Mammoet in 3,000 tonne load out milestone
26 February 2025
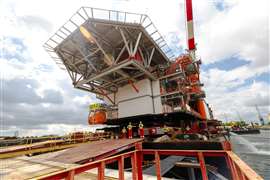
Contractor HSM Offshore engaged international heavy lift and transport specialist Mammoet for a load out on a landmark project.
It was for the first wind-powered offshore gas platform in the Dutch North Sea. The N05-A platform uses electricity delivered via an undersea cable from the nearby 113.4 MW Riffgat offshore wind farm.
Using wind energy is expected to reduce carbon dioxide emissions by more than 85 per cent over the life of the platform.
Mammoet said its engineering approach allowed the jacket to be assembled more efficiently and reduced the construction lead time.
The job was done at HSM Offshore’s quayside yard in Schiedam, Rotterdam, Netherlands, close to its own yard. It loaded out the 3,150 tonne jacket and the 3,050 tonne topside to go on top of it. Both were loaded onto a barge and then shipped out. ONE-Dyas, owner of the platform, then managed the sailing and installation out at sea.
Back to the fabrication yard, the jacket and the platform were assembled and weighed using mobile cranes, trailers and slf propelled modular transporter (SPMT). The jacket was fabricated in sections and then brought together using heavy transport. It was then upended using four Liebherr wheeled mobile telescopic cranes: two 700 tonne capacity LTM 1650-8.1s and two 450 tonne capacity LTM 1450-8.1s. Installation of the jacket’s pile sleeves was done with a 750 tonne capacity wheeled mobile crane.

Putting it together
For final assembly at the quayside the top section was lifted by two heavy lift sheerleg vessels. That lift gave enough space for the bottom section to be driven underneath on trailers so the two sections could be joined.
For the topside which was built indoors, SPMT was driven underneath it so it could be moved outside and driven to the quay. While there Mammoet used trailers and its mobile cranes to mount a pedestal crane on the superstructure.
The completed topside and jacket were loaded separately onto SPMT before being weighed using Mammoet load cells to determine their final weights. Four files of 32 axle lines of SPMT were deployed.
To meet the schedule both modules were loaded onto the same barge. Normally they are shipped separately. In this case it presented engineering challenges and there were issues with space. Room had to be found on the vessel for pumps and winches and there had to be a different mooring arrangement.
On the mooring
“The mooring was quite critical, and we had to do a lot of engineering,” explained Sven Segeren, project manager at Mammoet. “Normally, we would use a configuration of winches to moor and stabilise the vessel but that wasn’t possible because of the force of the considerable loads.
“The loads on the winches were too high and the bollards not strong enough, so a small spud leg barge was used to secure the vessel and keep it in position prior to, during and after load-out.”
Preparation of the main barge took five days, installing the ballast pumps, pre-ballasting and then checking sailing conditions for the voyage.
Both modules were loaded out in a two-day operation.
“We work a lot with HSM Offshore. They always involve us at the beginning of projects, so we can help them with smart solutions for assembly,” said Segeren.
STAY CONNECTED
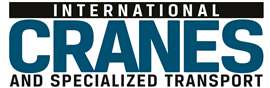
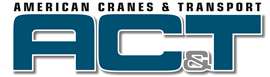
Receive the information you need when you need it through our world-leading magazines, newsletters and daily briefings.
CONNECT WITH THE TEAM
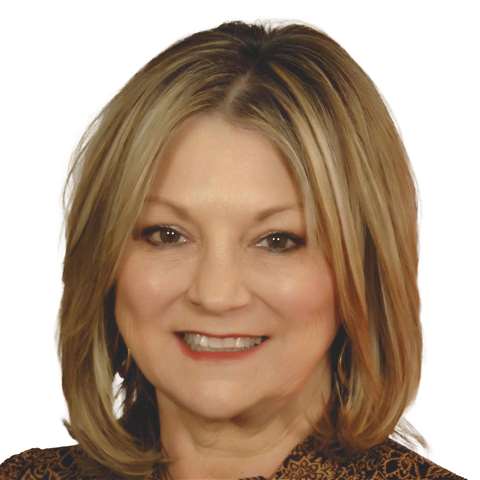
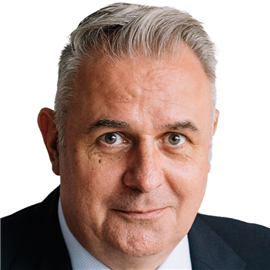
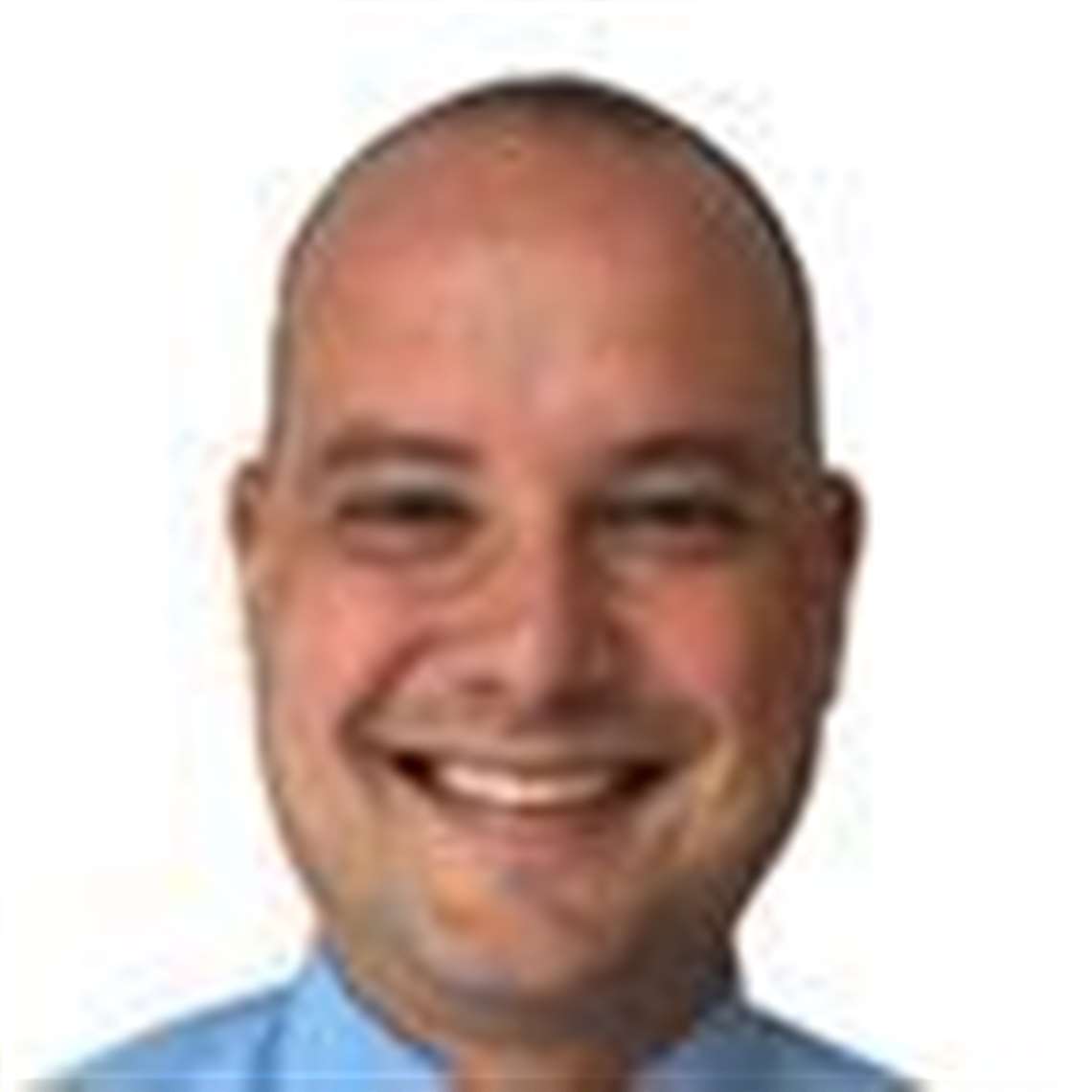
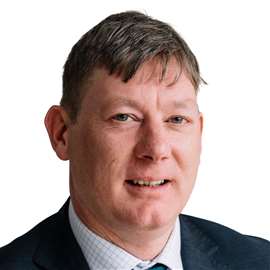