrication enables contractors to use fewer, bigger cranes to lift larger, prefabricated building elements that have been assembled on the ground under conditions that are safer for workers.
“Often, clients will say to us: ‘But we need more hooks on the job.’ But often you don’t need more hooks – you need to understand what you are lifting and what you really need to do is reduce the number of lifts on the job. And you do that by making the pieces bigger,” says Marr.
‘Fear of change’
Marr attributes a reluctance in some markets to considering using a single larger crane coupled with modern methods of construction to a fear of change.
But he is seeing a gradual shift in attitudes. “We look at it and think there is an opportunity you are leaving behind here. There is a better way to build and more margin in it for you if you want to adopt a different method.
“But you have got to be brave and take the first step towards a different way of constructing,” he says.
As the methods change, the challenge becomes how to get material to the crane quickly enough because its lifting efficiency has improved, he adds. And he asserts that larger cranes with high-capacity, high-speed lifting “blow the smaller fleet out of the water” in terms of how much material they can move onto a project.
But he also stresses the need for early engagement with clients – as was the case on the Çanakkale 1915 suspension bridge in Turkey, which saw Marr Contracting’s cranes lifting loads of around 160t up to a height of 300m. “That was really about early engagement with the client and completely turning upside down their construction methodology,” he says.
“By modularising all of your components offsite, you have better control of your tolerances and we can bring the modules in and lift them up in big chunks.”
The bridge finished nearly two years ahead of schedule.
Prefabrication drives manufacturers to produce bigger cranes
One manufacturer that has taken note of growing demand for larger cranes is Liebherr.
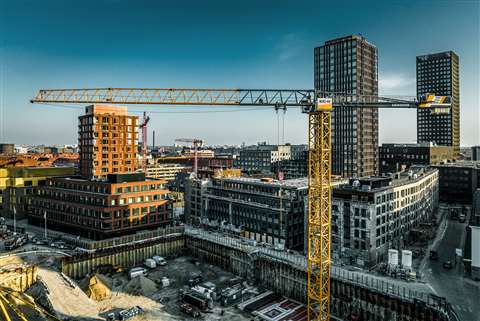
“We see a trend for larger and heavier prefabricated parts, with the aim of shortening construction times,” a spokesperson for the company says.
“Construction with prefabricated parts varies from country to country. This is one of the reasons why Liebherr introduced new series-produced larger cranes for its successful series last year.”
Those cranes include the new 1188 EC-H 40 Fibre, with a maximum lifting capacity of 40t, which has been designed to move heavy precast parts into position. The crane, which is Liebherr’s strongest series-production crane lifts up to 13.1t at the top and has a maximum reach of 90m.
Meanwhile it has extended its EC-B series updates with the 520 EC-B 20 Fibre and 470 EC-B 20. The flat top cranes offer a maximum load capacity of up to 20t.
Spain-based tower crane manufacturer Jaso has also seen an upswing in demand for larger machines.
Theodor Peter Huitema, area manager for Jaso, says, “The growing trend towards PPVC, particularly in Asia, has led to increased requests for cranes with heavy duty lifting capacities.
“As a response to this demand, Jaso designed the J1400; it has an 80m-long jib and can lift a maximum load of 64t and 10.5t at tip load. The first four units of this model have been purchased by Singapore-headquartered Crane World Asia.”
Jaso’s second biggest unit from its range is the J800.48, which has 80m reach and a maximum load of 48t.
Huitema says the demand for large tower cranes for PPVC projects extends beyond just Singapore. The company is also working on projects in Australia, Hong Kong and the USA and markets like Sweden and the Netherlands also make use of large cranes to lift heavy pre-fab units. On a smaller scale, he notes, there are also pre-fab and pre-fabricated bathroom unit (PBU) projects in Chile and Spain, driving demand for cranes in the 500-700tnm class.
“This trend is set to grow because of an increasing lack of labour and more building with prefabricated modules,” he adds.
STAY CONNECTED
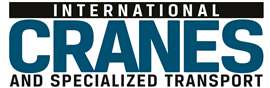
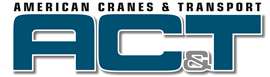
Receive the information you need when you need it through our world-leading magazines, newsletters and daily briefings.
CONNECT WITH THE TEAM
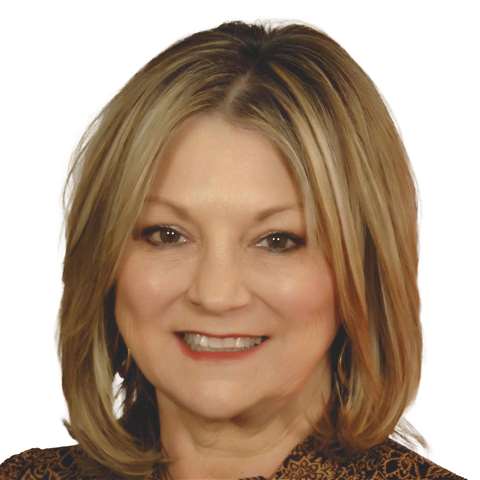
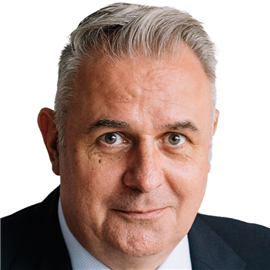
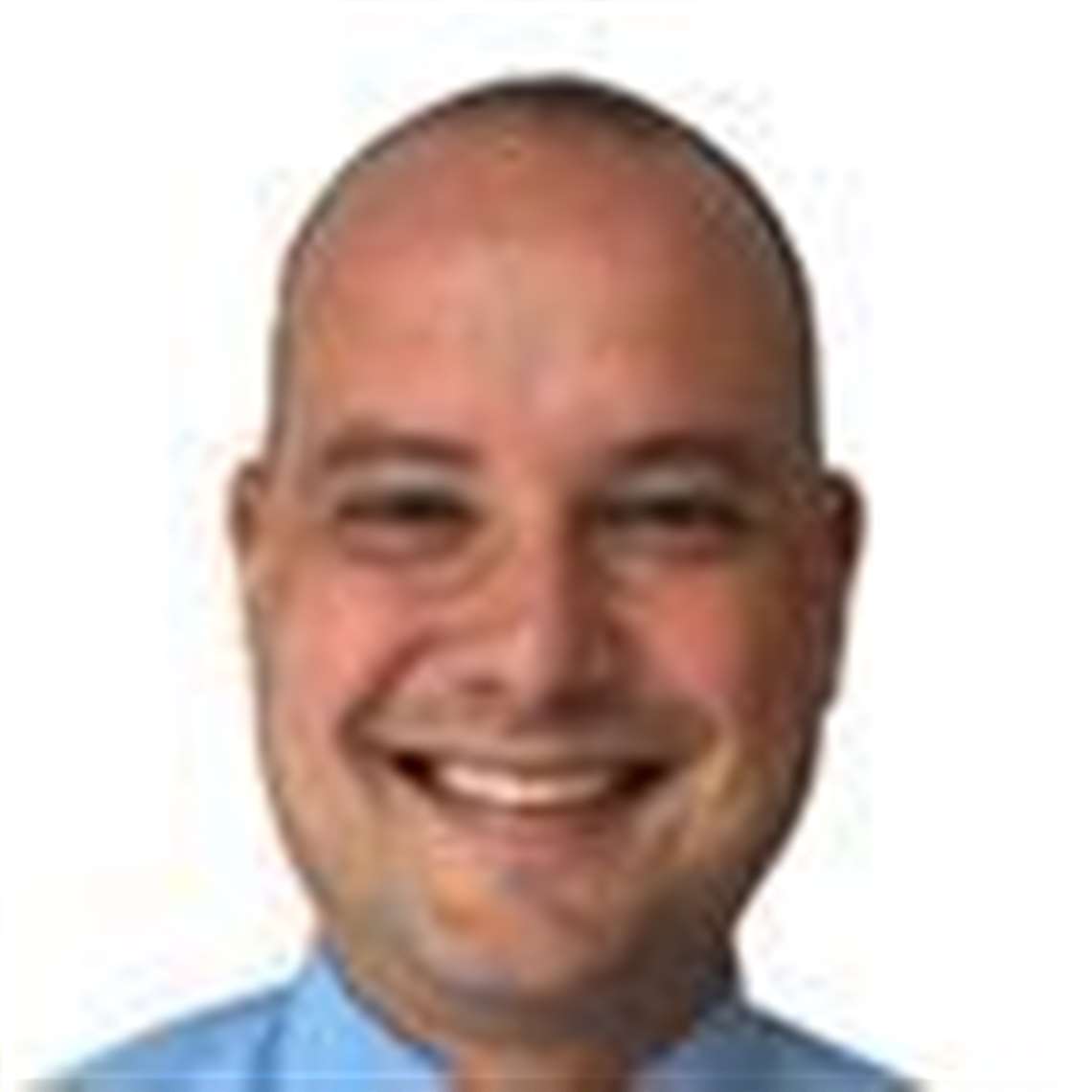
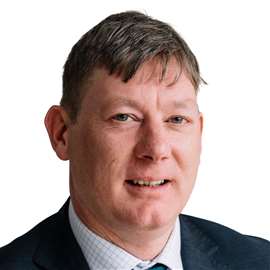