Read this article in French German Italian Portuguese Spanish
Rounding up the latest specialized lifting projects
07 March 2024
Loosley speaking, specialized lifting involves using equipment that is not run of the mill to pick up and place something that is ultra heavy. Specialized lifting and rigging often requires engineered lift plans and solutions that are creative, safe, efficient and, many times, cost effective.
Each year, ACT showcases various specialized lifting and rigging jobs that require the utmost in experience and practical know how. Here’s our 2024 roundup.
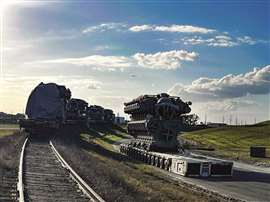
Edwards Moving & Rigging
In a testament to precision and engineering prowess, Edwards Moving & Rigging embarked on a large project that pushed the boundaries of its logistical expertise and underscored the team’s commitment to delivering excellence, according to the company.
The undertaking involved the seamless transition of six Reciprocating Internal Combustion Engines (RICE), each weighing a staggering 716,502 pounds, from rail to a powerhouse destined to redefine energy capabilities, and also receiving six alternators via over-the-road trucks, for a southern utility company.
Edwards’ crews lifted each engine block from the railcar and shifted it onto their 16-line Goldhofer PST configuration, utilizing a gantry with side shifts, designed and built by Enerpac. Once on the Goldhofer system, Edwards chained the engines to the specifications required and began the trip to the staging area, where various components were installed on the engines.
The transport to the staging site required mitigation at several points along the route, all successfully managed with Edwards’ inventory of various sized bridge jumpers, the company said.
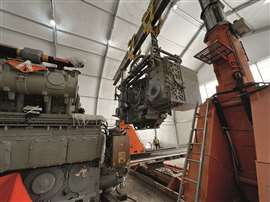
While one crew moved the engines to the staging area, a second crew received the alternators that were trucked from the port and placed them by crane onto staging material, enabling the Edwards team to self-load the alternators onto its Goldhofer PST. The Edwards crew then moved the alternators to the powerhouse and slid them into final position prior to moving the engines into the building.
In the staging area, the Edwards team moved each engine into a large assembly tent where the engine’s base, flywheel and turbo charger were installed free from any weather. The crew utilized a gantry set up inside the tent to lift each fully assembled engine onto its 16-line Goldhofer PST.
The fully assembled engines were transported to steel pads that were built by Edwards’ crew and were located adjacent to the powerhouse. The Edwards team used climbing jacks and its Hydra-Slide Synchronous Power Pack to lower the engines into position for sliding. The crew then slid the engines through the powerhouse on Edwards’ slide tracks to their final locations.
“Utilizing two crews and thorough planning, Edwards was able to maximize efficiency and complete the project ahead of schedule and on budget,” the company said. “The project represents Edwards Moving & Rigging’s unwavering commitment to pushing boundaries, embracing challenges and delivering solutions that redefine what’s possible in the world of heavy equipment transportation and assembly,” explained Tobias Epple, director of regional sales for Edwards Moving & Rigging. “Whether it’s a short or long haul, specialized jacking or rigging, barge or rail transport, a complicated crane lift or a complete turnkey operation, Edwards’ sales, safety and engineering staff are ready to solve your transportation and rigging needs.”
Founded in 1961, Edwards Moving and Rigging is based in Shelbyville, KY.
PSC Crane & Rigging
PSC Crane & Rigging recently performed the installation of a fully-automated stamping press line at an automotive component supplier’s facility. The project consisted of approximately 40 truckloads of components and 135 crates of machine parts. Executed as a turnkey solution, PSC performed not only the heavy rigging and assembly activities, but also the electrical wiring and process piping installations.
Among the heaviest lifts, the PSC Crane & Rigging team installed the crown section of a 3,000-ton stamping press weighing more than 550,000 pounds. The PSC team used a 500-ton capacity J&R Lift-N-Lock gantry system that allowed for full capacity lifting at a maximum of 34 feet in lift height.
The gantry configuration was accompanied by 125-ton J&R Power Links that provide for lateral travel along the header beams for precision placement of the crown section on machined keyways.
“PSC Crane & Rigging partners with J&R Engineering, relying on them to provide state-of-the-art lifting technologies to meet our customer’s challenging projects,” said PSC’s Randy Sever.
PSC Crane & Rigging owns four J&R Engineering gantries with capacities of 350 tons, 500 tons, 700 tons and 900 tons. Each features the J&R Power Links system. PSC also has a 400-ton Power Rotator and 600 lineal feet of J&R Propel Gantry Track.
PSC Crane & Rigging, based in Piqua, OH, provides heavy lift and installation services across the country for various projects in automotive, industrial, manufacturing and power generation. PSC Crane & Rigging also offers gantry rental for certified operators.

NessCampbell Crane + Rigging
The NessCampbell Crane + Rigging team recently tackled a complex project with precision and innovation, according to President John Anderson. The team provided a tailored rolling gantry solution to dismantle steel framework for concrete forms.
“Tasked with removing large sections efficiently, we deployed our 400-ton Lift Systems 44A hydraulic gantry and a six-line Goldhofer trailer on the Seattle Waterfront,” Anderson said. “The confined space and challenging maneuverability demanded a specialized approach, and our solution not only met but exceeded expectations, significantly reducing job time.”
Founded in 1947, NessCampbell Crane + Rigging serves clients and communities in Oregon, Washington and Idaho. From its eight locations across the Northwest, the company provides crane rental and services as well as specialized transportation rigging, machinery moving and engineering services.
Phoenix Machinery Movers unloaded a 2,000-ton Nidec stamping press crown from a 19-axle trailer using its newest gantry, the 350-ton capacity J&R Engineering Lift-N-Lock 700 series. The new gantry was instrumental in making the unloading process smooth and safe, the company said.
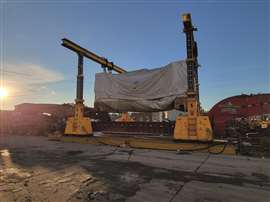
Phoenix Machinery Movers
The crown, which weighed 340,000 pounds, was unloaded outdoors in very cold conditions, typical for January in Michigan. It was transferred inside the building through a wall opening where it was unpacked and set in its final location.
The job was for a long-standing Phoenix Machinery Movers customer Motor City Stamping, based in metro Detroit, MI.
“Based in Shelby Township, MI, Phoenix Machinery Movers and Industrial Contractors provides comprehensive rigging solutions and expert project management,” the company said. “Our experienced machinery movers are committed to providing comprehensive support for your relocation requirements, whether it’s a single machine or an entire plant, according to the company. Phoenix provides a broad range of commercial and industrial contractor services for local, national and international companies.”
Dearborn Companies
Dearborn Companies recently participated in the successful design and engineering of a complex lift operation in Chicago. La Grange Crane Services contracted with Dearborn Companies to provide engineering expertise.
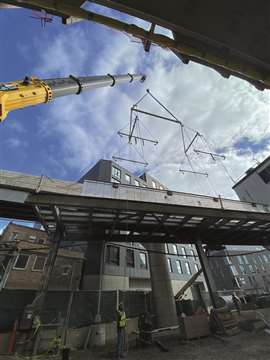
The project was part of the Chicago Transit Authority Red and Purple Modernization (CTA-RPM) project, in which the Walsh-Fluor J.V. self-performed operations. The task was to hoist and lower a retired relay house onto a transporter, a job requiring the skilled efforts of Ironworkers from Local 1.
The project presented several engineering challenges, primarily due to the relay house’s location between two live elevated train tracks with only 31 inches of lateral clearance, creating a unique spatial challenge. The operation demanded exact timing to maintain uninterrupted train schedules, requiring the lift to be executed in the brief intervals between train passings. The total load and center of gravity were meticulously estimated and analyzed to ensure the lift’s safety and stability. The Dearborn Companies team also conducted an engineered analysis of the lifting lugs on the relay house to determine the maximum vertical force allowable, utilizing digital load links to monitor the load in real-time and to prevent overload.
Optimizing rigging angles was crucial to maintaining forces within safe limits. Despite the intricate nature of the rigging equipment provided by LGH USA, the rigging team ensured the operation’s safety and efficiency. A complicated spreader bar system using Modulift beams was designed to lift, hoist and lower the relay house onto the transporter.
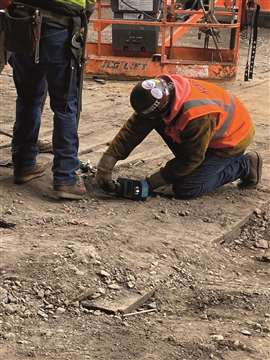
Coming off the hook of the Grove GMK 7550 was a Mod110H. The top rigging for that beam was a static sling on one side and a hand chain fall on the other side. On the bottom shackle of each side of the Mod110H were Mod50s. The top rigging for those also had a static sling on one side and a hand chain fall on the other side. On the bottom shackle of each side of the Mod50s were Mod24s. The top rigging for those were all hand chain falls. On the bottom shackle of each side of the Mod24s were 8-ton sheave blocks. Three-quarter-inch wire rope was attached to each lug that was reaved though the blocks under each Mod24, then connected back down into an adjacent lug. Digital scales were used coupled within the wire rope to measure the forces.
Achieving precision in crane placement and ensuring its stability required detailed engineering from Dearborn Companies, including considerations for pad and other site-specific factors at the jobsite.
“This operation showcased Dearborn Companies’ leadership in engineering and highlights the incredible results achievable through collaborative effort and expert partnership,” said Patrick Clark, director of business development for Dearborn. “We extend our heartfelt thanks to La Grange Crane and all our partners for their trust and cooperation in this complex endeavor, including Walsh-Fluor JV., and their customer, the CTA.”
Based in Bridgeview, IL, Dearborn Companies is an experienced civil and structural engineering firm that caters to a range of industries. The company provides ground condition and ground stabilization engineering, 3D mapping of underground utilities, 3D documentation, tower crane foundations and tiebacks, engineered lift planning, third-party lift planning review and engineered oversized/overweight transportation studies.
STAY CONNECTED
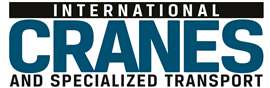
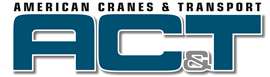
Receive the information you need when you need it through our world-leading magazines, newsletters and daily briefings.
CONNECT WITH THE TEAM
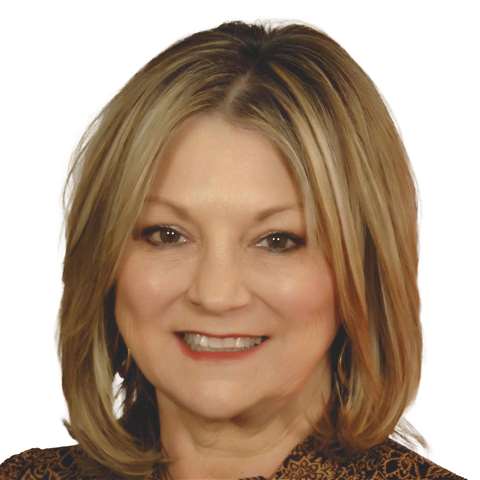
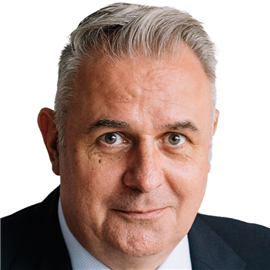
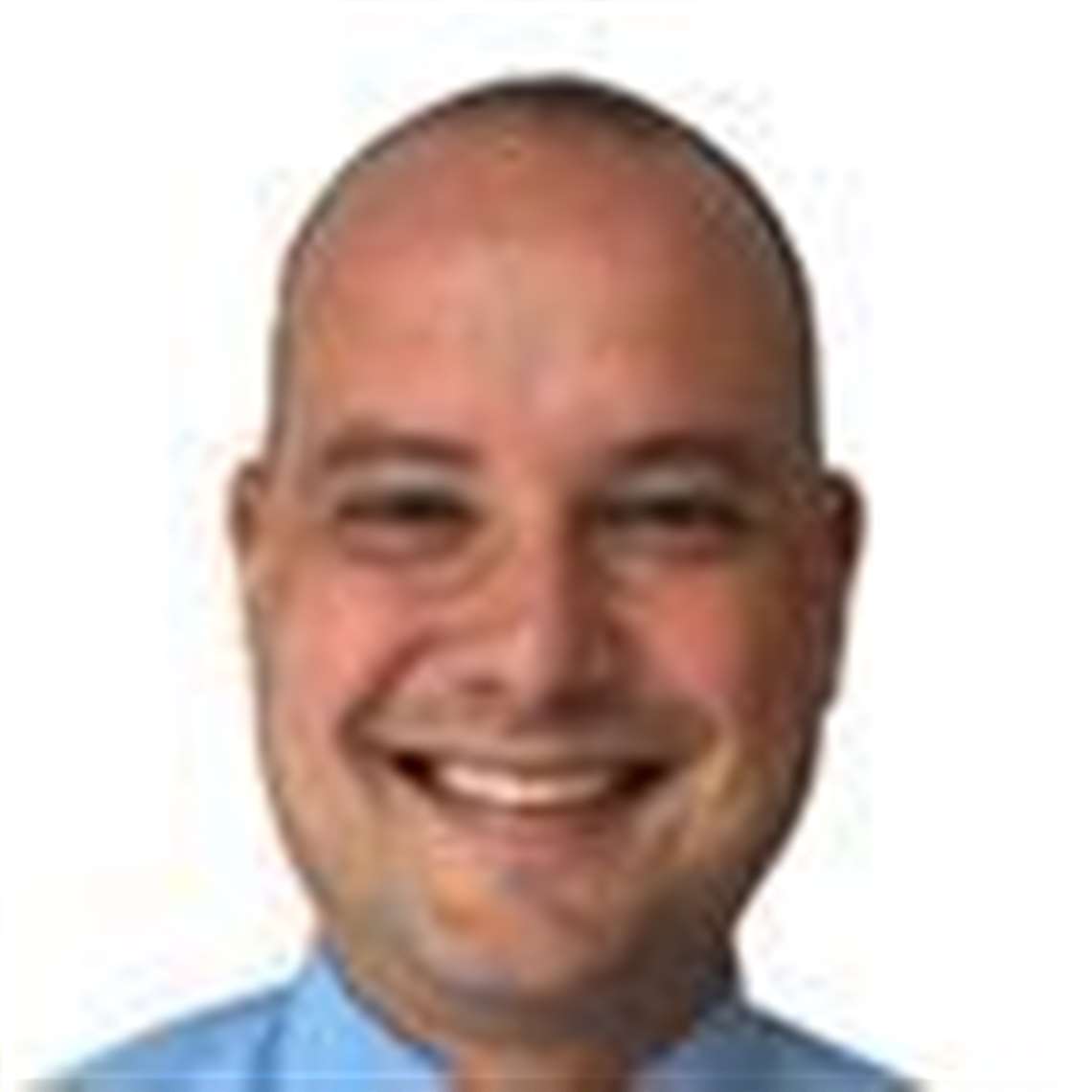
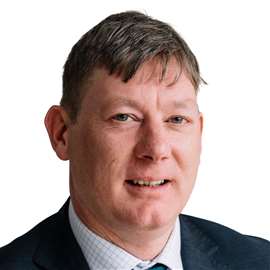