Read this article in French German Italian Portuguese Spanish
Choosing the right crane for tilt-up construction
12 January 2024
Tilt panels are precast walls that are built horizontally on the ground with lifting inserts built into them. They are designed so that a crane or cranes can lift the panel into a vertical position to become the walls of a building.
The tilt-up market is very competitive for both those building the panels and the companies hired to erect them. Tilt panels are popular for warehouse construction because the walls can be erected quickly, shortening construction time.
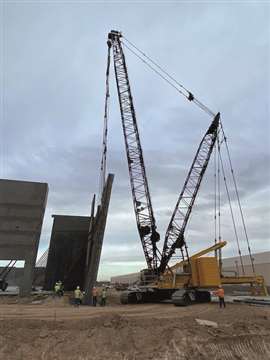
Generally, one crane lifts all the panels for a given building into place. There are occasions, however, where it is necessary to perform a tandem lift with two cranes to pick up a panel due to its weight or placement. However, tandem lifts don’t happen often because a higher capacity crane can often perform the work required.
Numerous factors are considered when choosing the right crane for a tilt-up project. At Marco Crane, we look at the weight of the panels, placement on the floor or casting slab, if we can perform the lifts from outside the building or up on the floor, and site access both at the beginning of a project and after the panels have been erected. Crawler cranes are typically the most common cranes used for tilt-up jobs in today’s market. They have larger capacities, can walk with a load and can move around a jobsite faster with less setup time than truck cranes.
From an operator standpoint, experience is very important to a crane company’s tilt panel customers. Customers view a crane operator’s experience just as important as the crane that is chosen for the project.
Rigging know-how
In the Southwestern United States, where Marco Crane erects many tilt panels, operators have learned to adapt to different jobsite situations. One example is offsetting the rigging to account for pick points that may have been placed in the wrong position. Another is recognizing the way a panel bows during the beginning of the lift cycle. A panel may have to be laid back down on the slab and have strong backs installed to assist with supporting the panel until it is in the vertical position.
Beyond crane fleet variety or pricing, customers will choose a crane company because of the experience of their operators, a major factor in this type of work. It’s important that a contractor is comfortable with the crane company and its operators. They want to be assured that this work can be performed in a safe and efficient manner.
Tilt-wall construction has evolved greatly through the years, and the crane needs are trying to keep pace with the industry’s demands. In the early years of tilt-wall construction, lattice boom truck cranes were the machine of choice.
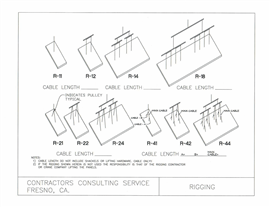
Marco Crane performed its first tilt panel job around 1970 with a 1957 Bay City crane with 55-tons capacity. Today, our most common crane used for tilt-up work is our 386-ton Manitowoc MLC300 lattice boom crawler crane. Back in the 1970s, panels typically weighed around 30,000 to 40,000 pounds. Today’s tilt panels are in the 250,000-pound range. The heaviest tilt walls ever lifted by Marco Crane were just under 500,000 pounds, not including the rigging.
Tilt-wall construction has even evolved from a typical single-story building and the occasional two-story building to buildings that are three and even four stories tall. Due to the number of windows in multiple story buildings, the length of the slings used on a tilt wall job has increased. In some cases, we are using primary slings that are 85-feet long and secondary slings that are 65-feet long to spread the load during the lift cycle from horizontal to vertical. Due to the increased height of the panels today, and the capacity of the crane used, longer booms are necessary. It’s not uncommon to see boom lengths ranging between 157 to 197 feet for a tilt panel rig.
For Marco Crane, heavy lift attachments are often installed on our MLC 300s once the panels begin to approach the 300,000-pound range. These attachments are needed to accommodate the heavier panels or distance to where picking and placement takes place.
Rigging evolution
Rigging has also evolved through the years. In the 1970s, most panels had four pick points, two high by two wide. Today, a large panel can have as many as 16 pick points or use the 16-pick point rigging design with “double lifters,” which gives you a total of 32 pick points installed when a panel is built. We will keep adapting to the evolving market of tilt-up work.
Safety is the primary concern of everyone associated with erecting tilt panels. Although it is not common, there have been instances through the years where pick points have pulled out during the lift cycle. There are also instances where the ground has failed to support the crane and the load.
In the early days of setting tilt panels, sometimes the crane’s capacity was exceeded causing a tipping condition. But today, there is an immense amount of preplanning that goes into a tilt-up job with numerous preconstruction meetings, computer-generated lift simulations/lift plans for the cranes and the rigging. Every element of the project must go through an approval process by several entities. Geotech surveys are often conducted to ensure ground stability, and if necessary, steel plates and wood mats are brought in to reduce the ground-bearing pressure.
A company’s safety record has become as important, if not more important, than the service capabilities they provide.
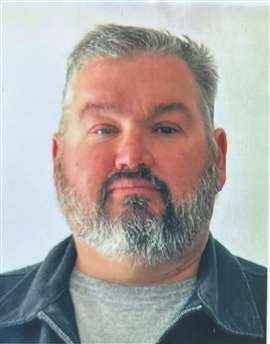
THE AUTHOR
CJ Ryan is Crane Superintendent for Marco Crane & Rigging. He is a second-generation crane operator with over 30 years of experience with tilt-panel erection.
STAY CONNECTED
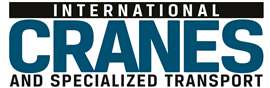
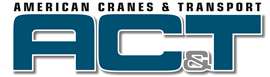
Receive the information you need when you need it through our world-leading magazines, newsletters and daily briefings.
CONNECT WITH THE TEAM
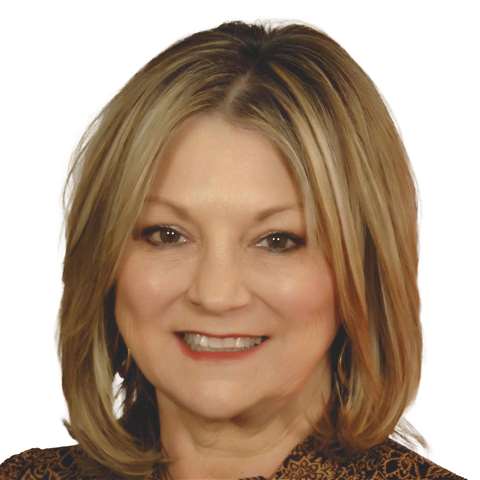
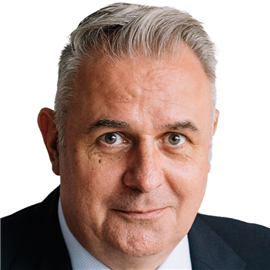
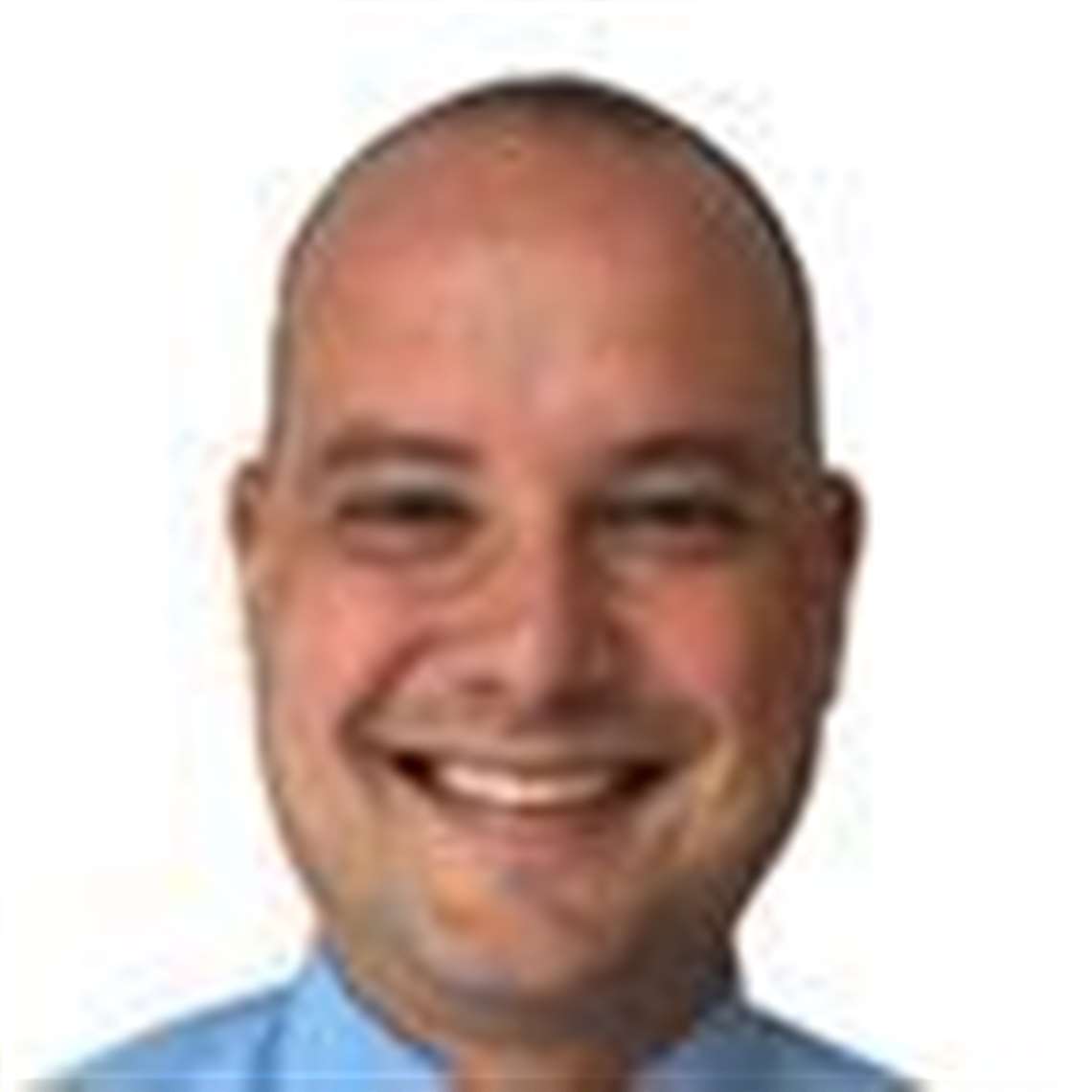
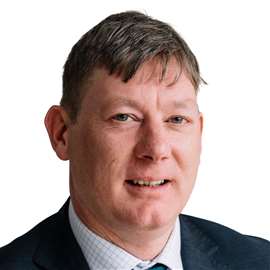