Read this article in French German Italian Portuguese Spanish
Mega crane demand is on the rise
09 January 2024
Around the world, super huge lifts are being performed that could only be accomplished by a super heavy lift crane. Such is the case at the Hinkley Point C Nuclear Power Station in the United Kingdom, at a semi-conductor plant in Phoenix, AZ and at a refinery in India, to name a few.

Cranes on these jobs include the Sarens SGC-250, the Manitowoc 31000 and the Mammoet PTC210-DS, respectively. Deep South Crane & Rigging deploys its 3,000-ton capacity VersaCrane to oil and gas refinery projects as does Lampson International with its Transi-Lift mega cranes.
“Demand is increasing for mega cranes in the United States,” said Lampson International’s Kate Lampson. “We are starting to see an uptick in requests for our Lampson Transi-Lift in a number of industries and for various applications.”
A growing need
The demand for super heavy lift cranes can be influenced by various factors, contends Carl Sarens, director of technical solutions, projects and engineering, for Sarens.
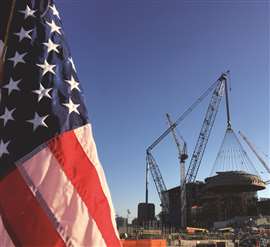
“Whether there is a growing need depends on the trends and developments in key industries,” he said. “There are several indications that currently contribute to a growing need for super heavy lift cranes such as the expansion of renewable energy and a push for net-zero emissions globally, a surviving-and-still-thriving oil and gas and petrochemical market. It’s important to note that these trends and needs may evolve over time based on economic conditions, technological advancements and shifts in global priorities.”
Lampson said that supply chain issues and restrictions on certain industries continue to challenge this market.
“Although the supply chain appears to be recovering post COVID, it is slow to recover and there are still regular delays and challenges,” she said. “With the policies of the current Administration, we do anticipate that work in the oil and gas industry may continue to have challenges.”
Sarens pointed to the “literal massiveness” of these cranes and their mobilization as a challenge of doing business in this market.
“Their assembly is a project in itself,” Sarens said. “For a heavy lift crane to be engaged for a project, a first requirment is for the job at hand to justify the mobilization of such a crane.
The French connection
Sarens is currently undertaking a project of iconic significance for the modernization of the national rail network in France. As part of the project, first the two century-old rail bridges weighing 468 metric tons each – the Pont de Chartres for RER line B and Pont de Gallardon for RER line C – will be dismantled. Next, two new bridge sections will be installed. The two new bridges will allow the passage of faster and more efficient trains in two Paris lines that are used by a total of over 1.5 million people daily in the metropolitan area of Paris. The comfort of local residents will also be improved, with a reduction in traffic noise and vibrations.
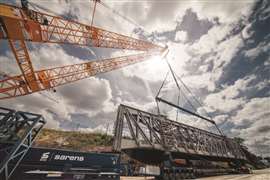
The available area in between the busy road and the railway track was a challenge, along with the low ground bearing pressure. The Sarens SGC-90, a fully electric and silent ring crane, was shortlisted to tackle these challenges and execute the project.
The SGC-90, also known as “Little Celeste,” reached the Port of Rouen from Indonesia and was then transported via trucks to Massy in France. An AC100, LR1200, and CC2800 completed the assembly of the SGC-90 with 100-meter main boom configuration in eight weeks.
According to Sarens Senior Project Manager Dirk Vinck, “It was very challenging to assemble the crane in the limited area available. The ground was prepared with mats to adjust the ground bearing pressure. To maintain safety during the project, heavy tackle, weighing a total of 260 tons, was used to connect old and new bridges to the crane hook.”
Sarens worked on the first phase of the project, involving the dismantling of the two old bridges, this past July 2023. The SGC-90 lifted the two bridge sections and set them down on SPMTs. The SPMTs then drove the old bridge sections to the area where they were finally taken away for scrapping. In the second phase, beginning August, the two new bridge
sections will be lifted into position. The bridges weigh 1,375 metric tons (Chartres) and 949 metric tons (Gallardon) and are preassembled on the other side of the road. These sections will be transported closer to the SGC-90 by SPMTs.
The sky’s the limit
Sarens said the demand for super heavy lift cranes is growing undoubtedly, but certain commercial conditions must be met which often involve the length of the crane’s operation on a project for its mobilization to make sense.
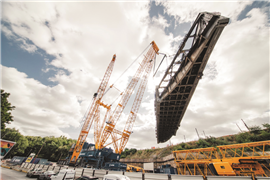
“At Sarens, most of our Giant Cranes are containerizable, which minimizes the impact mobilization has on the lifecycle of a project,” Sarens said. “Furthermore, it also reduces the carbon footprint of the project.”
Another challenge is the lead time required to secure a project and to get the crane ready to work.
Lampson said schedules for mega cranes tend to vary based on the industry the crane is operating in and the application for which it is being used. Big jobs of late have been stadiums, the nuclear sector, the offshore wind sector, the offshore oil and gas sector, the civil sector and other infrastructure projects. The sky is the limit for these cranes and their huge lifts.
Big and getting bigger
Today, about 20 to 25 mega cranes are available to work around the world. But do the owners and makers of these cranes anticipate a future need for larger capacity mega cranes?
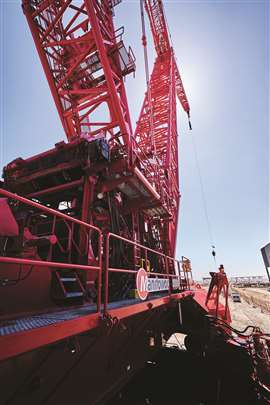
“The short answer is that we certainly do,” said Sarens. “Human ingenuity in engineering, especially when it comes from seasoned experts, knows no boundaries. Electrification of our ring crane fleet is underway with several already being capable of running on electricity. The relentless development of technologies around super heavy lift cranes is a response to a demand that we don’t see going down anytime soon.”
Over the next five years, Lampson and Sarens anticipate the workload for super cranes will increase.
“The most likely scenario is that the demand for these cranes will grow,” said Sarens. “We recently saw the United States enter the offshore game with the first offshore wind park to be created on the East Coast. Europe has been a pioneer in offshore wind, and we believe that this trend will grow in other continents as well. Sarens sees an imminent increased demand for super heavy lift cranes for this sector in the next five years.”
Lampson is seeing a demand for their Transi-Lift in the 1,500 to 2,600-ton capacity range for the construction of power plants, replacement of components at refineries, new stadium construction, infrastructure projects, wind tower erection, bridge work, lock replacements at dams and off-shore oil platforms.
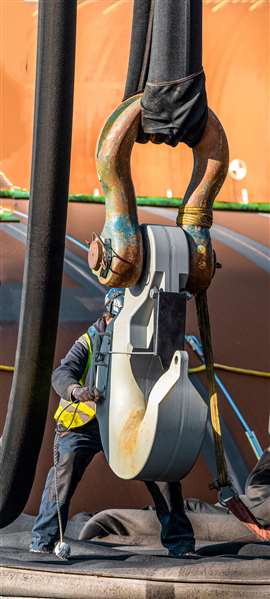
Pipe down
Around 30 kilometers northeast of Rügen, a German island in the Baltic Sea, is where Dutch company Van Oord is building the foundations for the Baltic Eagle offshore wind farm. Van Oord will construct 50 wind turbines with a capacity of 476 megawatts that will supply electricity for 475,000 households. The wind farm is set to go online by the end of 2024, according to the operator Iberdrola, a Spanish energy provider. But there’s still a lot of work to be performed at sea and on land before the project starts producing energy.
Two Liebherr crawler cranes are operating at full power performing port handling on the Baltic coast. This deployment marked the premier of Liebherr’s new LR 12500-1.0.
At the coastal city of Rostock, the lattice booms of the two machines rise steeply into the sky. But the orientation becomes more difficult when in the actual port area, with the view obscured by steel pipes as tall as houses, stacked close together. The pipes will be driven into the seabed at sea and will later support the offshore turbines. The monopiles float on their way to the construction site in the sea. They are towed by a tugboat about 85 nautical miles to the “Baltic Eagle” construction site. The Liebherr cranes are set up at the port basin to place the pipes in the water.

This job is being executed by the Belgian heavy lifting giant Sarens, which specializes in crane rental, heavy lifting and engineered transport. Sarens had the first LR 12500-1.0 delivered directly to Rostock from the factory in Ehingen. “With the support of Liebherr’s fitters, we finished assembling our new crawler crane here after three weeks,” said Willem Dittmer, project manager for Sarens, who is spearheading the operation.

Small but growing market
Liebherr manufactures many classes of cranes, including for the mega crane market. Currently the company produces two cranes in the more than 2,000-ton capacity range, the LR 12500-1.0 and the LR 13000.
Crawler Crane Product Manager Jens Könneker contends the market for cranes with capacities in excess of 2,000 tons is small, but growing, and it will continue to do so.
Liebherr is focusing on the megatrend of expanding renewable energies, which generates work for mega cranes. An example is port handling of components for offshore wind turbines. Liebherr expects significant growth rates for the offshore wind power sector, particularly in 2025. “There is a demand for cranes that are larger than our largest crawler crane, the LR 13000,” said Könneker.
Liebherr’s largest cranes predominantly work in Europe and North America. Most any project for a 2,000-plus ton crane is going to be planned far in advance compared to traditional crane work,” said Jim Jatho, product manager for lattice boom crawlers for Liebherr USA.
Mammoet to debut world’s largest electric mega crane
The first components have been fabricated for Mammoet’s SK6000 ring crane. It will be the worlds largest crane, Mammoet reports, and the highest-capacity electric crane on the planet – behind Mammoet’s own 5,000-metric ton capacity SK350. The SK6000 offers a hook height, outreach and lifting capacity far in excess of any crane on the market, the company said.
The SK6000 can be operated entirely from electric power, helping customers reduce the carbon impact of their projects. By utilizing Mammoet’s electric SPMT power pack system, a fully electric land-based marshalling and load-out scope is now possible.

The first parts for the SK6000 have been produced at Mammoet’s fabricator in the Netherlands. Building on the established design of the SK350 series, it will support the sector as offshore wind components grow in size and travel larger distances. The SK6000 is capable of lifting 3,000-metric ton components at 220 meters hook height, and has a maximum radius of 144 meters. It will be able to take on lifts in the 3,000 to 6000 metric ton range, including suction bucket jackets, XXL monopiles and floating wind foundations.
STAY CONNECTED
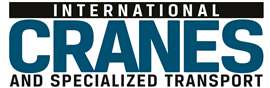
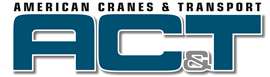
Receive the information you need when you need it through our world-leading magazines, newsletters and daily briefings.
CONNECT WITH THE TEAM
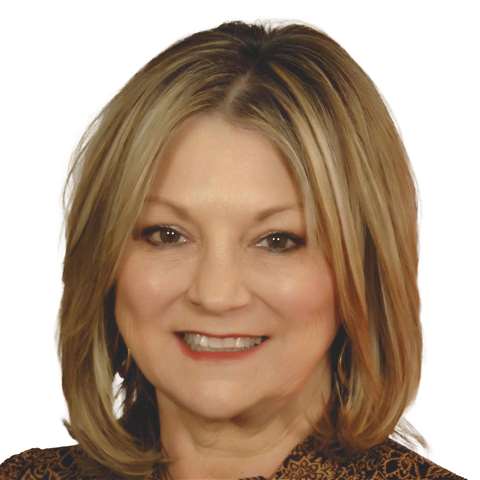
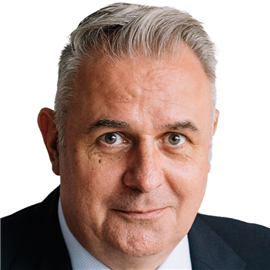
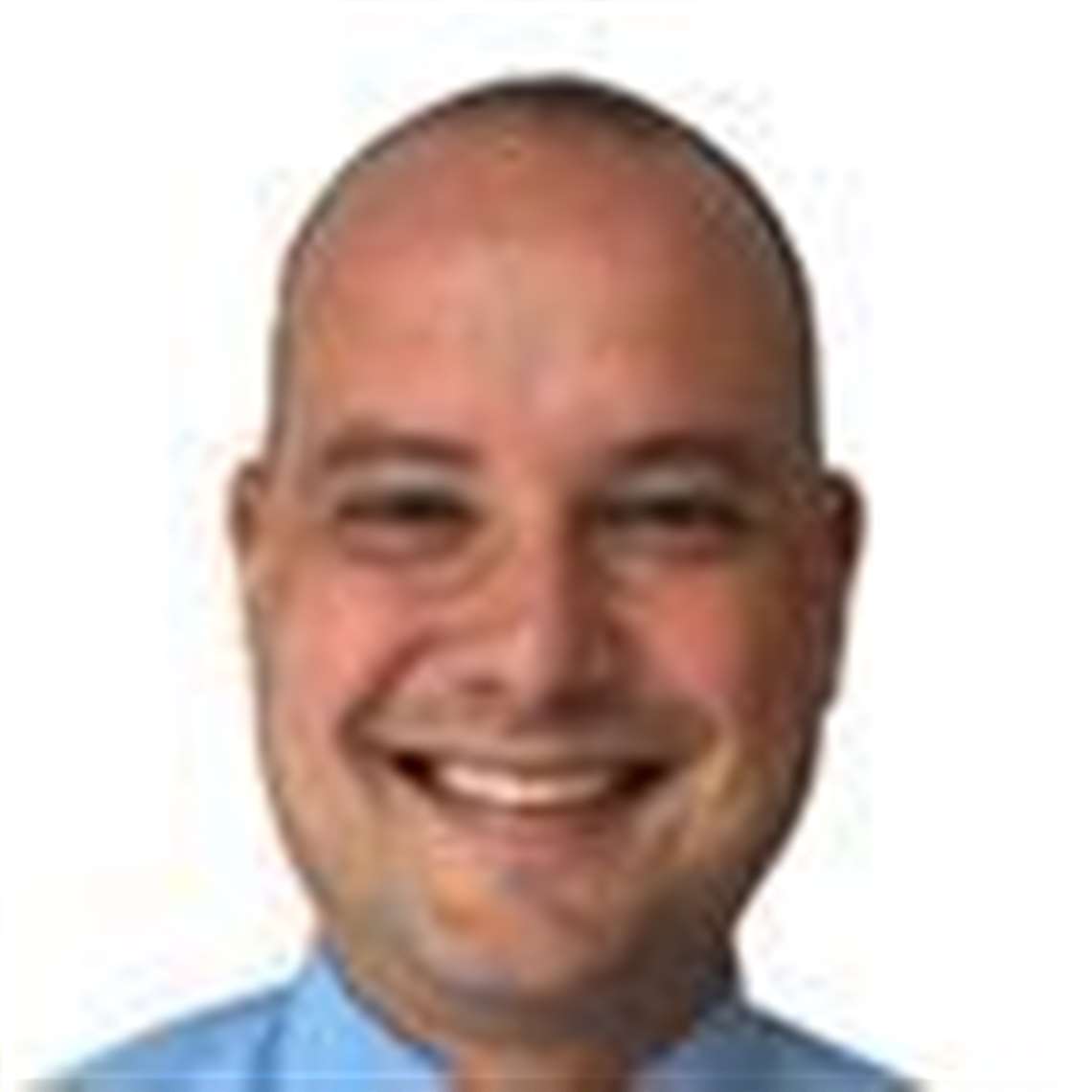
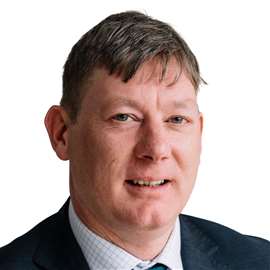