Read this article in French German Italian Portuguese Spanish
Super size trio: moving 3,600 tonne compressors
12 March 2025
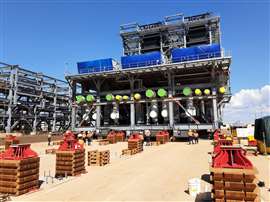
Manoeuvring and jacking down a trio of enormous compressors, each weighing 3,600 tonnes, was no mean feat on a project in Australia.
A synchronous jacking system was selected for the jack down by contractor Alevro, a joint-venture company between Italian heavy lift and transport specialist Fagioli and Australian engineering specialist Monadelphous.
Alevro chose to use an Enerpac EVO system for the project at the Pluto LNG onshore facility near Karratha in Western Australia. The giant compressors are used to make the liquefied natural gas (LNG) by compressing and condensing mainly methane gas to around minus 160 degrees centigrade, turning it into a liquid.
Pluto Train 2 will process natural gas from the Scarborough field in the Carnarvon Basin, around 375 km off the coast of Western Australia. When up and running it will have an annual production capacity of around 5 million tonnes of LNG.
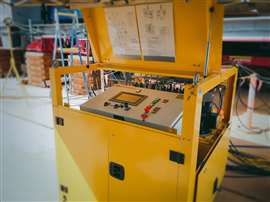
First stage
Before installing the compressors, however, the company first had to transport them from the quayside using self propelled modular transporter (SPMT).
With the compressor transported in over its final position the next stage of the job could begin. With the SPMT out of the way the compressors could be lowered onto the foundations using the Enerpac EVO System.
In addition to their huge weight, the compressors were also large, measuring 63 metres long by 30 wide and standing 30 metres tall. This meant pre-planning was critical to the success of the project.
The site was prepared with a ground level concrete slab and an array of anchor points. A total of 44 Enerpac climbing jacks were carefully placed in a pre-determined arrangement. Each stack stood at 1.2 metres. The stacks were topped by 500 mm of climbing jack frames, each holding 250 tonne Enerpac 250T jacks.
For the jack-down process everything was done using two Enerpac EVO power packs. Each one operated 24 jacks on 12 hydraulic lines. The power requirement was a manageable 7.5 kw.
Careful design
To avoid hitting the module structure, a specially tailored design was created for the jacking frames. “Our first task was to perform the load-in operation of the compressor module via SPMT transfer and then transporting it from the quayside to the prepared on-site foundations which involved 168 axle lines of SPMT and eight power packs,” said Tomasz Milewski, Alevro engineering manager.
Massimiliano Vettrici, Alevro operations manager, was in charge of running the overall operation. “Testing the jack-down system was crucial in building confidence for the next stage of the compressor installation, where the Enerpac cylinders would bear the full weight of the compressor module. Additionally, we paid particular attention to module alignment while on SPMT, as we did not anticipate any movement during the lowering phase, given the numerous jacking points.
“The load transfer from SPMT to climbing jacks utilised the Enerpac EVO ‘tilting mode’ to align the module with its behaviour onto the SPMTs’ hydraulic bed. The entire jack-down operation, using the Enerpac climbing jacks and EVO systems, went very smoothly. The successful installation of all compressor modules has now established the framework for future jack-downs,” concluded Vettrici.
Alevro’s methodology and creative execution was recognised at the Crane Industry Council of Australia (CICA) Awards. The jack-down operation was awarded Best Innovation by the CICA judges and took the People’s Choice for innovation award.
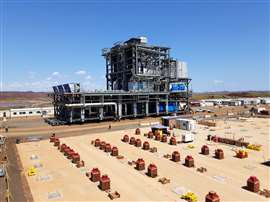
STAY CONNECTED
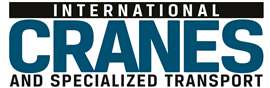
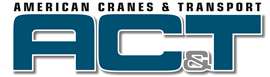
Receive the information you need when you need it through our world-leading magazines, newsletters and daily briefings.
CONNECT WITH THE TEAM
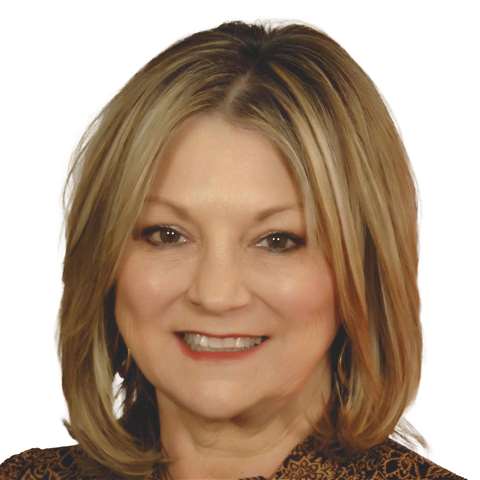
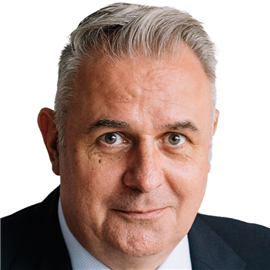
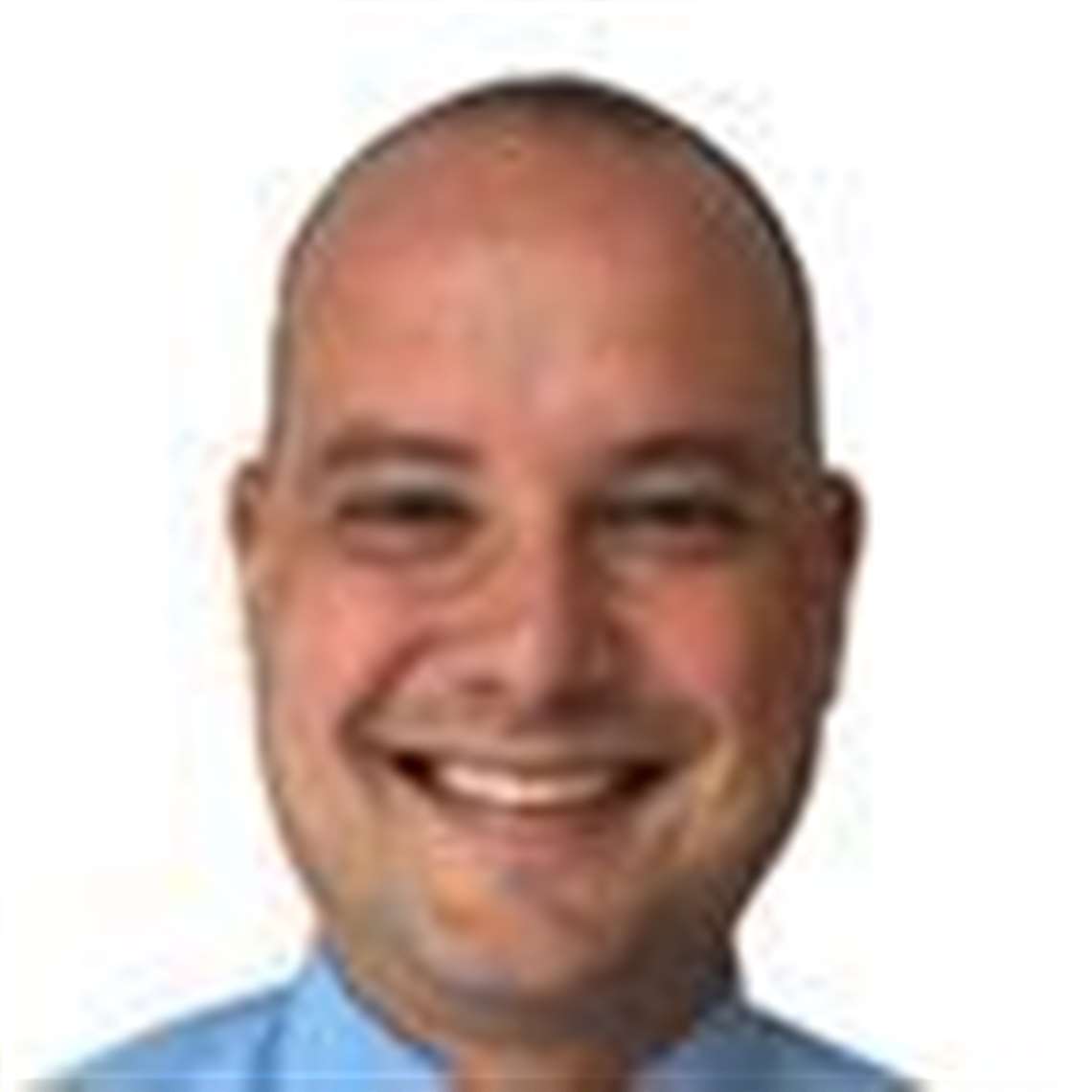
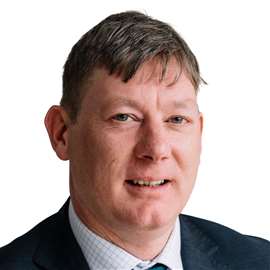