Read this article in French German Italian Portuguese Spanish
How using refurbished cranes saves time and money
05 February 2024
Repairing, refurbishing and remanufacturing crane components not only saves money but can be a sustainable choice too. Niamh Marriott reports
Crane manufacturers worldwide are continuing to look for ways to meet customer sustainability requirements whilst continuing to offer competitive pricing.
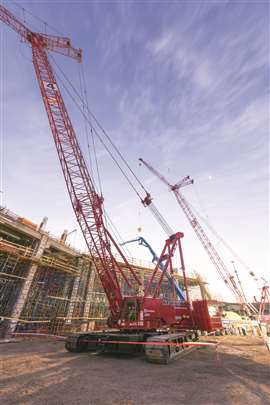
Buying a new machine goes hand in hand with high costs and long waiting times, says Simon Albrecht of Germany-based industrial auction house Surplex. “Many business owners are discovering the benefits of second-hand machines for their own production operations, with the used machine market enjoying a new lease of life. When things are handled properly, high profits can be expected from sales.”
An additional benefit? “It enables buyers to extend the life cycle of machines while lowering CO2, in turn, protecting the environment.”
Dedicated division
Many of the larger manufacturers already offer repair solutions for cranes, either as part of their after-care service or as a separate, dedicated division of their business.
Manitowoc has its EnCore programme. The company says that whether a crane requires repair due to damage caused by an accident, or needs an end of service life rebuild, EnCore gives a viable option over a new crane purchase.
It says the key advantages of remanufacturing include maximising your investment, reducing downtime and security in the knowledge that the crane has been restored to industry-standard and engineering specifications.
Manitowoc also offers a component exchange programme.
USA-based Maxim Crane Works is working with EnCore on a multi-year project to remanufacture 14 of its Manitowoc 2250 crawler cranes. Once refurbished the cranes will be redeployed across its US rental fleet.
The company said the plan is one of the largest projects of this kind to date. The work is initially being carried out at MGX Equipment Services facilities in Belle Chasse and Birmingham, Alabama.
Fraction of the cost
Larry Lis, vice president of fleet at Maxim Crane Works, says, “The Manitowoc 2250 is the only true 300 ton (272 tonne) crawler crane on the market with the ideal cost-benefit tradeoff for rental work.
“We have 50 Manitowoc 2250s working in our fleet. We can have them remanufactured by Manitowoc and have great working cranes for another 12 to 15 years at a fraction of the cost of purchasing newer cranes that may not be ideal for our current demands.”
“Our operators know how to use them. Our mechanics know how to work on them. We already have a strong spare parts inventory for cranes in this class. Our logistics team knows how to transport them. We understand the differences in how to move and operate them in various regions. It’s a definite plus,” he explained. “They will also have a strong resale value if we decide to change up the fleet.
“The remanufacturing certificate from Manitowoc will hold a lot of value.”
The EnCore remanufacturing project will continue through 2026, with three or four 2250s being remanufactured at a time. Lis said the plan could be expanded and more cranes cycled through, should the need arise.
Nearly new
German crane specialist BKL says it not only offers a range of new tower cranes but can also provide “nearly new” and used cranes too. This also includes parts and accessories. Its cranes can be serviced and repaired by BKL’s technicians. New to BKL is its purchase of used cranes. The company says its crane team is looking to buy or trade used construction cranes.
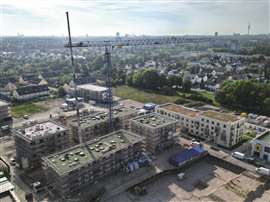
Japanese manufacturer Tadano offers repair work as part of its after sales service at its factory in Lauf, Germany where it has a specialist crane workshop. At the workshop, cranes for repair are examined and inspected so the team can prepare a cost estimate and time expectation for works. The work is then carried out with original spare parts and any new functions or features can be added to modernise the crane, Tadano says.
Partner up
Announced during the Bauma exhibition in October 2022 Crowland Cranes and Avezaat Cranes formed a joint service partner agreement. The two companies have already worked closely together in recent years on crane repair projects.
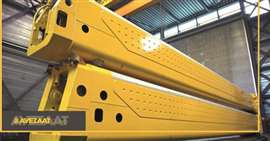
Joining output opens new channels for both of these crane repair specialists, enabling them to share their experience and knowledge of the crane industry.
Peter Issitt, Crowland Cranes managing director, says, “Avezaat Cranes are one of the most respected, structural crane repairers in the industry, with increasing skill and experience required to complete structural repairs today on modern cranes, having Avezaat as our service partner will provide the team at Crowland, our clients and UK insurers, with even greater confidence when completing major crane repairs.”
Taking stock
Since this announcement, Avezaat Cranes says it now offers more new and used boom sections. A spokesperson for the company says, “We’re proud to offer newly manufactured lattice booms, jibs, and telescopic booms for all makes and types of crawler cranes and telescopic cranes.
Aveezat has facilities in both Holland and Dubai so can offer short delivery times on manufactured parts. “Our large stock of high-tension tube and plate materials ensure short delivery times, getting your crane back in action quickly and safely. Whether it’s for a planned new manufacture project or an emergency repair on site worldwide, we can offer timely and high-quality solutions.”
Electric power
Retrofitting parts is nothing new for the crane industry but as early adopters see the benefits of electric power, it is likely that more existing cranes will be fitted with electric motors.
Heavy lift giant Mammoet is doing just that, saying it is leading the way towards zero emissions on site.
Switching to electric power maintains the same levels of performance but makes projects quieter and safer.
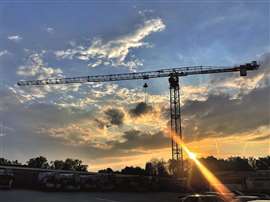
A recent crane refurbishment of a 100 tonne lifting capacity crane offered some series benefits. It had an undercarriage engine and a superstructure engine, which powered the crane. The superstructure engine was replaced with an electric motor.
Ard Prins, crane operator at Mammoet says, “A diesel engine generates all kinds of vibrations, and there’s none of that now. It’s a lot more comfortable to work with.
“The diesel engine takes you to the site, but it’s the electric motor that does all the lifting.
“It’s the world’s first electric 100 tonne crane,” says Mike Ekkel, managing director of the north region at Mammoet. It’s been quite a long project but we want to be a leader in sustainability. We want to contribute to creating a better society. We also want to service our customers who have an increasing need for equipment that generates zero emissions on site. The demand is pretty high but it wasn’t available. We had two options: wait until it would become available or take the first step and develop it ourselves, and that’s what we did.
Prins adds, “When I heard they were going to electrify my crane, I was quite sceptical at first. To what extent will it change? Will it handle differently? But the first time I worked with this crane I was pleasantly surprised. It basically handles the same but the noise is gone.
Ekkel concludes, “It’s a fantastic project because I firmly believe in sustainable innovation. It’s very important for our future.”
STAY CONNECTED
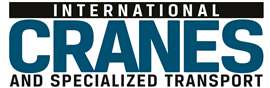
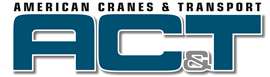
Receive the information you need when you need it through our world-leading magazines, newsletters and daily briefings.
CONNECT WITH THE TEAM
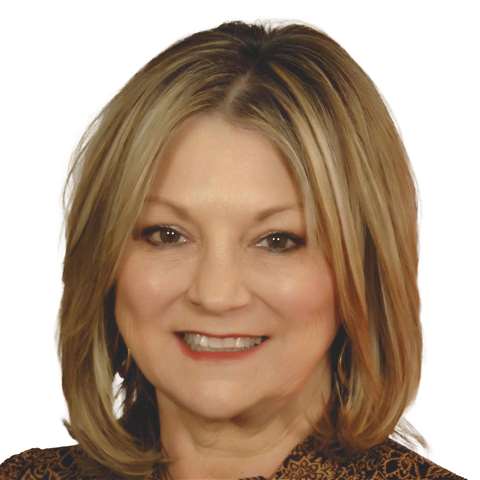
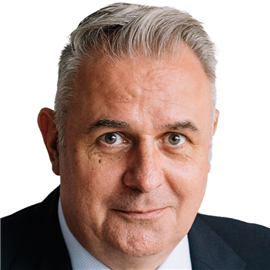
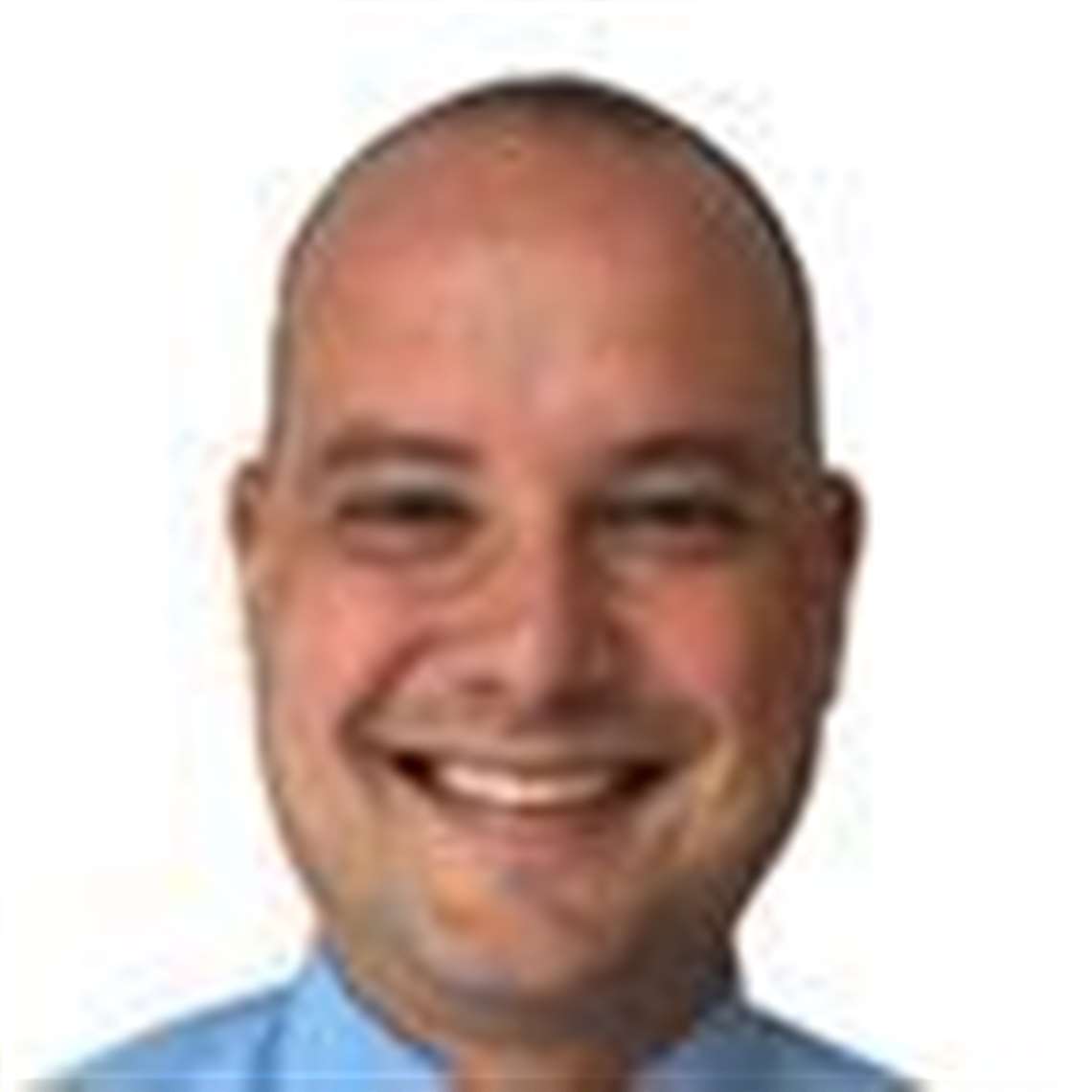
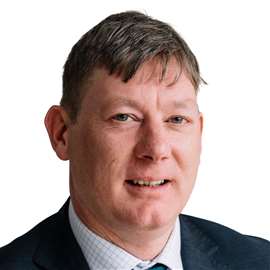