Read this article in French German Italian Portuguese Spanish
Energy sector lifting and transport
09 July 2025
From wind farms to nuclear plants, building the future of energy relies on specialist cranes and heavy transport to lift, shift and install critical infrastructure. Niamh Marriott reports.
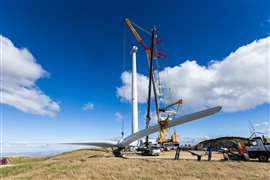
Though there is also still a considerable continued investment in oil & gas, and nuclear power, the energy sector is undergoing a sizeable change. There is a strong global push towards renewables, especially wind power.
This greener landscape is driving demand for highly specialized lifting and transport solutions. As renewable projects scale up in size and complexity, and conventional energy infrastructure demands heavier and more precise installation, the role of expert lifting and transport providers is more central than ever.
Manufacturers like Liebherr are supplying crawler and tower cranes tailored for wind turbine assembly and modular nuclear builds, while heavy lift giants Sarens and Mammoet are deploying self propelled modular transporter (SPMT) and bespoke lifting and jacking systems to move transformers, reactor components and offshore platform modules with millimetre precision.
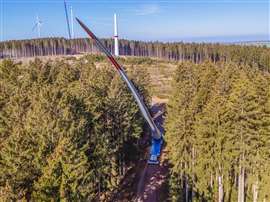
Wind work
Wind power, particularly with new offshore wind farms, is leading the charge as the energy sector continues its global pivot towards renewables. In response, the lifting and transport industry is stepping up to meet the scale and complexity of new infrastructure demands.
A potential obstacle for new wind farms in the USA is President Trump’s executive order temporarily halting offshore wind lease sales in federal waters and pausing the approvals, permits and loans for both onshore and offshore wind projects. Elsewhere however, new wind farms are being planned and built.
Crane manufacturers continue to produce cranes for taller and heavier wind turbine components. “As OEMs introduce new turbine models, increasing hub heights require larger crawler cranes for onshore turbine erection,” says Buckner HeavyLift’s Brian Miller. “The Liebherr LR 11000 has become the preferred choice, as it can efficiently install wind turbines with hub heights up to 120 metres without the need for a derrick, streamlining mobilisation, pad-to-pad relocation and reducing setup time.”
It’s not just cranes that are proving popular, as demand for SPMT continues to rise. Heavy lift equipment provider NXGEN expanded its fleet with an additional 100 axle lines of Scheuerle SPMT.
Japanese transport and lifting specialist contractor Denzai also added a total of 48 lines of SPMT to its equipment fleet. That deal is for eight modules of German manufacturer Goldhofer’s PST-ES-E (315), each with 6-axle lines. Denzai says it will use the new equipment for offshore wind energy generation construction projects with delivery scheduled in early 2026.
Huge load
The recent loadout of the 23,120 tonne B212-Charybdis offshore wind turbine installation jack-up vessel by lifting and heavy transport specialist Fagioli highlights the rising scale of specialized transport in the energy sector. Built in Texas, USA, the project required 880 axle lines of Scheuerle SPMTs, 28 power packs, three semi-submersible barges from Norway, plus tugboats and spacer barges to handle the vessel’s immense size.
While the project did break three world records, what stands out is the orchestration of technology and expertise necessary to handle the vessel’s size and configuration, highlighting how offshore wind demands are reshaping the lifting and transport landscape.
The growing dimensions of offshore wind vessels pose engineering challenges, especially in US shipyards not traditionally geared for such scale.
Factors like the port’s low 2.74m dock height and the vessel’s challenging weight distribution demanded precise planning and innovation.
Global collaboration
Global collaboration was essential, with Fagioli coordinating equipment fleets across Europe, Asia, and the USA, integrating hydraulic and electronic systems into one remote-control command to move the vessel safely. The port was closed for 72 hours to manage tide cycles, weather, and traffic during the loadout.
Even once positioned, the vessel’s jack-up legs had to be deployed into the water before its weight could be fully transferred. The load transfer was completed successfully, and the port reopened ahead of schedule.
This kind of complex operation is becoming more common as the energy industry pushes further into offshore wind and other renewable infrastructure.
Offshore operations
Elsewhere in the world, heavy lift giant Mammoet recently worked on the loadout of a 3,050 tonne topside and 3,150 tonne jacket for the N05-A platform, the first offshore gas platform in the Dutch North Sea powered entirely by wind from the nearby 113.4 MW Riffgat offshore wind farm.
This electrification is expected to reduce carbon emissions by over 85 per cent.
Part of the GEMS project on the Netherlands-Germany border, Mammoet supported assembly and transport at HSM Offshore’s Rotterdam facility using mobile cranes, sheerlegs, and SPMT.
A key challenge was loading both large structures onto the same barge, an unusual approach to shorten the schedule, which required complex engineering and a spud leg barge for mooring due to the combined heavy loads. The loadout was completed in two days using four 32 axle lines of SPMT.
Mammoet’s involvement demonstrate how specialized heavy transport supports the growth of renewable and low-carbon offshore energy infrastructure.
Power shift
Mammoet has also been selected as a key contractor by SeAH Wind. It will provide SPMT for the Hornsea 3 Offshore Wind Project. SeAH Wind will supply monopile foundations to the wind farm for installation approximately 120 kilometres off the Norfolk Coast in the North Sea. On completion it will be the world’s largest offshore wind farm, the company says.
With commercial production to start in the coming months, these subcontractors were selected to support the operational and logistical services on the 120 acre site.
Darren Watson, Mammoet sales manager, says, “We are delighted to be helping SeAH Wind to deliver the future of offshore wind foundations by providing marshalling capabilities that are constantly at the cutting edge of what can be lifted and transported.”
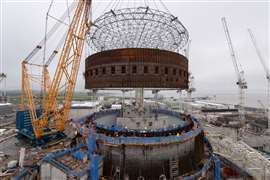
Nuclear work
With nuclear infrastructure experiencing a resurgence as part of the global drive for low-carbon energy, major construction projects like Hinkley Point C nuclear station in the UK are pushing the limits of heavy lifting and precision engineering.
Late last year, Sarens’ 5,000 tonne capacity SGC-250 ‘Big Carl’ crane lifted a 423 tonne steel ring into place - the third and final liner ring for the second reactor building. Measuring 47 metres in diameter and 11.6 metres high, the ring forms part of the inner containment wall and includes mountings for a polar crane used in refuelling.
The steel dome for this reactor building will be installed this year, following the approach used on the first reactor, which saw its dome placed in December 2023.
Oil and gas
Sarens also continues to support major oil and gas projects, recently providing heavy haulage solutions for developments in Indonesia. These projects include the West Belut development, the Sisi Nubi AOI Project (Packages A & B), and the Terubuk L & M fields, which play a significant role in boosting Indonesia’s oil and gas production, demonstrating the demand for oil and gas remains high.
The company has collaborated on high-profile projects such as Saudi Aramco’s Marjan Field in the Middle East, Pertamina’s refinery upgrades in Balikpapan, and Qatar Energy’s North Field Oil projects.
The current scope of work, which began in June 2024 and continues through June 2025, takes place at the Meitech Eka Bintan yard. Sarens is using a variety of specialised equipment, including load cells ranging from 150 tonnes to 600 tonnes, and up to 56 SPMT axles with 4 PPUs. One of the most challenging lifts involves a jacket weighing 1,100 tonnes.
STAY CONNECTED
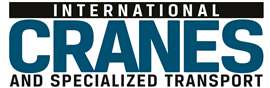
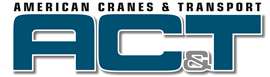
Receive the information you need when you need it through our world-leading magazines, newsletters and daily briefings.
CONNECT WITH THE TEAM
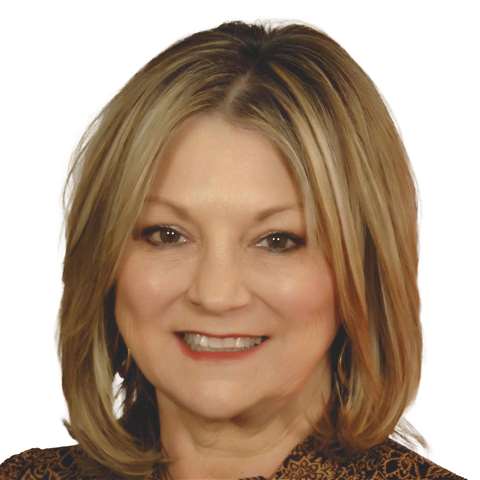
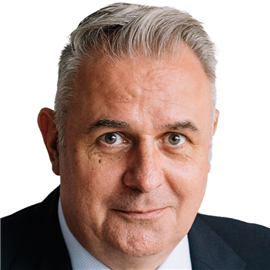
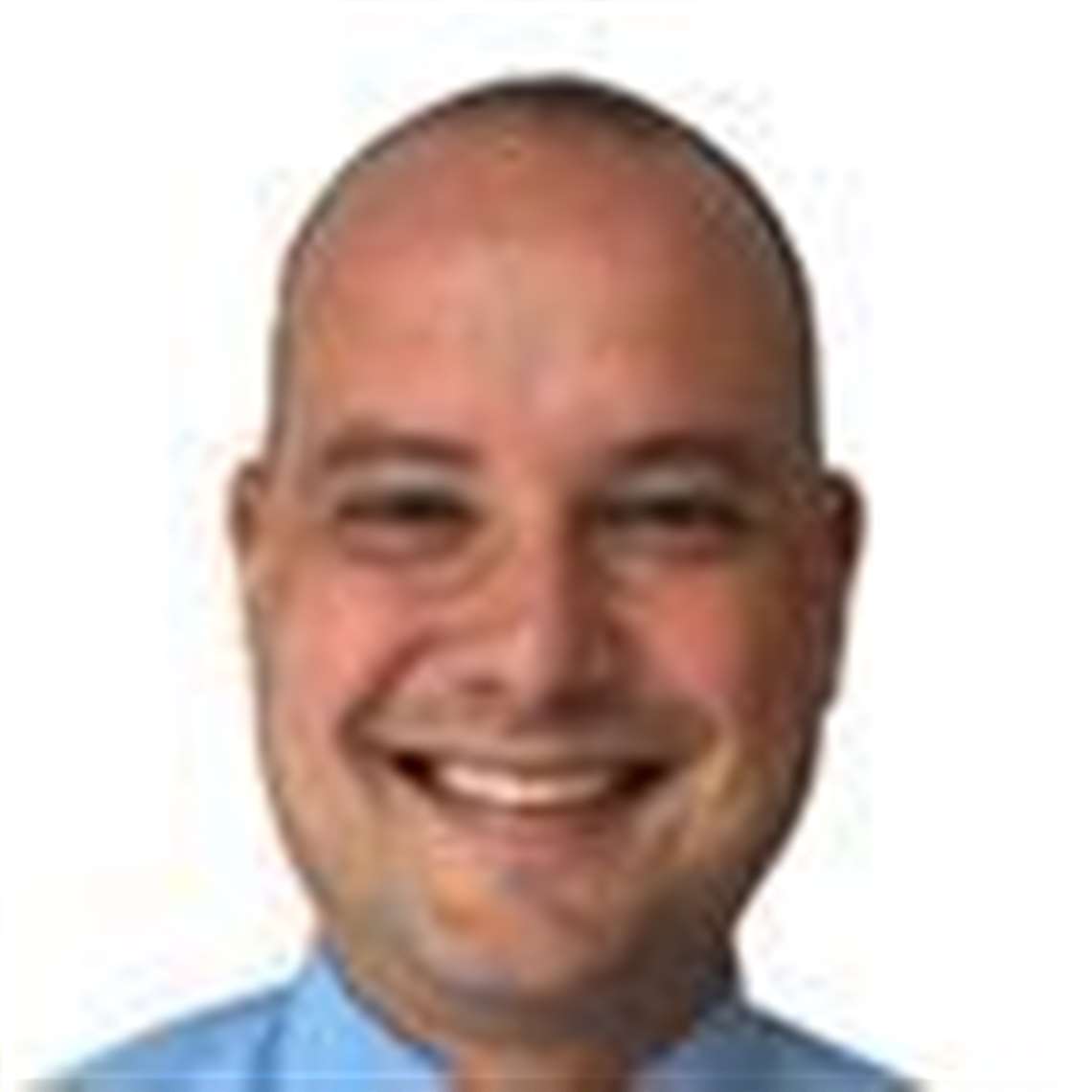
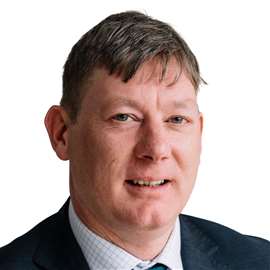