Read this article in French German Italian Portuguese Spanish
Hooked on: below the hook developments
24 July 2025
Developments in below the hook equipment are improving the safety and efficiency of increasingly complex and heavy lifting work. Niamh Marriott reports
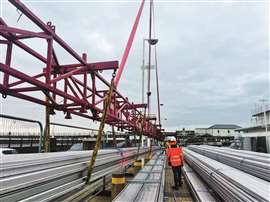
Netherlands-based family-run equipment manufacturer Bomecon cares about its people, proper engineering design and providing solutions for a whole range of industries.
I went to visit the company at its site in Nijkerk in the Netherlands to find out more. Bomecon offers standard products with modular options to best suit each lifting requirement a company might be tasked with. The company also works with companies to design, engineer and manufacture bespoke and custom equipment.
From spreader beams to the unique balancer range, the focus is on ensuring loads are properly balanced and can be manoeuvred into place despite site challenges or restrictions.
Their equipment has been used far and wide on a whole load of different global projects. From pre fabricated elements being lifted onto new multi storey construction builds in the UK, to replacing glazing on a ship in Singapore and lifting giant wind turbines at offshore farms.
By way of a partnership with Vita Inclinata the load stabilisation solution can be incorporated with lifting beams.
Bomecon owner and general manager Sabine van den Bor showed me around the production site, explaining the manufacturing process and highlighting some recent projects of note, including the renovation of the old BBC building in London, UK, and a construction job in Dubai.
Curious to know more about the Balancer range, I spoke to Martijn van den Bor, owner and operations manager, about the design and use cases for this specific below the hook device.
Let’s talk about the spreader beam and the balancer. You’ve got two types – 2D and 4D. Why both?
“The 2D balancer uses hydraulic cylinders and was designed to be compact – only 22 centimetres thick,” he explains. “That allows it to fit very close to facades without interfering with flooring, which is ideal for wood buildings with panels 26 to 32 centimetres thick. The chain runs over a wheel connected to the cylinder, which moves in and out to adjust the balance.”
And the 4D?
“The 4D version is more advanced. One part remains static, and the other moves. You can fully control all four points independently. In one case, we had a nine-metre-wide balcony panel that needed to slide over pre-installed I-beams, with just two centimetres of clearance. The architect didn’t want any visible lifting points on top, so we had to find an alternative solution. Using the 4D balancer, we were able to level the panel in all directions - forward, backward, side-to-side – in just 90 seconds.”
Maintenance and longevity
“Everything is tested prior to going out to market,” Martijn explains. Full overhauls are typically carried out every eight years but yearly inspections and maintenance are standard.
“We take all the outside off and we check the insides every year,” he says. While not every inspection involves load testing – “because that’s also getting close to breaking the machine” – visual checks are key. “If the paint is still correctly on, you’re good. But if you see little cuts, too much stress, then we remove the paint and see what’s underneath.”
Battery-powered components and hydraulics receive more frequent attention. “You change some oils, change some valves, always check the machines, especially the hydraulic and electronic compartments,” he says. Upon return from use, machines are stripped, cleaned, greased, and checked as standard procedure. “It’s high quality, high standards,” he affirms.
Ease of use and customer training
Not every component is plug-and-play. “If you have a lifting beam that’s not adjustable, then there’s only one way to use it,” he says. But more complex components, like the 4D balancer with remote controls, require training. “We do a half-day training with the crew. We want at least three or four people trained, including the supervisor,” he adds.
After training, they complete a document to confirm the user understands proper usage, load limits, charging routines, and safe parking. “In the UK I think they call that familiarisation,” he adds. “It’s more done with the remote-controlled, battery-powered machines than with, let’s say, metal wall beams.”
We are starting to see a few other similar products on the market to the balancer. What makes your product better than your competitors’? Why would somebody choose a Bomecon balancer over another product?
“I know the products. One of them started by using our machine and developed it differently,” he says. “But I’ve seen products with loose cylinders and hoses on the outside. If you break it while standing there – it’s more dangerous.”
In contrast, these machines are built robustly, with components safely housed internally. “You don’t see the cylinders, you don’t see the hydraulic hoses. It’s quite difficult to break anything,” he explains. The balancer also allows precise adjustment via remote control, switching between cylinders as needed, something he hasn’t seen in competing products.
He admits the machine may appear bulky at first glance. “I’m also an honest person. If I look at the other side, our machine is a little bit more big. The first time you look at it, you think, whoa. But when it’s hanging on a crane hook, you don’t notice anymore. Then they say, ‘Oh, this is going very smooth.’”
To be custom and bespoke isn’t something everyone can do – especially in below the-hook equipment. Would you agree that’s an advantage?
“Yes, although on the other hand, we try to get it as standard as possible. That’s what the brochure is for – we try to explain that clearly. People can see with the clear load tables what they can do, what they can choose. They already start thinking about it themselves a bit.
“But still, we like to ask: What do you want to do with it?”
With 22 years of experience, he’s seen a shift. “Now we’ve got customers who know what they want. That’s a good balance – between long-standing clients and new ones who have no clue.”
A standout project?
One recent bespoke build was for Amsterdam Schiphol airport in the Netherlands, about 30 minutes from their site.
“They had to remove filters from a building next to the runway, with planes and trolleys moving nearby,” he recalls. The team created a compact truck crane system with a roof and safety barriers, allowing workers to operate safely without harnesses.
The job stretched along a 450 metre building, and they repurposed reels from a glass washing system to make it work. “It wasn’t even comparable to anything in our programme,” he says. “They asked, ‘Could you do that?’ I said, ‘I think we can.’”
They pitched the idea after 40 hours of engineering. “We showed them the big lines, and they said, ‘Alright, start building it.’”
Final thoughts – engineering-led, project-driven?
For Martijn, it’s the emphasis on engineering that makes the difference. “These aren’t quick products. The engineering’s a really important part of it,” he says. “Even connecting parts has its own challenges. Every project is different.”
He gestures around the building, emphasising the extensive range of products, technology and the engineering team: “We try to work with our big toolbox.”
Range improvements
Camlok, a Columbus McKinnon brand, recently added to its range of below the hook equipment with several developments designed to meet evolving industry demands for safety, versatility, and modularity.
Its latest developments include enhancements to the CY Series hinged vertical plate clamps, which now feature “hinged hook rings for improved gripping pressure across lifting angles,” along with “quick and secure locking mechanisms” and “service-friendly construction for easy maintenance and part replacement.”
The LJ Series of non-marking clamps has also been expanded and are now available with rubber or leather-lined pads for damage-free handling of stainless steel, aluminium, and other sensitive materials.
The company says Camlok clamps are recognised for their “robust British engineering, ease of repair, and availability of spare parts”, making them a cost-efficient choice in the long term. All products are fully compliant with Loler, EN 13155, and ASME B30.20 standards and include “clearly marked WLL and jaw capacities, […] positive tension jaw springs, and […] safety latches and locking levers.”
As part of its digital integration efforts, Camlok is also adding QR codes directly onto products, providing instant access to manuals, safety instructions, and inspection checklists.
With increasing demand for adaptable solutions, Camlok’s wide jaw TAG and TWG clamps now offer “quick-open levers, interchangeable pads, and compact designs for confined spaces.” The company says its lighter, ergonomic models like the HGC hand grip clamps and TPZ board clamps, are helping to reduce operator strain while maintaining high safety standards.
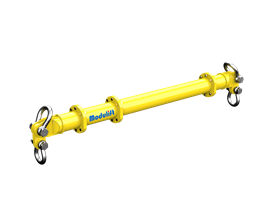
Partner up
Several partnership and distribution agreements have been announced this year.
Pewag brands Load Monitoring Systems and Modulift have appointed Westcon Løfteteknikk (WCL) as an official distributor in Norway, marking a milestone in global expansion. The announcement supports Pewag’s Stronger Together strategy, uniting its lifting brands under one roof to serve global markets with below-the-hook products.
“This is a natural evolution of an already strong partnership,” says Thomas Dietvorst, segment manager lifting solutions at Pewag.
“Westcon Løfteteknikk has consistently demonstrated technical competence, market insight and a customer-first approach. As a global distributor of LMS and Modulift, they are ideally placed to support Norwegian clients with innovative products, fast delivery, and local expertise.”
As part of the expansion Westcon Løfteteknikk holds stock of LMS load cells and Modulift spreader beams, ready for immediate rental or purchase in Norway. The equipment pool includes 6.5 tonne – 55 tonne load cells together with MOD 6, MOD 12, MOD 24, MOD 34 and MOD 50 spreader beams.
The company says spreader beams ensure safe load distribution, while load cells provide real-time monitoring to mitigate overload risks and support regulatory compliance. “We’ve worked closely with LMS and Modulift for many years,” says Tommy Nilsen, sales and marketing director at Westcon Løfteteknikk. “Becoming official distributors simply strengthens our ability to respond faster to our customers.”
Calibration
Together with an enhanced equipment pool, Westcon Løfteteknikk is investing in an LMS high-precision calibration machine. Capable of calibrating tension load cells ranging from 3.25 to 55 tonnes with an accuracy of ±0.05 per cent, this facility will enable Westcon Løfteteknikk to offer full in-house calibration services by the end of 2025.
“Bringing calibration in-house is a game-changer for our customers,” says Nilsen. “It means reduced downtime, fewer transport costs and a faster service for our Norwegian client base.”
Level lift
UK-based specialist lifting provider GGR Group is now an official UK distributor for levelling yoke manufacturer Ganterud. This new partnership expands GGR Group’s product portfolio with load levelling technology, available to UK customers for both rental and purchase.
When lifting heavy, imbalanced, or irregularly shaped loads, precision and control are critical. Ganterud’s innovative levelling yokes, also known as lifting yokes, are designed to maintain load stability by enabling operators to adjust the centre of gravity at the touch of a button. These tools are designed for safe handling of items such as precast concrete elements, stair units, and steel structures.
Graeme Riley, GGR Group CEO, says, “We’re always looking for ways to help our customers work more safely and efficiently. The addition of Ganterud levelling yokes provides a practical solution for complex lifts, ensuring greater control and reducing time spent on crane operations.”
GGR Group now offers five models from the Ganterud range, each engineered to meet specific lifting challenges. Each one has wireless remote control (100 metre range), weather-resistant casings (IP65/IP67 rated), and rugged, low-maintenance designs, making them ideal for demanding site conditions across construction and industrial sectors.
STAY CONNECTED
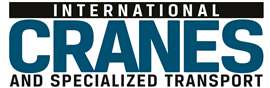
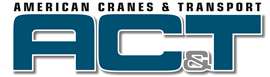
Receive the information you need when you need it through our world-leading magazines, newsletters and daily briefings.
CONNECT WITH THE TEAM
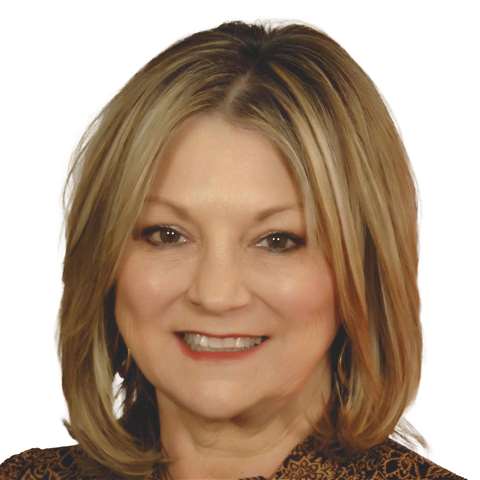
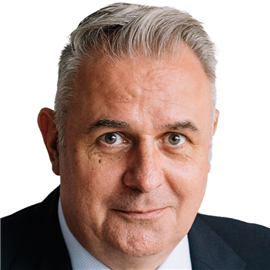
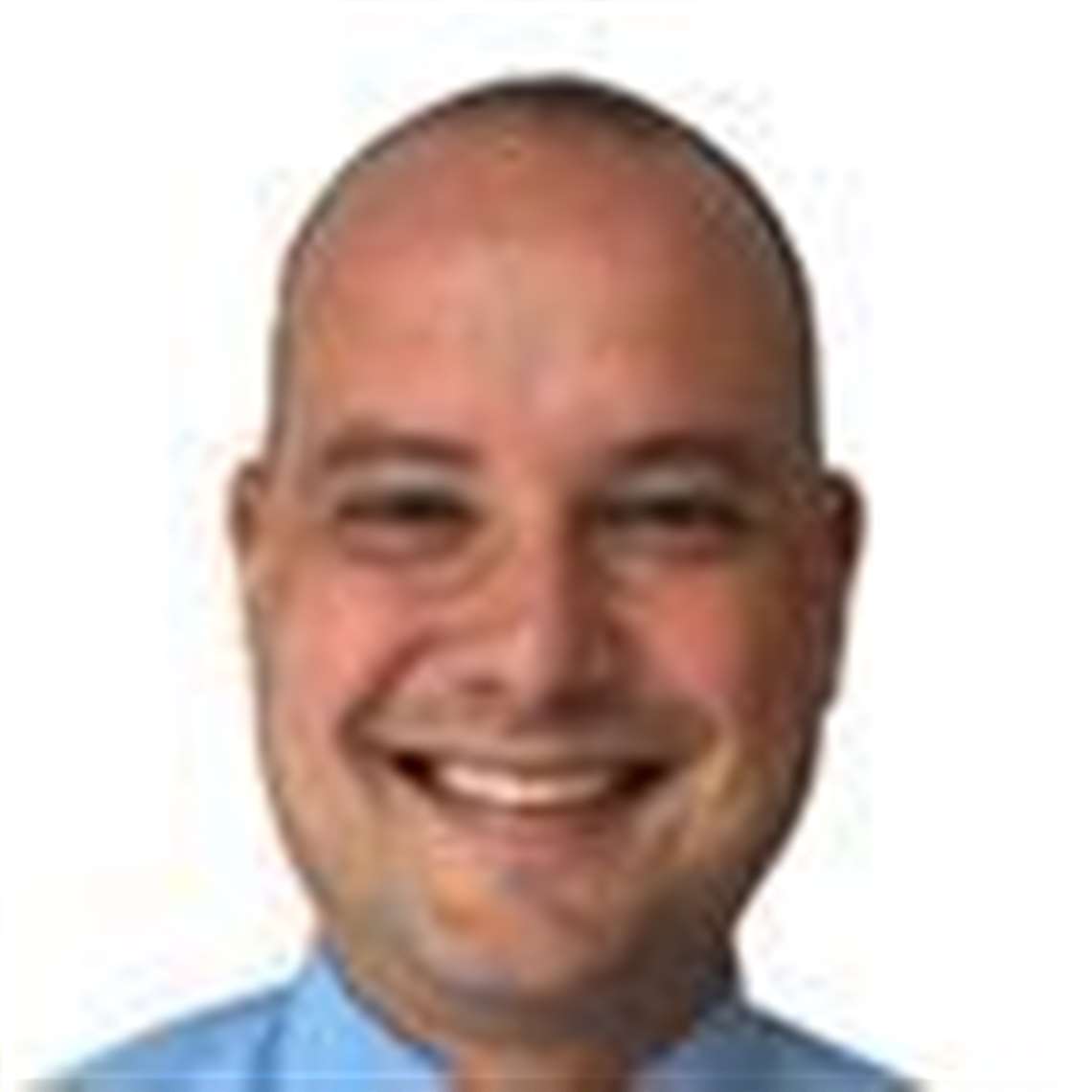
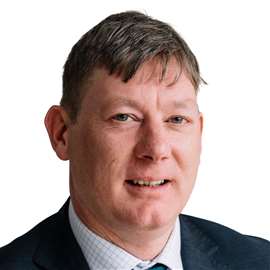