Read this article in French German Italian Portuguese Spanish
Creative use of SPMT
03 March 2025
Engineering teams are solving a variety of heavy haul and rigging project challenges using self propelled modular transporters.
Self-propelled modular transporter (SPMT) has long been considered an innovative tool for moving huge and heavy pieces of equipment, vessels and even buildings through plants and over the road. With their modular features and adept maneuverability, engineering teams can get really creative when solving heavy haul and rigging project challenges.
Tailing solution
JMS Crane Service in Billings, MT reached out to Bay Ltd. in Texas for a solution for tailing three reactors inside a Montana refinery. The tailing path required special attention to the ground bearing pressures (GBP). The Bay Ltd. team was challenged to produce minimal GBP on the tailing “runway.” With a lift weight of just over a million pounds each, traditional means of a crawler crane for tailing was quickly eliminated.
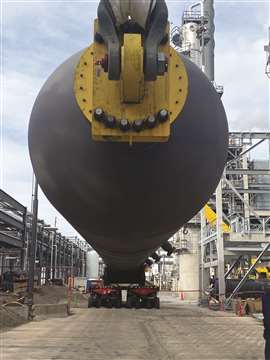
After much discussion and planning, the Bay Ltd. team decided to use their custom engineered tailing frame “DINO” set atop of a 4-file 10-line Scheuerle SPMT. Each reactor was hauled into the unit from a remote lay-down yard by a 15-line Goldhofer THP SL45 where the upper tail frame of “DINO” was installed on the skirt of the reactor. The Goldhofer then transferred the skirt-end with the upper frame to the lower frame of “DINO” on the Scheuerle system, and the head end to the lift crane.
Removing the now empty Goldhofer from the tailing path provided challenges as mere inches of lateral movement were left for an exit. Once the Goldhofer was out of the way, each reactor was tailed up flawlessly. All three reactors were hauled into the unit and set in place in an astonishing two shifts. Other challenges to overcome included: maneuvering under existing pipe racks, bridging culverts, turning each reactor 180 degrees before entering the unit and hauling the reactors over the crane pad while the crane was still on the pad.
Mind the gap
Heavy transport specialist Berard completed the installation of the Interstate 10/Interstate 12 Flyover Bridge in Baton Rouge, LA using Scheuerle’s SPMT technology. For the transport and placement of the approximately 250-ton bridge segment, Berard deployed 72 axle lines and eight Power Pack Units (PPUs). One of the primary challenges was navigating the tight space constraints on the construction site. The SPMTs were configured in a double-stacked setup to ensure the necessary maneuverability and balance in the limited space available.
Despite the challenging conditions, the bridge segment was placed with a deviation of only a quarter inch (approximately 6 millimeters) from the designated position. This demonstrates not only the reliability of the technology used, but also the high level of competence and experience of the Berard team in precise load movement, Berard said.
Another critical factor in the project’s success was the efficient control of the PPUs, which ensured an even distribution of power across the axle lines. This provided stable and smooth transportation, even on uneven surfaces.
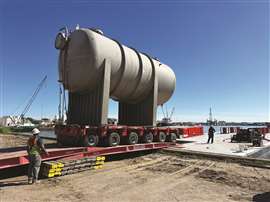
By successfully installing the Flyover Bridge, Berard has made a significant contribution to improving infrastructure and mobility in the region. The project underscores the essential role of innovative heavy transport solutions in modern bridge construction.
Reducer delivery
Edwards, a leader in specialized heavy haulage, demonstrated the creative use of a 6-line PST/SLE Goldhofer trailer, equipped with electronic steering, to successfully deliver reducers to a hydro facility.
The project presented significant challenges, including tight turns along a narrow route and a steep grade that limited conventional transport methods. The use of the 6-line PST/SLE Goldhofer trailer proved to be the right tool in addressing these obstacles. The SPMT offered precise maneuverability, allowing Edwards to navigate sharp corners with ease. Its multi-axle design evenly distributed the weight of the reducer, ensuring stability and safety throughout the journey.
The steep incline near the hydro facility posed another hurdle. However, the robust design of the Goldhofer SPMT, combined with the high traction force, enabled Edwards to manage the grade effectively. The ability to independently control each axle line was a key element, allowing the team to adapt to the changing terrain and the narrow entrance to the delivery site.
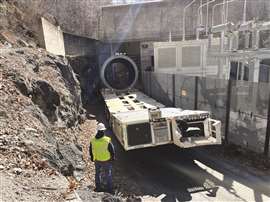
The successful execution of this project highlights the evolving role of SPMTs in heavy haulage no matter how small or large the cargo. From navigating tight urban spaces to scaling rugged terrain, the modular trailers are redefining possibilities in the transport sector. Edwards’ innovative use of the PST/SLE trailer exemplifies how technology and expertise can combine to achieve remarkable results in complex logistics projects, the company said.
Overcoming limitations
Bellemare Heavy Haul & Rigging moves heavy loads by engineering innovative solutions that leverage cutting-edge technology, particularly the strategic deployment of SPMTs. From transporting colossal industrial machinery to executing intricate bridge installations, the company’s SPMTs are versatile and reliable, the company said.
During a critical refinery shutdown, Bellemare’s team faced a significant challenge: transporting a massive heat exchanger that exceeded weight restrictions. Site limitations did not allow for the use of a traditional bundle extractor, which is when the Bellemare team drew upon its ingenuity to devise a novel solution: utilizing two SPMTs to strategically separate the heat exchanger into manageable components.
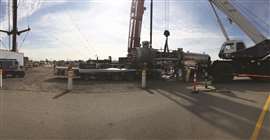
This approach not only facilitated safe and efficient transport, but also ensured the refinery shutdown remained on schedule, minimizing costly downtime.
Decommissioning challenge
Mountain Crane moved two decommissioned steam generators from a nuclear power plant to a secure facility. It was a complex and risky job. For this task, a 12-line Goldhofer THP/SL trailer played a crucial role in safely transporting two steam generators, each weighing 457,000 pounds.
Designed to handle extremely heavy loads, the Goldhofer system’s 12-axle setup spreads the weight evenly, allowing it to carry up to 600 tons. This ensures smooth transport, even with such massive cargo, while protecting both the trailer and the road surface, Mountain Crane said.
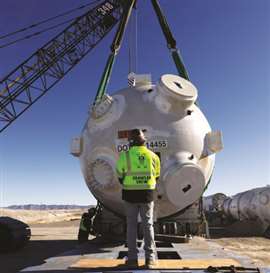
One of the key features of the Goldhofer trailer is its advanced steering system, which provides excellent control in tight spaces. This was especially important at the radioactive facility, where space was limited. The trailer’s ability to maneuver precisely helped the team move the steam generators to their final location, even after they were lifted from railcars using large cranes.
The Goldhofer trailer excelled in tough conditions, handling uneven ground and sharp turns with ease. Its stability and control were essential for ensuring safety throughout the journey. This operation, carried out for Energy Solutions, proved the value of SPMTs in moving heavy items in difficult environments.
Rugged terrain
When a 180,000-pound transformer needed to be transported through the rugged terrain of El Dorado County, CA, Omega Morgan’s specialized transportation team rose to the challenge. Tasked with moving the massive transformer from a utilities laydown yard to the substation at Union Valley Dam, the team faced a 25-mile mountain route with steep grades ranging from eight to 16 percent.
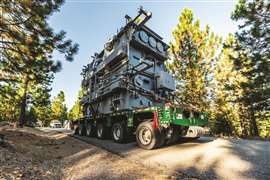
This haul required ingenuity, precision and top-tier equipment. The crew relied on a K25 6-line self-propelled modular transporter and their high-frame girder system to overcome the route’s most challenging obstacle: the Silver Creek Bridge.
At the utilities laydown yard, the team jack-and-slid the transformer onto the SPMT, then transported it to the south end of the Silver Creek Bridge. To “jump” the bridge, they engineered a meticulous process: beams were placed atop the trailer and beneath the transformer, allowing the load to be transferred onto the bridge jump system. With the transformer securely positioned, they slid it across the bridge, disassembled the system, drove the SPMT across and reloaded the transformer on the other side.
Upon reaching the substation, the team skillfully extracted the old transformer, transported it to the laydown yard and maneuvered the new transformer into place with the same jack-and-slide system and SPMT.
STAY CONNECTED
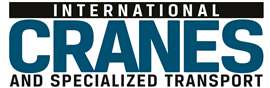
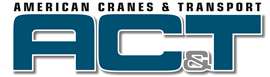
Receive the information you need when you need it through our world-leading magazines, newsletters and daily briefings.
CONNECT WITH THE TEAM
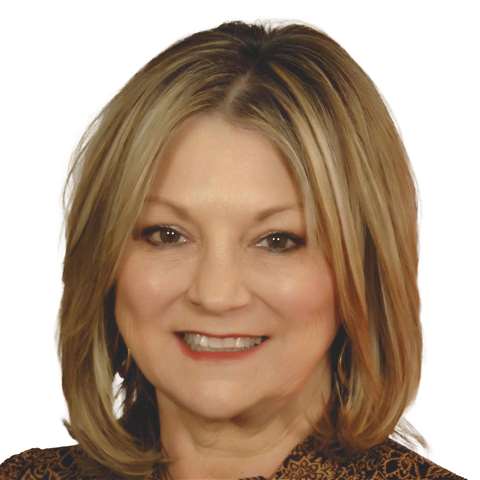
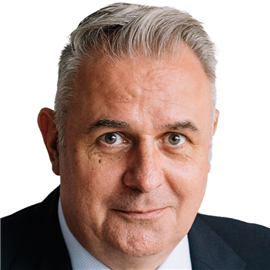
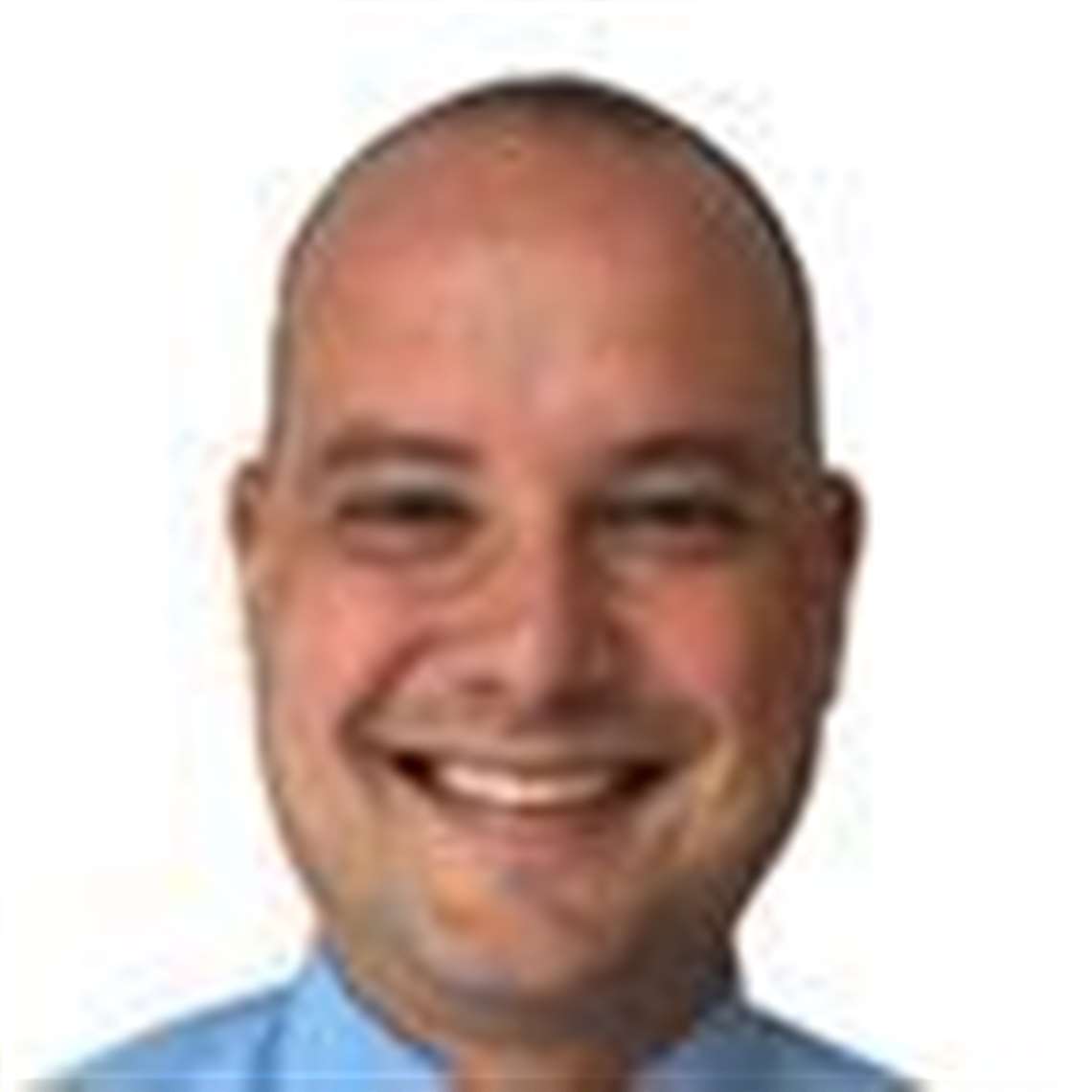
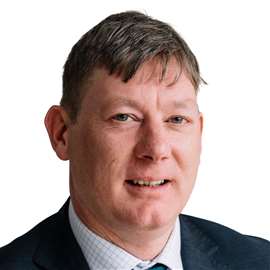