Read this article in French German Italian Portuguese Spanish
How is the lifting and transport industry working towards a sustainable future?
25 February 2024
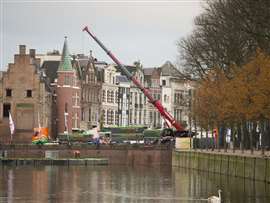
International heavy lift and transport specialist Mammoet is innovating with zero-emission lifting and transport on site to help its customers reduce the carbon footprint of their projects.
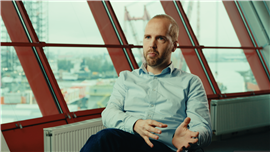
Who better to have the first word on this than Mammoet head of sustainability Mathias Hoogstra, “If you ask me what my main vision is, I want us to redefine the construction site – at least at small scale initially – where we have electric or hydrogen cars, electric cranes, electric trucks, and have all this equipment cross-link and charge each other.
“An energy hub or energy balancing system would know where to direct power efficiently during a project. Equipment with the lowest energy would be fed by the equipment with the highest, or when required powered by additional external sources like hydrogen or bio-fuel generators.
So, by design, we focus on exchanging energy as efficiently as possible and becoming zero-emission on site.”
Mammoet sees sustainability as an important factor in the future of the heavy lifting and transport industry. A major challenge is presented by the sheer scale of the huge and heavy loads involved. Electrifying fleets of cranes and self-propelled trailers has for years felt like a pipe dream, Mammoet says.
Recent developments, however, mean an entire project can now be done without engine exhaust emissions. This is achieved using equipment already introduced to the market. Sustainability in heavy industry offers big rewards for sufficiently adaptable companies.
Mathias Hoogstra explains, “You see now, in government legislation but also in the tendering process, solutions that are adhering to zero emissions score more points. In the past this was the case but the delta is becoming more and more significant in the value chain.
“I wouldn’t say the whole flood wave is already there, but the first change is starting. If you want to be a leader in the market, in my opinion, you must ensure that you are leading this whole transition and are at the forefront for your customers.”
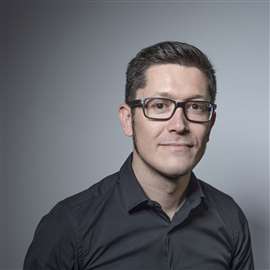
Annual growth
Rafael Martinez, Mammoet sales manager for the civil sector, reports growth in demand for sustainable heavy lifting and transport over several years. “Low or zero-emission conditions are becoming more common these days. There are sometimes very specific needs to drive down the carbon impact of projects, originated by local particularities or restrictions by public entities, like projects within congested urban environments, or environmentally protected areas. In Europe, this is something we are already seeing for tunnels”.
There is no turning back and this is something all companies must implement to succeed. “It can go faster in some sectors and countries, slower in others. Ultimately, we are all on this trajectory and all businesses must adapt and prepare,” Martinez says.
“From a public opinion perspective, no-one will be able to sell the need for more diesel-powered machines on-site. It is starting to become more important, and in certain cases it becomes key. In fact, projects that generate significant carbon emissions find it more and more difficult to secure funding from large financial institutions,” Martinez explains.
Heading for net zero
Investment has been made at Mammoet to be less reliant on diesel and to offer customers a choice of alternatives. Existing equipment, including the electric self propelled modular transporter (SPMT) and the SK series of super heavy lift cranes, allows the company to serve the entire site lifting and transport scope of a project.
Just a few years ago this would have seemed impossible purely due to the long working hours required.
Hoogstra continues, “I would say we are proving ourselves now. We were developing for specific markets; and from this we are now seeing that we can combine different solutions to make a whole project more sustainable, whatever the demand. For example, we can now execute the marshalling and pre-assembly scopes of an offshore wind farm emissions-free.
“Our focus in the civil sector is to make sure that the movements of large items, such as viaducts and bridges, can be carried out with zero emissions using hydraulics that are powered by electricity. We installed a tunnel section recently in Belgium, of 850 tonnes, and did it fully electric. So, we can do it and can scale up fast to make sure we can do more.”
Electric SPMT
SPMT is used on many heavy lifting projects so it makes sense to electrify it for net zero heavy transport. Mammoet used an outside supplier and the first electric Power Pack Unit (ePPU) prototype was tested at Mammoet in Schiedam, Netherlands.
In terms of capability there is no significant difference between electric and diesel-powered SPMT and both offer a capacity of 40 tonnes per axle line. Dimensions and mounting position of the ePPU are the same as the diesel one.
Battery charging from 0 to 100 per cent takes around five and a half hours, meaning it can be done overnight ready for the next day.
Swapping out the PPU diesel engine and fuel tanks for an electric motor and battery helps sustainability by future-proofing existing equipment and it extends its service life.
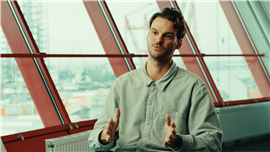
Niek Bezuijen, Mammoet global sustainability advisor, explains, “We nominated an old power pack to upgrade, which didn’t work as efficiently anymore. From a sustainability perspective, we thought: why don’t we retrofit it and make it electric because this results in a tailpipe zero-emission solution, and less waste?
“By reusing this equipment, we avoid the carbon impact of discarding it, the production cycle needed to create an all-new electric replacement and, of course, the diesel emissions that the former equipment would have emitted when used,” Bezuijen says.
More ideas
Lowering the carbon impact of projects means looking into other zero-emission options. “A hydrogen power feasibility test was carried out by skidding a single electrical transformer. The hydraulic system uses a hydrogen generator to perform the skidding operation. This solution emits only water vapour. For practical reasons it is more favourable to do the operation electrically, via the grid, or with a battery,” said Bezuijen. “In remote areas, it is often still possible to bring a battery pack, because jacking and skidding at the lower tonnages doesn’t require much energy – this is what we discovered with the test using hydrogen, in fact.
“We performed the same test with the battery, and to put an electrical transformer in place we only used seven kilowatt-hours (kWh). To put that into perspective, a Tesla has around 60 or 70 kWh of battery, so we only used 10 per cent of that”.
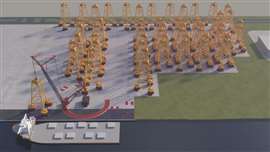
Electric lifting
Mammoet has been using electrically-powered cranes for some time. It has engineered zero-emission offshore wind and onshore wind cranes, and the SK series of cranes has been on the fleet for more than ten years. The SK range is notable among ring cranes in that its hydraulics run from an electric motor, powered by a generator.
SKs are great for construction projects needing a ring crane on site for a long time but what about projects where the crane is not required for a long time?
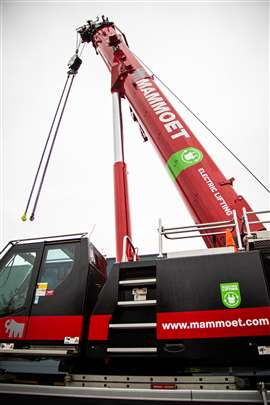
Enter a specially modified 100 tonne capacity wheeled mobile telescopic crane. “This [Liebherr] LTM 1095 crane was four years old,” says Bezuijen. “We decided to do a retrofit and use it as an opportunity to learn more about the electrification of our equipment. We also wanted to push the market for these types of cranes towards zero emission.”
The upper carrier with the crane works and operator cabin is fully electric. “It has a 105 kWh battery inside, so we can run basically a normal working day with it. We conducted some tests a couple of months ago and the crane is now ready to operate.
“The crane’s pre-existing engine was actually still in good condition, so we were able to use it to breathe new life into another crane in the fleet whose drivetrain was approaching end-of-life, and again reduce waste.”
Offsetting cost
Budget is one of the biggest challenges to the adoption of green energy technology. Mammoet plans to support heavy industry to find energy savings to offset the potential costs of going green.
Hoogstra says changing over to electric, hydrogen and biofuel to power equipment and a change in mindset are needed, “In previous years, we were looking to reduce usage of diesel on site. Now, we are taking a step further to monitor energy usage in an electric power environment and actively steer on efficient execution.
“We are conducting tests with our range of electric equipment to determine typical power usage per shift. This will help our customers to put appropriate and cost-effective electricity infrastructure in place, best suited to the project at hand.”
Putting the plans into action is the next step. “We are looking forward to speeding up the whole process based on the needs of our customers. As such, we are looking for participants among our customer base that want to work with us and take these steps together,” Hoogstra concludes.
STAY CONNECTED
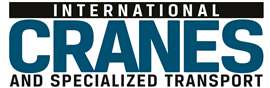
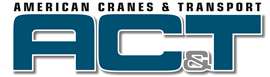
Receive the information you need when you need it through our world-leading magazines, newsletters and daily briefings.
CONNECT WITH THE TEAM
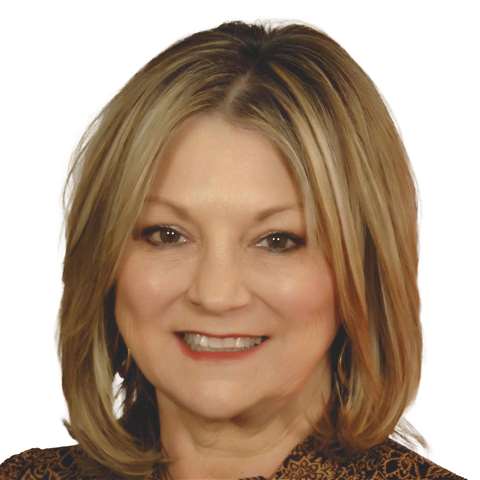
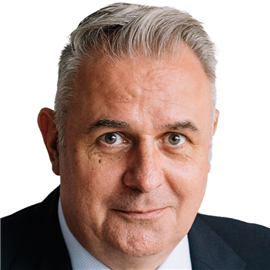
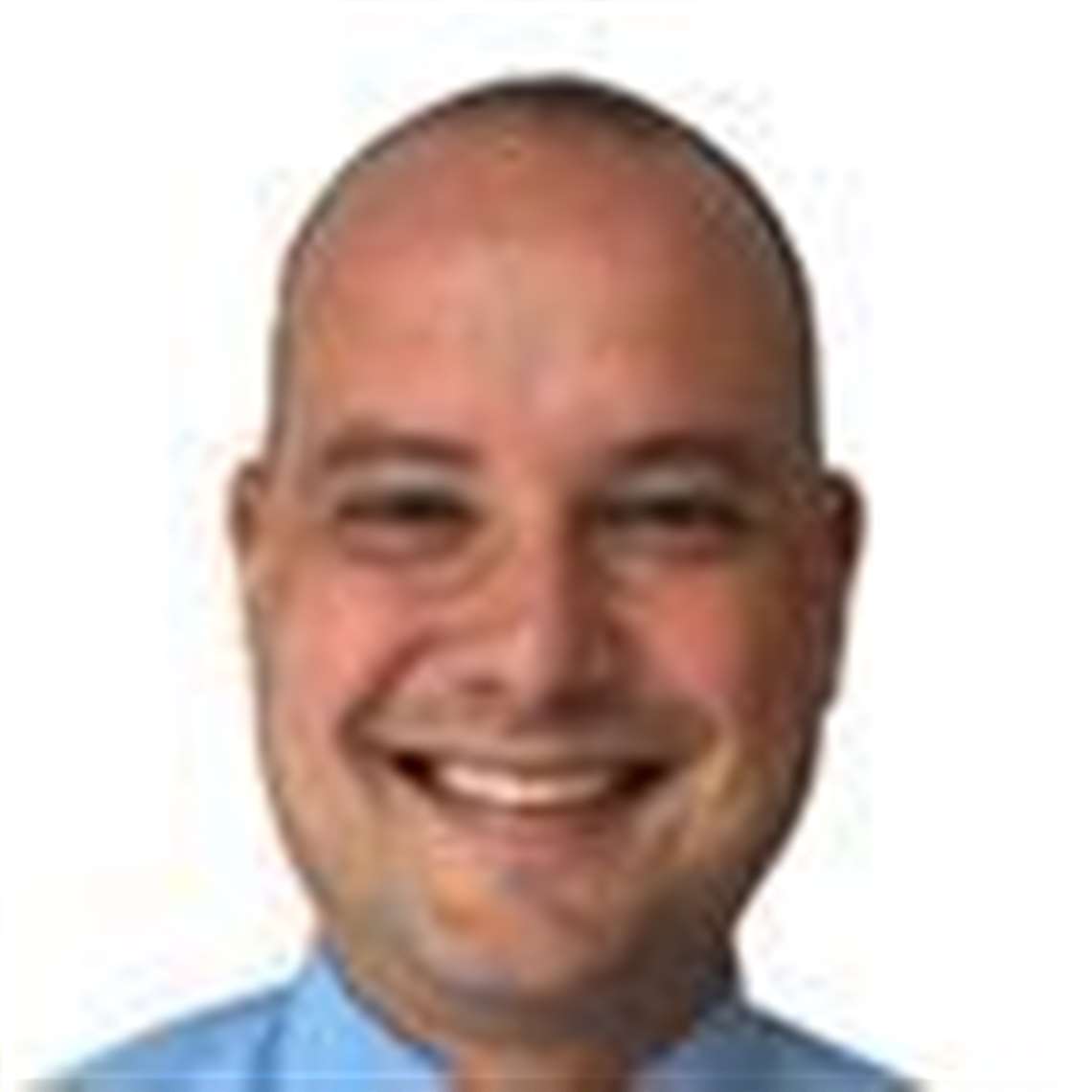
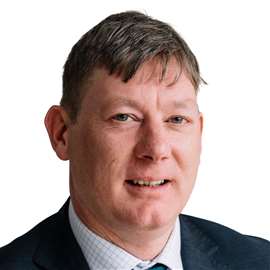