Rigging the impossible: Job roundup
22 July 2025
A roundup of jobs that required highly specialized rigging equipment.
If you really want to see some innovative rigging in action, make it a point to attend the SC&RA Job of the Year presentations at the Association’s Annual Conference each year. Incredible feats of rigging are presented by the best of the best. These jobs present a wide array of problems and solutions, using a combination of every day rigging gear and equipment and customized rigging solutions.
Wash tower erection
The lifting and erection of a caustic and water wash tower at S-Oil’s Shaheen Project in Korea was a highly complex and meticulously planned rigging operation that required the highest standards of safety, innovation and engineering excellence by the expert team from Japanese crane, transport and construction specialist Denzai KK. The lift involved handling a 794 tonne tower, standing nearly 70 meters tall, within the confined space of an active industrial facility. Due to the weight, height and sensitivity of the load, as well as the site constraints, the execution demanded extensive engineering analysis, innovative rigging solutions and a flawless execution strategy.
The top priority for the Denzai team was safety, at every phase of the operation. A comprehensive safety program was implemented, ensuring strict adherence to regulations as well as site-specific protocols. To align on procedures and emergency protocols, pre-lift safety meetings were conducted with all personnel, including crane operators, riggers and safety officers. The ground was reinforced using steel mats and plates to ensure stability, while real-time monitoring of wind speeds (limit: 13.4 metres a second) was conducted to prevent lifting under unsafe conditions. To further enhance safety, high-capacity Crosby shackles, grommet slings and a custom-engineered spreader beam were used to distribute load forces evenly, preventing excessive stress on the lifting points.
Denzai used its 2,500 tonne capacity Liebherr LR 12500-1.0 lattice boom crawler as the main crane and a 750 tonne Liebherr LR 1750 was chosen as the tailing crane.
This project required both innovative problem-solving and precise execution to overcome its inherent challenges. Given the offset center of gravity (CG) and the lack of standard pick points, a customized trunnion and tailing lug system was designed to facilitate the lift while maintaining load stability. The team also leveraged 3D modeling and finite element analysis (FEA) to determine the optimal rigging configuration and validate lifting stresses.
A particularly complex aspect of this lift was the tandem crane operation, where both cranes had to work in perfect coordination. The LR 12500-1.0 executed the primary lift while the LR 1750 controlled the tail, ensuring smooth rotation and controlled movement.
To accommodate tight working conditions, the lift was meticulously planned, accounting for ground pressure calculations, obstructions and limited crane positioning options. This level of complexity required extensive engineering foresight and operational precision, according to Kohki Uemura, Denzai CEO.
“The engineering and planning phase was instrumental to the success of this project,” Uemura said. “The tower’s asymmetrical weight distribution necessitated highly detailed rigging calculations to ensure safe lifting and placement. Load verification techniques, including 3D scanning and weight confirmation, were employed to gather precise data on the tower’s dimensions, weight and CG location.”
The rigging tackle arrangement was equally critical, incorporating high-capacity grommet slings rated for more than 3,600 tonnes combined to provide adequate load distribution. The lift itself was executed within a highly congested refinery site, requiring exceptional precision in crane mobilization and load movement. Despite constraints, the team successfully hoisted and rotated the tower while the tailing crane provided the necessary counterbalance.
This project was a time-sensitive and high-stakes operation. Delays or safety incidents could have resulted in significant financial penalties and project setbacks. By leveraging advanced engineering analysis, unnecessary over-engineering was avoided, leading to substantial cost savings on rigging and crane rental expenses.
Additionally, the ground preparation strategy minimized the need for excessive civil works, optimizing costs while maintaining safety. This lift set a new benchmark for heavy lifting in confined industrial environments. The project’s innovative approach to rigging design, tandem crane operation and engineering analysis has contributed valuable lessons for future large-scale lifting operations.
The successful execution of the water wash tower lift exemplifies excellence in safety, innovation, engineering complexity and execution precision, according to Uemura. This project stands as a testament to what is possible in heavy rigging.
Shaker screen switch out
ProLift Rigging in the USA was challenged with the removal of a 30,000 pound (13.6 tonne) shaker screen and replacing it with a new unit. The customer determined the time frame from start to finish was seven days. This was based on methods previously used to execute the scope of work.
After several site visits and discussions about methods used in the past, the ProLift team assessed various solutions. One plan involved removing the roof and a significant number of crossmembers so the shaker screen could be picked straight up by a crane and then replaced with a new one. Another method involved bull rigging with chain falls, snatch blocks and come-a-longs. In the end, ProLift proposed an alternative solution.
“ProLift didn’t want to accept a method that would result in lengthy downtime for the customer that would result in greater loss of revenue or an increased exposure to risk,” said Travis Black. “Reducing the risk factor was, first and foremost, the top priority, especially with this scope having to be executed at heights.”
ProLift’s engineering department did a lot of brainstorming. The focus was on alternative methods geared towards safety, efficiencies, ingenuity and available internal equipment within the ProLift branch network, Black said.
“The collaboration resulted in a method that would be different than any other proposal the customer had received in the past, so proper communication of the method had to be choreographed in a manner that the customer had confidence in ProLift,” Black said. “The solution comprised our two multi-point spreader bars fastened together by two frame adapters to form a multi-point lifting frame. Then combining the multi-point lifting frame to our Bear Paw cantilever system, which resulted in a multi-point cantilever lifting frame. With no precedent for the customer to reflect on, they were hesitant to entertain the alternative solution as a viable option, especially since the solution marked the first time this scope had been proposed to be executed this way at this facility.”
The lift required safe and meticulously engineered plans that factored in tight clearances, heavy lifts, coordinated crane movements and an experienced field crew. Safety was a constant concern, especially due to the challenges posed by limited overhead clearance, an obstructing mezzanine and the need for precise hook movement.
The mezzanine extended almost four feet beyond the level above the screen at a height of 27 feet (8.2 metres) off the ground, making vertical lift path control critical. In addition, the pick points on the front were 13 feet 4 inches (4 metres) apart, with the rear points extending 8 feet 3 inches (2.5 metres) under the level above, requiring careful rigging selection to maintain load stability. Due to the cantilever being off the crane’s whip line, the lift would involve a combination of booming, swinging and winching adjustments to maintain a controlled load path. Given the complexity, the dynamic of this lift required a highly skilled crane operator and signal person, Black said.
After several meetings and follow-up clarification requests, the customer agreed to the proposed method and the scope of work was awarded to ProLift.
The ProLift team developed a timeline and started mobilizing the necessary lifting gear, skilled employees and equipment. The goal was to mobilize the equipment and assemble the cantilever system on Day 1. Then, on Day 2, remove the old shaker screen. Day 3 would be used to install the new unit and on the last day, disassemble and de-mobilize from the site.
Each day began with a safety meeting where the crews come together and complete ProLift’s worksite risk assessment (WRA). The WRA ensures identified risks are reduced to an acceptable level and appointing the correct individuals to ensure the mitigations are being followed. During the meeting, the SOPs pertaining to the scope were discussed, engineered drawings reviewed and open communication of site-specific customer requirements. Also, a pre-lift safety briefing was conducted to align the entire team on the lift sequence, communication protocol and load handling expectations.
The ProLift team executed the plan seamlessly. In fact, the scope of work was completed a day earlier than projected.
“The customer rated ProLift at 10 out of 10 on our customer post job review,” said Black.
Reactor rigmarole
Allegiance Crane & Equipment in the USA was tasked with the removal of two 236,000-pound (107 tonne) reactors in an active operating unit. Due to excessive lead times for fabrication and delivery, new reactors were not an option, necessitating the careful removal, repair and reinstallation of the existing units.
The project presented unique challenges. The reactors were encased in a support frame with more than three dozen obstructions, including lines, nozzles, valves, gauges, flanges and steel structures. The reactors needed to be lifted, rotated and supported high enough to allow personnel to access the welds needing repair.
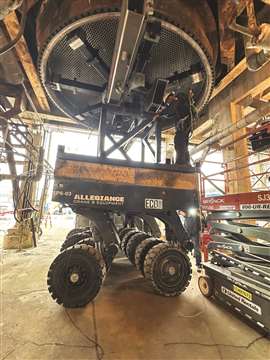
Initially, Allegiance’s plan involved using a Demag AC 700 wheeled mobile telescopic crane to lift and rotate the reactors out of the unit for repairs. Traditional crane-based removal was unfeasible due to space constraints and the potential to disrupt other critical work. The solution required a minimized footprint while maintaining lifting capacity, precision and safety.
The Allegiance engineering and project team designed and implemented an innovative lifting method using a Cometto Eco 1000 six-line self-propelled transporter module, a 300-US ton (272 tonne) Hydra-Slide turntable, a custom-engineered interface structure designed to fit the turntable and support the base of the 236,000 pound (107 tonne) reactor and custom-engineered stands (stackable) designed to bolt into support structure and allow reactor to rest on its existing support pedestal. There were three parts to executing the plan.
First, the reactor was lifted in one-foot increments within its support structure to prevent overextending the trailer. The Hydra-Slide turntable was used to rotate the reactor, allowing it to navigate numerous obstructions safely. Once sufficient clearance was achieved, a one-foot engineered support stand was inserted into the existing structure and bolted in place. The reactor was then lowered onto the stand, providing stable access. This process was repeated in increments until the reactor reached the required three-foot elevation so welds could be accessed. Finally, after repairs, the reactor was lowered to its original position using the same staged method, carefully navigating obstructions. The team then moved to the second reactor and successfully repeated the process.
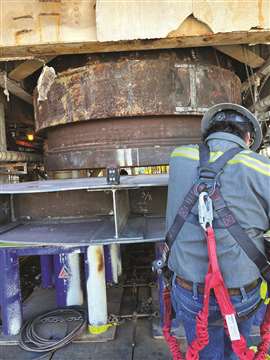
Through this plan, the Alliance team eliminated the need for large crane, which in turn eliminated overhead lifting and suspended loads, reducing congestion and allowing other work to proceed without delays. The Allegiance team maintained project timelines, ensured efficient reactor repairs, engineered a safe and repeatable method and minimized risk and disruption, successfully navigating complex obstructions while maintaining precision control over the reactors.
“This project demonstrated the effectiveness of custom-engineered lifting solutions in constrained environments,” said Allegiance Crane & Rigging’s B.J. Buchanan. “The success of this method has established a new best practice for future reactor repairs, providing clients with a cost-effective, efficient and low-impact solution for similar challenges.”
STAY CONNECTED
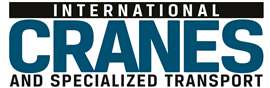
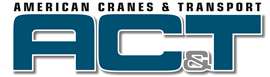
Receive the information you need when you need it through our world-leading magazines, newsletters and daily briefings.
CONNECT WITH THE TEAM
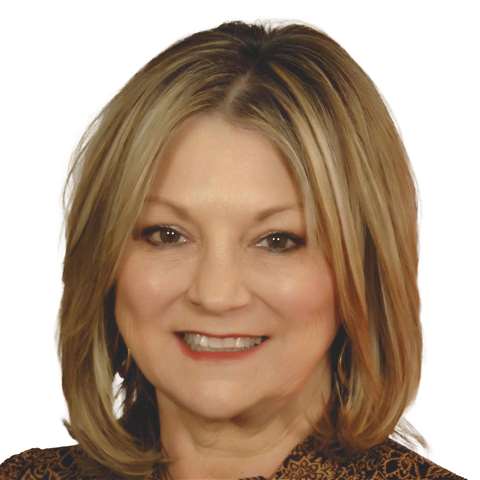
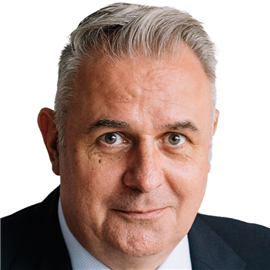
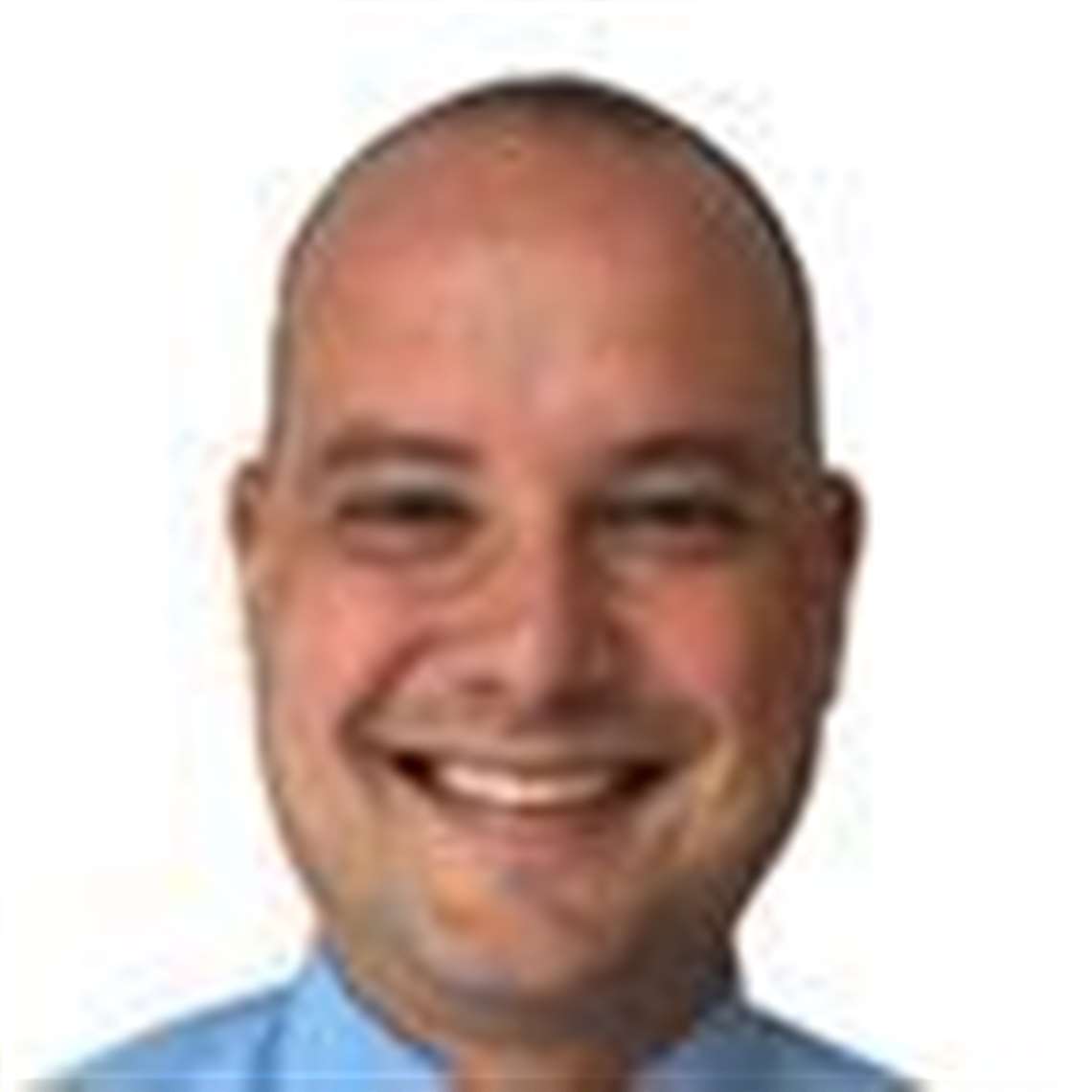
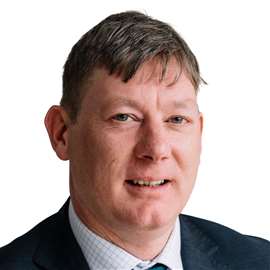