Read this article in French German Italian Portuguese Spanish
Wire or synthetic? How to choose the right rope for the job
28 February 2024
New rope technology gives operators options for lifting work. Niamh Marriott reports.
New products lead the biggest trends in the rope market, says a recent Technavio market research report. It says major company innovations and product launches are expected to attract more end users and help companies increase consumer reach.
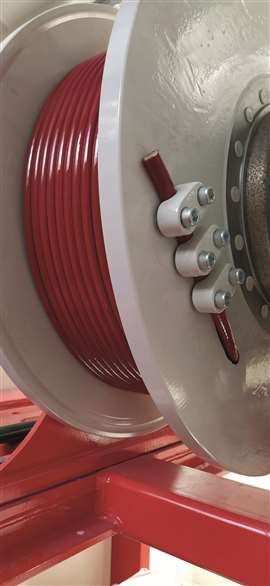
Furthermore, there is an increasing effort in the market by major players to replace the conventional raw materials used in rope production with modern options that have no negative impact on the environment in the production process.
For example, the Euro block VF winch uses Dyneema rope, made using an ultra-lightweight polyethylene fibre that is up to 15 times stronger than steel. These ropes are highly resistant to abrasion, moisture, UV rays, and chemicals. In addition, they also have high energy absorption and very low elongation.
Staying strong
As the rope debate continues – synthetic fibre or steel wire – there are new options coming to the crane market.
Due to properties such as a higher strength-to-weight ratio, synthetic fibre ropes are light and easy to install.
“Fibre ropes, up to seven times lighter than steel ropes and easier to handle, offer significant advantages,” says UK-based industrial equipment supplier Rotrex Winches. “They are compatible with water and corrosive environments, where they can resist rust damage and degradation. Fibre ropes are ideal for offshore projects or marine and port operations.”
“Additionally, fibre ropes are safer than steel ropes, as they do not snap back if broken, reducing the risk of injury for those working nearby. While more flexible than steel ropes, fibre ropes have lower strength and crush resistance.
There is, however, still a case for steel ropes in certain applications, Rotrex says. “Steel or wire cables, typically stronger than fibre ropes, are ideal for winching or lifting heavy equipment. They offer greater crush resistance and a higher nominal strength compared to fibre ropes, but they are not as flexible.
“One advantage of steel rope over synthetic rope is its increased resistance to cutting or melting. Steel ropes can be used in environments over 60 °C (140°F) without losing their lifting capacity, whereas synthetic fibre ropes typically lose capability at around 65 °C (150°F).”
The Rotrex Group has invested heavily in its fibre rope capabilities and can now offer an equal choice of steel or fibre ropes to meet industry demand.
While Technavio’s report suggests the steel wire segment is estimated to witness significant growth, synthetic options continue to be explored.
“Synthetic rope continues to grow in popularity for utility, trailer and towing, construction, military as well as other applications,” says a spokesperson for USA-based manufacturer Paccar Winch.
“Replacing traditional steel cables can drastically reduce the overall weight of any towing or utility vehicle, particularly those with multiple winches.
“Abrasion-resistant and easy to inspect, synthetic rope is torque neutral, which means it will not twist and is much easier to handle.”
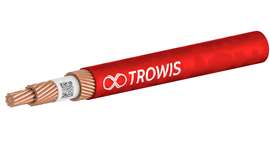
Synthetic alternative
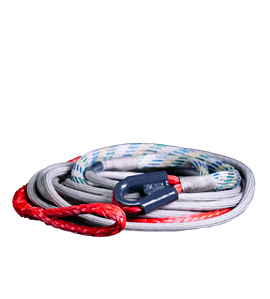
Paccar Winch has added a new TRS synthetic rope to its Braden product line. The rope has been engineered and tested to complement its TR series planetary recovery winches, which have rated line pulls up to 13.6 tonnes.
Rope diameters and lengths suited to specific winch drum sizes are available and it is a suitable alternative to wire rope. Four times lighter than comparable sizes of steel rope, the synthetic rope helps mitigate the overall weight of equipment transported to site.
As vehicle manufacturers continue to explore battery electric vehicle (BEV) technology, it will become increasingly important to minimise the weight of accessories to balance the overall gross vehicle weight rating (GVWR).
The Braden TRS range is a UHMPE (ultra-high molecular weight polyethylene) 32-carrier with a polyurethane coated braided sleeve over a Vectran LCP (Liquid Crystal Polymer) 12-strand inner load bearing core to make it stronger and more durable. Each rope has two eye splices, one for anchor wedge attachment to the winch drum and one on the outer end with a thimble spliced into the eye with a UHMPE protective chafe layer at the throat of the splice.
The rope is non-crushable, abrasion resistant, easy to inspect and torque neutral, which means it will not twist and is much easier to handle than wire, the company adds. The rope is available in rope diameters from 11 to 16 mm and lengths from 24.4 to 64.0 metres.
Easy switch
As previously reported, tower crane manufacturer Wolffkran demonstrated a synthetic fibre hoist rope to replace conventional steel wire hoist rope at the Bauma Munich construction trade show in 2022.
Its chaRope, developed with rope specialist Trowis, is “the only fibre rope that can replace a steel rope one to one,” Wolffkran says. It was shown at the trade exhibition on a Wolff 6021 FX flat top tower crane and since being launched to market, it has been field tested on Wolffkran’s UK rental fleet.
The chaRope fibre rope is roughly 80 per cent lighter than a steel rope. This saving in weight not only enables greater lifting capacities but also significantly easier and safer handling during transport, assembly, and rope changing.
In addition to the usual advantages of fibre rope over steel, Wolffkran says, substitution of steel with the new rope can be done without any modification to the crane.
American demand
It is not just the choice of material that is impacting the rope market – changes in manufacturing processes and environmental concerns are also at the forefront of the industry.
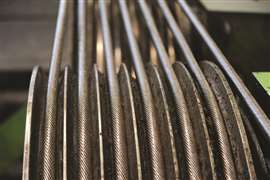
“Production facilities must have the ability to evolve and adapt as innovations in materials, coatings and manufacturing processes continue to alter the wire rope industry,” Andreas Schmeiss, global crane industry leader for WireCo World Group, comments to ICST sister magazine American Cranes & Transport.
“Leaders continue to develop stronger, more durable products capable of functioning in harsh environments while maintaining wide usage across a variety of industries.”
Over the past two years, WireCo has invested US$30 million in new machines, technology, facility upgrades and processes, including internal and external quality testing programmes, to support the infrastructure boom. WireCo invested $25 million to expand production capabilities in its Sedalia, Missouri, facility in the USA.
This focus on the US market was deliberate, responding to customers’ respect for and recognition of the company’s brands and products.
“We believe strongly in the US market and the infrastructure boom that is happening, both direct and indirect spend,” says Keith White, WireCo CEO. “We know the industry will need ropes as soon as possible, and that operators want to go with brands they trust. By making this investment, we’ve significantly increased our output and capacity and, most importantly, our ability to meet lead times and demand for our most valued partners.”
OFFSHORE OPERATIONS
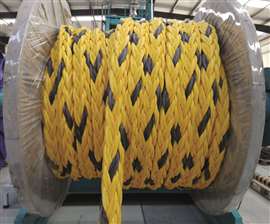
Without fibre ropes, many of today’s deepwater projects would be beyond all but the largest cranes, says Lankhorst Offshore. The weight of steel wire ropes makes wire rope lifting and lowering systems both inefficient and impractical at water depths greater than 2,000 metres. Development of the Lanko Deep AHC fibre rope by Lankhorst Offshore, part of Netherlands-based Lankhorst Ropes, is bringing deepwater projects within the reach of smaller, more cost effective lifting systems and vessels.
LankoDeep is based on Dyneema DM20 XBO optimised for cyclic bending. It is made up of 12 strands where each strand comprises a three-strand rope. This construction, combined with the proprietary yarn coating reduces internal heating and abrasion.
Lanko Deep AHC fibre rope was designed from the outset for deepwater lowering and recovery projects. The company says it offers significant operational and environmental benefits compared with steel wire ropes. Operationally the ropes are easier to handle and allow engineers to lift and deploy the maximum load without the need to factor in the self-weight of steel wire.
“Neutrally buoyant LankoDeep allows operators to maximise the lifting capacity of their crane during deepwater deployment and recovery. With the introduction of the new DNV certified end-to-end splice we’re considerably increasing the utility of LankoDeep, ensuring deployment and recovery operations run smoothly,” says Sergio Leite, Lankhorst Offshore sales director.
MAJOR WINCH ORDER
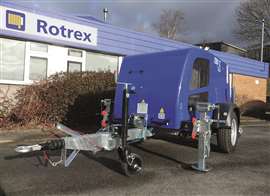
Rotrex Group has become the biggest provider of 4 tonne winches in the UK after it placed an order with Italian manufacturer OMAC for its UP40 winch.
The company, an exclusive distributor in the UK for OMAC, says the order for the UP40 winch comes off the back of growing popularity in the UK due to its “exceptional capabilities and features.”
It has a maximum pull of 40 kN, maximum speed of 65 metres a minute, a 12 mm maximum rope capacity and steel rope fitted up to 1,300 metres.
Other features include a light composite material canopy, built-in technology, including onboard wi-fi for data transmission and data recording technology.
STAY CONNECTED
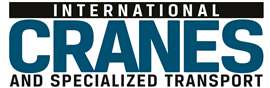
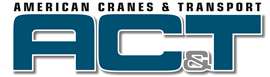
Receive the information you need when you need it through our world-leading magazines, newsletters and daily briefings.
CONNECT WITH THE TEAM
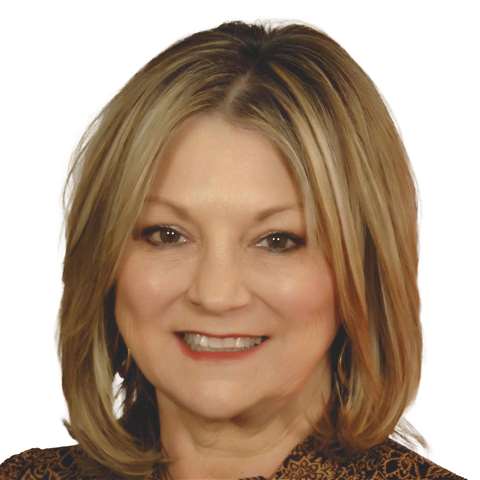
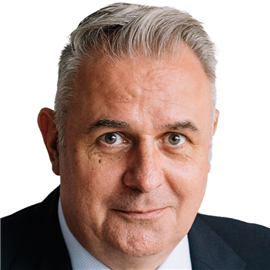
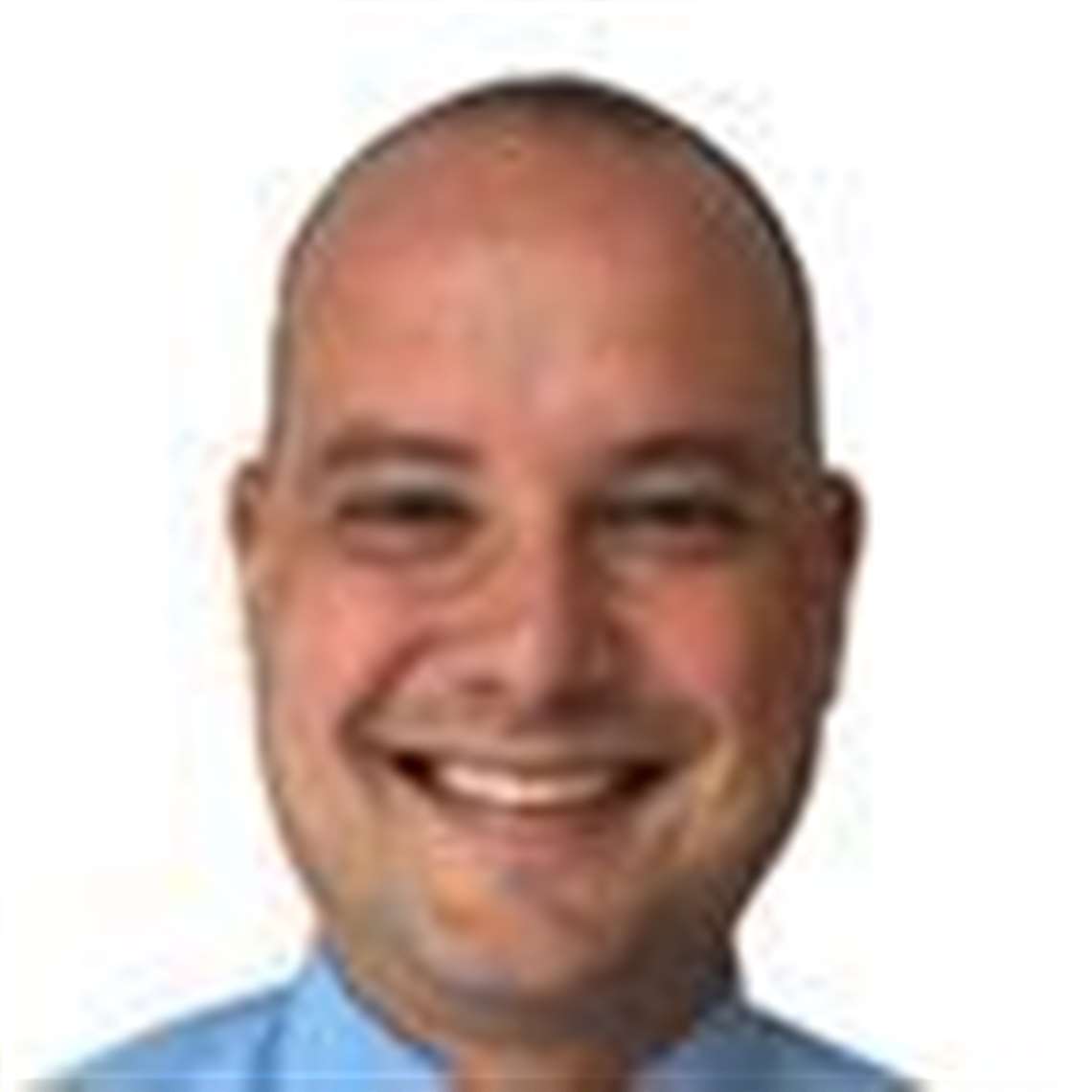
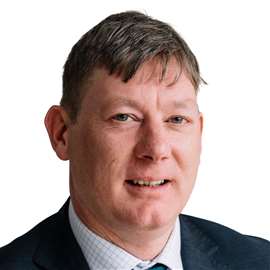