Read this article in French German Italian Portuguese Spanish
All terrain cranes: power, reach and hybrid lifting
15 July 2025
From extended booms to zero-emission operations, the latest all terrain cranes combine power, reach and sustainability to meet the demands of modern lifting. Niamh Marriott reports.
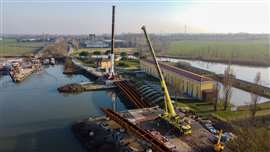
Blending the high speed road performance of a truck mounted crane with the off-road agility of a rough terrain crane, all terrain cranes are built for versatility.
Due to their all wheel steering, they can handle uneven ground on job sites with ease while still travelling on public roads. This crane type has between 2 and 12 axles and the largest have a capacity rating of 4,000 tonnes. Having said that, it might arguably be a misnomer to describe anything much bigger than about 400 tonnes as “all terrain” but the same technology continues all the way through.
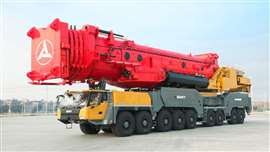
Several new models have been launched already this year and in the months before that. Back in September 2024, Link-Belt revealed its latest all terrain, the 200 tonne capacity 225|AT, which is the third in the company’s range of 5 axle ATs, and sits between its 150 tonne capacity 175|AT and the 275 tonne capacity 300|AT. The crane is now ready for delivery.
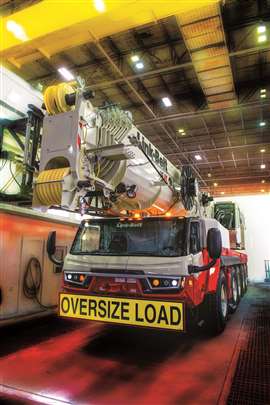
Smart testing
Designed, built and tested at Link-Belt’s factory in Lexington, Kentucky, USA, the new model was launched at the company’s CraneFest event.
It includes a 14 to 62 metre six section latching boom, a 13 to 22 metre two piece hydraulic offsetable SmartFly, a 2.4 metre heavy lift jib, one or two 7.6 metre lattice fly extensions, and a maximum tip height of 101.8 metres with full attachment.
Smart features include Link-Belt’s Pulse 2.0 operating system and its wireless rigging remote system. Its SmartStack counterweight detection and Variable Confined Area Lifting Capacities (V-CALC) system allow the crane to have a wide variety of outrigger configurations and ground bearing pressure readouts.
“We’re excited to add the 225|AT to our product offering,” says Andrew Soper, product manager for telescopic truck and all terrain cranes. “I’m personally thrilled for customers to experience this AT platform with its new features, improved capacities and superior transportability.”
Soper says the North American AT market is extremely competitive, with 11 models in the 111 to 150 tonne range, five models in the 151 to 219 tonne range, and nine models in the 220 to 300 tonne range.
The new crane was developed alongside the 300|AT, which was launched back in 2023 at the ConExpo trade show in Las Vegas, USA.
Improved reach
The 225|AT features improved reach, larger capacities and more counterweight than its predecessor, the 185 tonne ATC-3210.
With a modular design, the 225|AT includes up to 36 tonnes of counterweight. Power comes from a Cummins X15 diesel carrier engine but the company also says that the new model can be powered by hydrogenated vegetable oil (HVO), as it has a dual-tank system.
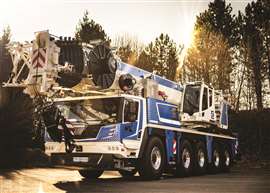
Electric options
There were several new models on show at Bauma 2025, the giant German trade fair back in April, including Liebherr’s latest.
The German manufacturer’s newest model is the LTM 1150-5.4E, a 150 tonne capacity wheeled mobile telescopic crane with both diesel and electric drive. This five axle crane includes a battery for autonomous, untethered operation and can also be plugged into the grid for charging and full power use. Its 400 kW diesel engine meets EU Stage V emissions standards and can also run on HVO, reducing CO₂ emissions by up to 90 per cent.
Running on electricity, it produces zero exhaust emissions at the point of use and is significantly quieter, Liebherr says.
The crane’s 111 kW electric motor is liquid cooled, high speed, and delivers nearly the same performance as the six cylinder diesel engine. It powers the pump transfer gearbox in the superstructure via a distributor gear.
The standard diesel version transmits drive mechanically through the slew ring into the superstructure, while the electric version uses the same driveline, switching between diesel-hydraulic and electro-hydraulic modes via a transfer gearbox.
Autonomous operation
The LTM 1150-5.4E builds on technology used in the compact Liebherr LTC 1050-3.1E, first introduced at Bauma back in 2022. Unlike its predecessor, the new 150 tonne model features a 1.5 tonne, 99 kWh battery pack with integrated charger, mounted at the rear.
This allows for autonomous operation of up to four hours without grid power. When connected, even a modest 16 or 32 Amp supply is sufficient for full operation, as the battery compensates for peak demand and charges simultaneously from the grid connection.
UK-based Emerson Crane Hire recently added four new cranes to its fleet, including three LTM 1150-5.4 models.
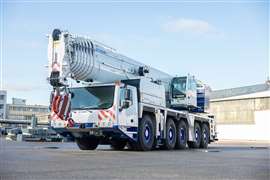
Extended reach
Also on show at Bauma was Japanese manufacturer Tadano’s new 250 tonne all terrain with a 79 metre main boom, the AC 5.250L-2.
Self erecting extensions are available from 5.8 to 30.0 metres. The overall system length is 109 metres, making it good for urban applications such as positioning heavy equipment over obstacles and assembling large tower cranes.
The crane delivers a maximum load moment of 736 tonne-metres and lifts 105 tonnes with a 13.5 metre main boom at a 7.0 metre working radius. An optional heavy lift attachment increases capacity to 138.7 tonnes.
Optimised for mobility, the AC 5.250L‑2 can be configured with 10 × 6 or 10 × 8 drive options on 406 mm steel wheels while meeting axle load limits for public road transport.
It has the IC‑1 Plus crane control system for real‑time load capacity monitoring. A Surround View camera system is available to assist with positioning the crane on site.
Power comes from a 396 kW (530 hp) Mercedes‑Benz diesel engine that complies with EU Stage V and US EPA Tier 4 Final exhaust emission standards. It has fuel‑saving functions such as an Eco Mode and a start-stop system.
Hybrid options
Manufacturer Manitowoc’s Grove showed a hybrid 5 axle all terrain crane at Bauma, which is available in two versions. The GMK5150L-1e (60 metre boom) and GMK5150XLe (68.7 metres) offer as much as a full day (five hours) of emissions-free lifting, the manufacturer says.
It has a fully electric upper works for crane operation. Loads charts are the same as for the diesel versions. The battery offers a capacity of 180 kW-h. Charging can be done by plugging the crane into a grid connection or from a 170 kW generator mounted onboard the crane in the carrier. The running time can be extended to around 20 hours when the crane is connected to the electricity grid via its cable.
Most of the driveline remains as per the diesel version, including the independent Megatrak suspension and disc-braked axles.
Power fuel
“These new plug-in hybrid cranes deliver more sustainable lifting and boost owners’ environmental credentials,” says Florian Peters, Manitowoc senior product manager for all terrain cranes.
“They can drive to the job site using HVO fuel to power the efficient Mercedes-Benz engine and reduce carbon emissions by up to 90 per cent while simultaneously charging the batteries. Then, they can set up and use clean electricity to handle the lifting tasks. There’s also a massive reduction in noise pollution – a great advantage when operating in a city centre.”
Fleet additions
Several companies in Europe expanded their fleets with Grove cranes. Poland’s Dźwigaj has added a GMK6300L-1, saying it made the choice due to positive past experiences with the brand. Spanish rental company Grúas del Vallés took delivery of two new 60 tonne GMK3060L-1 models, following a previous GMK3060L-1 purchase in 2022. Italy’s Baldini Group has added a 250 tonne GMK5250XL-1, one of the manufacturer’s largest models, to handle tower crane assembly, HVAC installations, industrial work, construction, and boat handling. Meanwhile, Polish crane rental company Karmax took delivery of a new GMK4100L-2 from dealer Zeppelin Polska, updating its fleet with the successor to its existing GMK4100L-1.
Load share
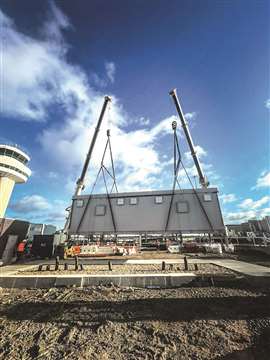
As part of a major engineering works projects, Southern Cranes and Access’ two Grove GMK5150XL all terrain cranes completed a tandem lift to install a 22 tonne substation at the UK’s London Gatwick Airport.
Clive Sadler, director, Southern Cranes and Access, explains, “We had to ensure all work was carried out below a 25 metre height so the airport would not have to suspend aircraft movements. Because the substation has eight lifting points, we would have needed an extra longitudinal spreader beam to lift with a single crane.
“So, it seemed logical to share the load between two cranes. We chose the GMK5150XL cranes because they can carry a large amount of counterweight (30.9 tonnes within a 16.5 tonne per-axle limit), meaning we only needed one support vehicle, saving us time and money.”
Working with the full 44.5 tonnes of counterweight, at a maximum radius of 22 metres, the substation was simultaneously lifted and positioned by both crane operators.
The cranes used Manitowoc’s onboard Crane Control System (CCS).
The on-site installation was completed in one day.
STAY CONNECTED
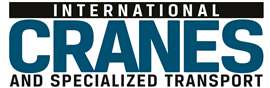
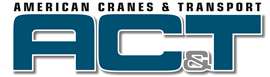
Receive the information you need when you need it through our world-leading magazines, newsletters and daily briefings.
CONNECT WITH THE TEAM
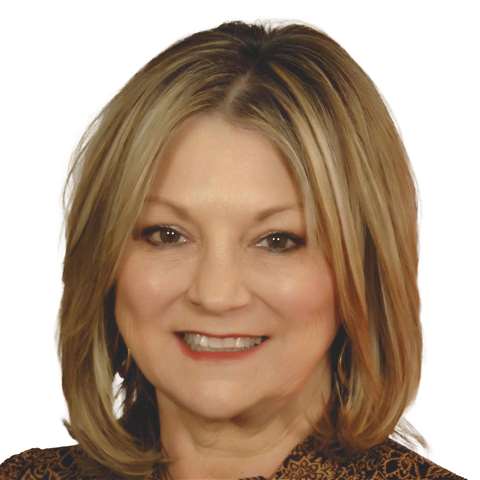
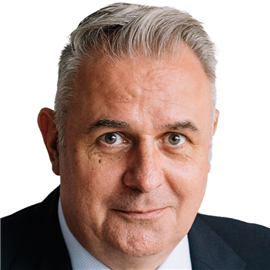
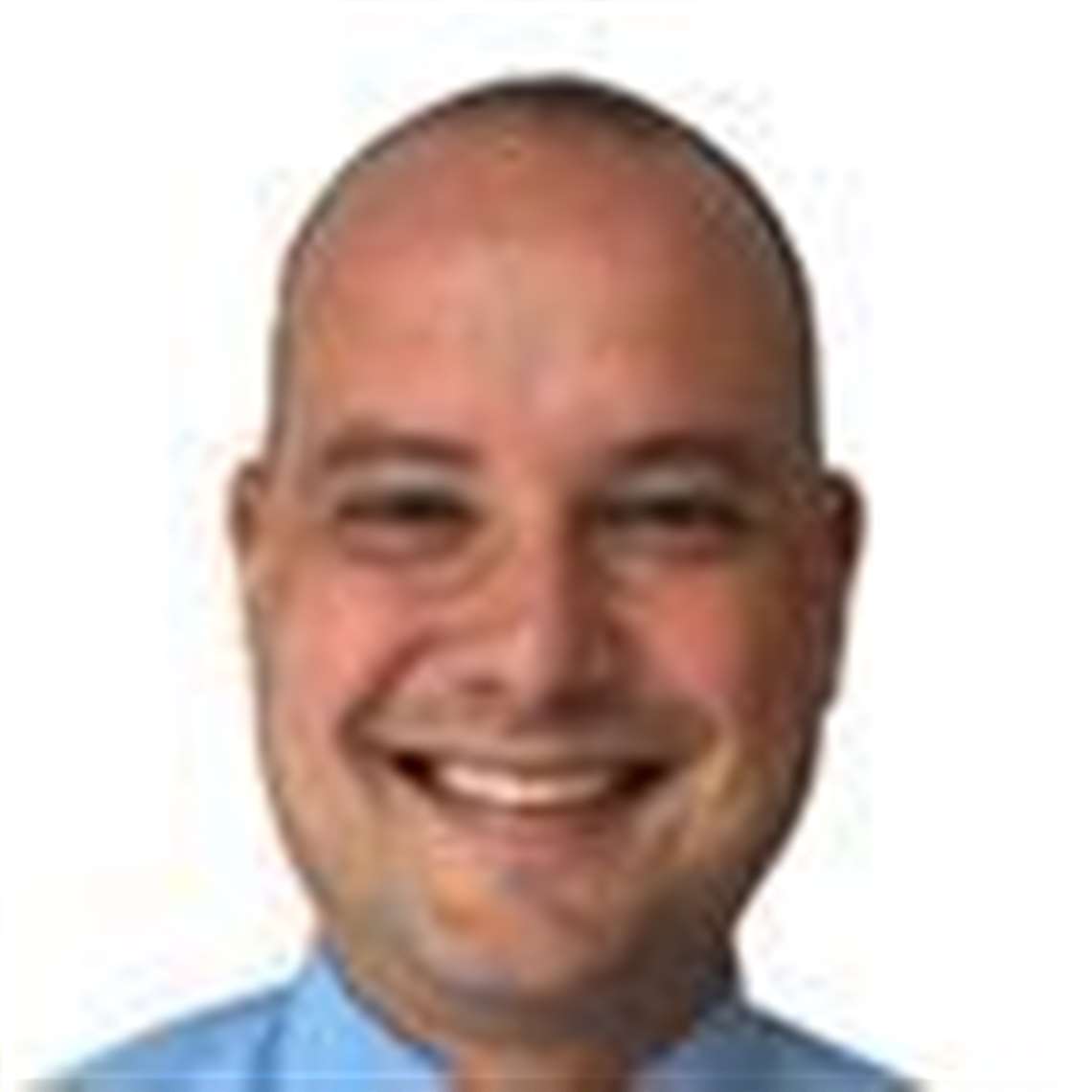
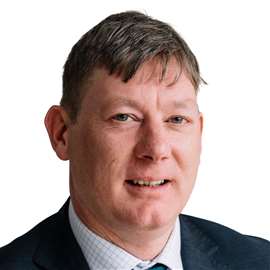